Home>diy>Building & Construction>What Is A Joist In Construction
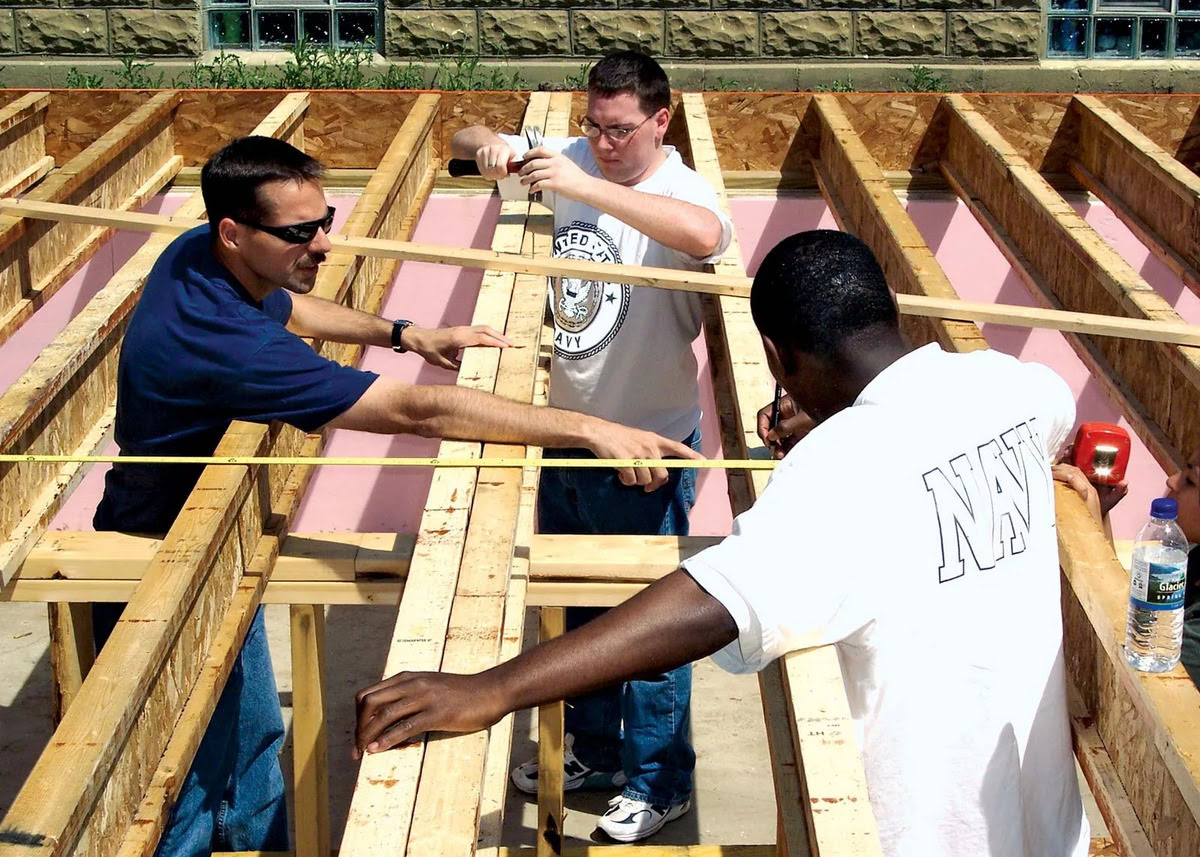
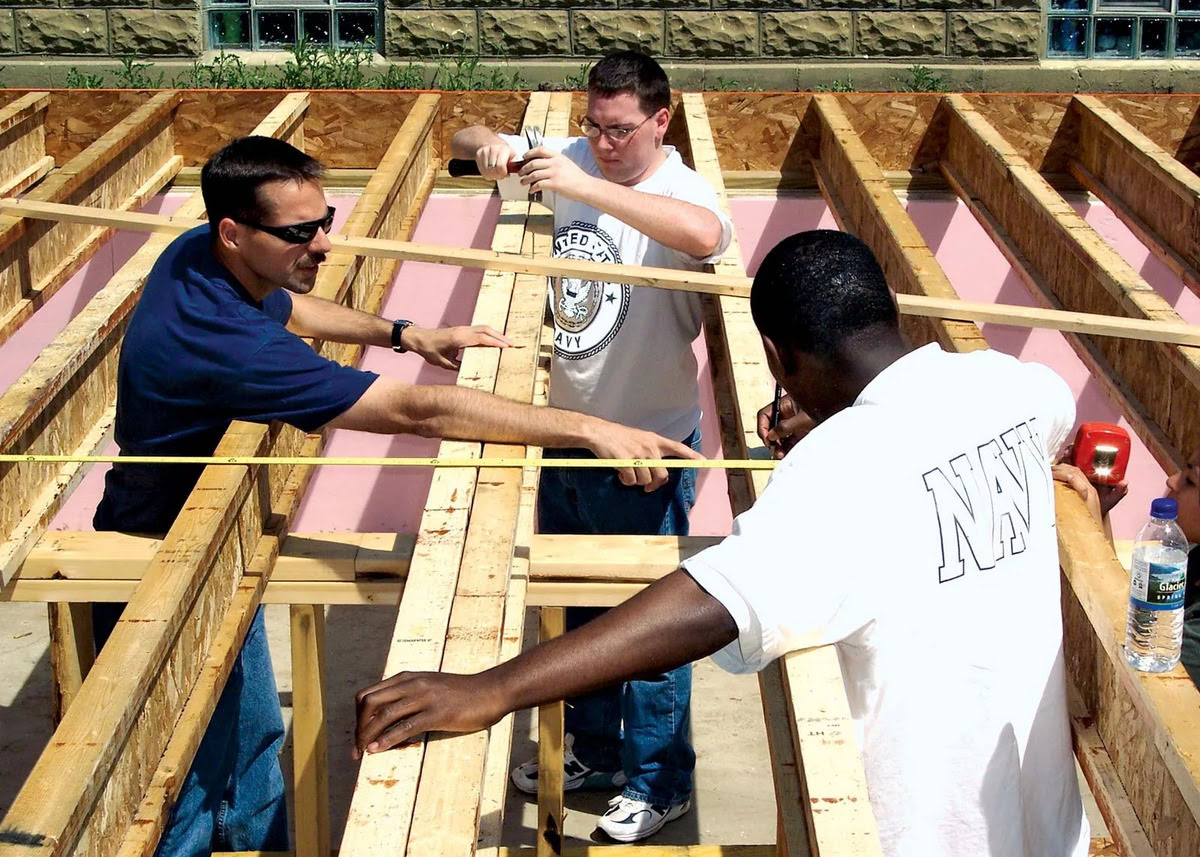
Building & Construction
What Is A Joist In Construction
Modified: December 7, 2023
Learn about joists in building construction and how they play a crucial role in supporting floors and roofs. Understand the importance of these structural elements in ensuring the stability and durability of a building.
(Many of the links in this article redirect to a specific reviewed product. Your purchase of these products through affiliate links helps to generate commission for Storables.com, at no extra cost. Learn more)
Introduction
Welcome to the world of construction! If you’re new to the industry or have recently embarked on a building project, you may have come across the term “joist.” But what exactly is a joist and what role does it play in construction? In this article, we will explore the definition, purpose, types, materials, installation process, and maintenance of joists.
Joists are a fundamental component in the construction of buildings, providing support and stability to the structure. They are horizontal or sloping beams that span an open space, such as between walls or beams, to support the weight of the floors, ceilings, or roofs above. Simply put, joists act as load-bearing members that transfer the weight of the structure to the foundation or load-bearing walls.
These structural elements are essential in preventing sagging, deflection, or collapse of the floors and ceilings, ensuring the integrity and safety of the building. Proper design and installation of joists are critical to ensure the stability and structural efficiency of the entire building.
There are various types of joists used in construction, each serving a specific purpose. From traditional timber joists to modern engineered joists, the choice depends on factors such as building design, load requirements, and budget constraints. Furthermore, the type of material used for joists can vary, including wood, steel, or engineered products like laminated veneer lumber (LVL) or steel joists.
In this article, we will delve into the different types of joists, discuss the materials commonly used, explore the factors to consider in joist design, highlight the installation process, offer tips for maintenance and repair, and provide insights on key considerations for joist replacement.
Whether you’re a construction professional or a homeowner seeking information on building construction, understanding joists and their importance is crucial. So, let’s dive deeper into the world of joists and discover their role in the stability and functionality of a building.
Key Takeaways:
- Joists are essential for building stability, supporting floors, ceilings, and roofs. Proper design, material selection, and maintenance ensure structural integrity and safety.
- When considering joist replacement, consult professionals to assess damage, choose suitable materials, and ensure proper installation. Careful planning and expertise are crucial for successful replacement.
Read more: What Are Joists In Construction
Definition of a Joist
A joist is a horizontal or sloping structural member that spans an open space, providing support for floors, ceilings, or roofs in a building. It is typically made of wood, steel, or engineered materials and is an integral part of the overall structural framework.
Joists are primarily designed to bear the weight of the load above and transfer it to the load-bearing walls or foundation of the structure. They serve as a critical component in distributing the load evenly to ensure the stability, strength, and integrity of the building.
These horizontal members are installed parallel to each other, creating a grid-like pattern across the span of the structure. The spacing between the joists varies depending on factors such as the type of construction, building codes, and the load requirements of the specific area.
Joists play a crucial role in preventing sagging or deflection of the floors and ceilings. They help to evenly distribute the weight and stress generated by the occupants, furniture, equipment, and other elements within the building. By providing support and rigidity, joists ensure that the floors, ceilings, and roofs maintain their structural integrity without compromising safety.
The design and size of joists depend on various factors such as the span of the open space, load requirements, building codes, and the materials used. Engineers and architects carefully calculate the dimensions of the joists, considering factors like the live load (people, furniture, etc.), dead load (weight of the structure itself), and any anticipated dynamic loads.
It’s important to note that joists are different from beams, which are typically larger and provide vertical support to the structure. While beams transfer the loads from above to the foundation or load-bearing walls, joists work in conjunction with beams to provide support and proper load distribution across the structure.
Overall, joists are an essential element in building construction, ensuring the stability and functionality of the floors, ceilings, and roofs. Their design, materials, and installation need to be carefully considered to ensure the structural efficiency and safety of the building.
Purpose of Joists in Construction
Joists serve a crucial purpose in construction, providing structural support, stability, and load-bearing capabilities to buildings. They play a vital role in ensuring the integrity and safety of the floors, ceilings, and roofs. Let’s take a closer look at the key purposes of joists in construction:
- Distributing Weight: One of the primary purposes of joists is to distribute the weight of the structure and its occupants evenly. By spanning the open spaces between walls or beams, joists transfer the load to the load-bearing walls or foundation. This prevents excessive stress on any single point and helps to avoid deflection, sagging, or collapse of the floors and ceilings.
- Supporting the Structure: Joists provide structural support to the floors, ceilings, and roofs by preventing them from bending or sagging. They help to maintain the flatness and horizontal alignment of these surfaces, ensuring a level and stable foundation for the occupants of the building.
- Maximizing Space: Joists allow for the creation of open spaces within a building by eliminating the need for additional support columns or walls. This enhances the flexibility and functionality of the interior design, allowing for larger, open-concept living or office spaces.
- Transferring Loads: Joists work in conjunction with other structural elements, such as beams, to transfer loads from the floors, ceilings, or roofs to the load-bearing components of the building, such as walls or columns. This ensures that the weight is properly distributed and supported throughout the structure.
- Sound Insulation: In addition to their load-bearing capabilities, joists also play a role in sound insulation within buildings. By creating a separation between floors, they help reduce the transmission of noise from one level to another, enhancing privacy and comfort for occupants.
- Fire Resistance: Depending on the materials used, joists can offer fire resistance to a certain degree. Fire-rated joists, such as those made of steel or treated wood, can help slow down the spread of fire within a building, providing occupants with valuable time to evacuate and reducing the risk of total structural collapse.
Overall, the purpose of joists in construction is to provide stability, support, and load distribution within a building. By properly designing and installing joists, builders can ensure the safety and longevity of the structure while maximizing usable space and enhancing the comfort of occupants.
Types of Joists
Joists come in various types, each designed to meet specific construction requirements and accommodate different structural needs. From traditional timber joists to modern engineered joists, understanding the different types can help you make informed decisions during the planning and construction phases. Here are some common types of joists:
- Timber Joists: Timber joists, also known as traditional or conventional joists, are made from solid timber beams. They have been used for centuries and are still a popular choice due to their strength, availability, and cost-effectiveness. Timber joists can be easily cut and modified on-site to fit specific dimensions and offer good insulation properties.
- I-Joists: Also known as I-beams or engineered joists, I-joists are a relatively newer construction innovation. They are composed of laminated veneer lumber (LVL) or oriented strand board (OSB) webs with a top and bottom flange. I-joists offer exceptional strength-to-weight ratio, allowing for longer spans without the need for additional support. They are known for their dimensional stability, resistance to warping and shrinking, and ease of installation.
- Laminated Joists: Laminated joists consist of multiple layers of timber boards bonded together with adhesives. This construction technique provides enhanced strength and stability. Laminated joists are commonly used for longer spans, offering increased load-carrying capacity and reduced deflection. They can be custom-made to accommodate specific design requirements and are often used in commercial and industrial construction.
- Steel Joists: Steel joists, also known as open web steel joists (OWSJ), are composed of steel members formed into a truss-like structure. They offer excellent strength, durability, and fire resistance. Steel joists are commonly used in commercial and industrial buildings where large spans and heavy loads are required. They are lightweight, allowing for easier handling and installation, and offer flexibility in design due to their modular nature.
- Composite Joists: Composite joists combine different materials to take advantage of their individual strengths. For example, a composite joist may consist of a steel flange and a concrete or timber core. These joists offer the benefits of both materials, such as the rigidity and fire resistance of steel combined with the acoustic and thermal properties of concrete or timber.
- Solid Joists: Solid joists, as the name suggests, are made from solid pieces of wood or engineered materials. They are typically used in smaller residential or light commercial construction projects where shorter spans and lower loads are anticipated. Solid joists are cost-effective and easy to install.
It’s important to consult with a structural engineer or architect to determine the most suitable type of joist for your specific project. Factors such as the span of the open space, load requirements, building codes, and budget considerations will influence the choice of joist type. By selecting the appropriate joist, you can ensure the structural integrity, safety, and efficiency of your building.
Common Materials Used for Joists
Joists can be made from various materials, each offering different characteristics and benefits. The choice of material for joists often depends on factors such as load requirements, building codes, cost, and sustainability. Here are some common materials used for joists:
- Wood: Wood is a traditional and widely used material for joists. Common types of wood used include softwood species such as pine, spruce, or fir. Wood joists have the advantage of being readily available, cost-effective, and easy to work with on-site. They offer good insulation properties and can be cut and shaped to fit specific dimensions. However, wood may be susceptible to rot, decay, and insect damage, requiring regular maintenance and treatment to prolong its lifespan.
- Engineered Wood Products: Engineered wood products, such as laminated veneer lumber (LVL), glued laminated timber (glulam), or parallel strand lumber (PSL), are becoming increasingly popular for joist construction. These products are made by bonding together layers or strands of wood with adhesives to create a strong and stable material. Engineered wood products offer enhanced strength, dimensional stability, and resistance to warping or shrinking. They are often used in longer spans or areas with higher load requirements.
- Steel: Steel joists are commonly used in commercial and industrial construction. Steel offers excellent strength, durability, and fire resistance. Steel joists can be manufactured in various shapes and sizes, allowing for optimal load-carrying capacity and spanning capabilities. They can be customized to meet the specific design requirements of a project. Steel joists are lightweight, making them easier to handle and install. However, steel can be more expensive than wood and may require additional fireproofing measures.
- Concrete: Concrete is a versatile material used in construction, including for joists in certain applications. Concrete joists, also known as post-tensioned concrete beams, are often used in multi-story buildings or structures requiring high load-bearing capabilities. Concrete joists offer excellent fire resistance, durability, and long-term stability. They can be precast or cast-in-place on-site, depending on the project requirements. Concrete joists require skilled labor and special equipment for installation.
- Composite Materials: Composite materials, such as fiber-reinforced polymers (FRP) or composite steel and concrete, offer the benefits of both materials. These joists combine the strength and durability of steel or concrete with the lightness and versatility of other materials. Composite materials can provide excellent load-carrying capabilities while reducing overall weight and improving resistance to environmental factors such as corrosion or moisture.
When selecting the material for joists, it’s essential to consider factors such as structural requirements, building codes, budget constraints, and the specific needs of the project. Consulting with a structural engineer or architect can help determine which material is best suited for your construction project, ensuring the integrity, stability, and longevity of the building.
When installing joists in construction, make sure to follow the building codes and manufacturer’s guidelines to ensure proper spacing and support for the structure above.
Factors to Consider in Joist Design
Designing joists for a construction project requires careful consideration of several factors to ensure the structural integrity, safety, and functionality of the building. These factors influence the size, spacing, and material selection for joists. Here are some key factors to consider in joist design:
- Load Requirements: Determining the anticipated load on the joists is crucial. This includes considering the live load (people, furniture, equipment) and the dead load (weight of the structure itself). The design must account for the maximum load the joists will need to support, ensuring they have adequate strength and structural capacity.
- Span Length: The span length is the distance between the supports that the joists will span. Longer spans may require larger or stronger joists to accommodate the increased load and prevent excessive deflection or sagging. The type of material and its load-bearing capabilities should be taken into account when determining the suitable span length.
- Building Codes: Adhering to local building codes and regulations is essential in joist design. Building codes provide guidelines for minimum requirements in terms of load capacities, fire resistance, and safety standards. It is crucial to consult the relevant building authorities and ensure compliance with the applicable codes to meet legal and safety standards.
- Material Selection: The selection of the joist material depends on various factors such as structural requirements, cost, availability, and sustainability. Different materials have different load-bearing capacities, fire resistance properties, and maintenance needs. Evaluating the pros and cons of each material can help choose the most appropriate one for the construction project.
- Spacing: The spacing between the joists is another important consideration. It depends on factors such as the size and load capacity of the joists, the type of flooring or decking material being used, and the anticipated load requirements. Proper spacing ensures even distribution of the load and reduces the risk of sagging or structural failure. It is crucial to follow building codes and manufacturer guidelines for appropriate spacing.
- Environmental Factors: Environmental factors, such as moisture, humidity, and temperature fluctuations, can impact the performance and longevity of joists. Certain materials may be more susceptible to decay, insect damage, or corrosion in specific environments. Assessing the site conditions and considering appropriate treatments or protective measures can help mitigate these effects.
- Compatibility with Other Structural Elements: Joist design should take into account the compatibility and interaction with other structural elements such as beams, columns, or load-bearing walls. Proper connections and continuity between these elements are vital to achieve a cohesive and structurally sound building framework.
Designing joists requires expertise and knowledge of engineering principles. It is recommended to engage a structural engineer or architect who can assess the specific project requirements, perform load calculations, and create a comprehensive joist design that meets safety standards and ensures the longevity of the building.
Installation Process of Joists
The installation process of joists is a critical step in the construction of a building. Proper installation ensures the structural integrity and functionality of the floors, ceilings, and roofs. Here is a general overview of the installation process for joists:
- Preparation: Before installation, the construction site needs to be prepared. This involves clearing the area of any debris or obstructions and ensuring a level and stable foundation for the joists. The layout and spacing of the joists should be marked on the supporting walls or beams based on the design specifications.
- Positioning: The first step in installing joists is positioning them on the supporting walls or beams. The end of each joist should be placed directly on the wall or beam and secured in place temporarily. Care should be taken to ensure that the joists are aligned correctly and level across their length.
- Securing: Once the joists are positioned, they need to be securely fastened to the supporting walls or beams. This typically involves using joist hangers, brackets, or metal connectors to create a strong and stable connection. Proper attachment of the joists to the supports helps to distribute the load evenly and prevents any movement or shifting over time.
- Spacing: After securing the first joist, the remaining joists are installed parallel to each other, spaced evenly according to the design specifications. Spacing can vary depending on factors such as the span length, the type of flooring material, and load requirements. It is essential to follow building codes and guidelines provided by the manufacturer for the appropriate spacing between the joists.
- Leveling and Alignment: Throughout the installation process, it is crucial to ensure that the joists are level and aligned properly. This involves using a level to check the horizontal orientation of the joists and adjusting as necessary. Proper leveling and alignment help to ensure the structural stability and prevent uneven floors or ceilings.
- Bracing: Temporary bracing may be necessary during the installation process to provide additional support and prevent any movement or collapse of the joists. This may involve installing diagonal braces or supports between the joists and the supporting walls or beams. The bracing should be removed once the construction progresses and the permanent load-bearing elements are in place.
- Additional Considerations: Depending on the specific project requirements, additional steps may be necessary during the installation of joists. This could include integrating insulation, soundproofing materials, or fire-rated treatments into the joist system. Consultation with a structural engineer or architect is essential to ensure compliance with building codes and industry standards.
It’s important to note that the installation process of joists requires knowledge of construction techniques and adherence to safety measures. It is recommended to engage professional contractors or skilled carpenters experienced in joist installation to ensure the proper execution of the process.
Maintenance and Repair of Joists
Proper maintenance and timely repairs are crucial for ensuring the longevity and structural integrity of joists in a building. Regular inspections and maintenance can help identify any issues early on and prevent further damage. Here are some important considerations for the maintenance and repair of joists:
- Regular Inspections: Regular inspections of the joists are essential to detect any signs of damage or deterioration. Inspect for signs of sagging, cracks, rot, insect infestation, or water damage. Look for any indications of excessive deflection or unevenness in the floors or ceilings. Inspections should be carried out annually or as recommended by a structural engineer or building professional.
- Addressing Water Damage: Moisture is one of the biggest enemies of joists. Any signs of water damage, such as leaks or moisture intrusion, should be addressed immediately. Identify the source of the water and fix it to prevent further damage. Damaged or rotted joists should be replaced promptly to maintain the structural stability of the building.
- Treating Wood Joists: If the joists are made of wood, they should be treated with appropriate wood preservatives to protect against rot, decay, and insect infestation. Regularly inspect the treated wood for any signs of degradation, and apply additional treatments as needed. Follow the manufacturer’s recommendations and consult with a professional if unsure about the appropriate treatment methods.
- Supporting Load Redistribution: Over time, the load distribution on the joists may change due to remodeling, additions, or changes in the usage of the building. If significant alterations are made, it’s important to consult with a structural engineer to assess whether any adjustments or additional support may be required for the joists.
- Proper Ventilation: Adequate ventilation in the subfloor or crawl space is important to prevent moisture buildup and potential damage to the joists. Ensure there is proper airflow and ventilation to help reduce the risk of condensation, rot, or fungal growth. Clear any debris or obstructions that may hinder proper ventilation.
- Professional Repairs: If damage or structural issues are identified during inspections, it is advisable to consult with a professional contractor, carpenter, or structural engineer for the necessary repairs. They can assess the extent of the damage and provide appropriate solutions, which may include reinforcement, sistering, or replacement of the damaged joists.
- Maintaining Records: Keeping a record of maintenance and repair activities for the joists is important for future reference and documentation. This includes dates of inspections, repairs or treatments carried out, and any professional consultations. These records can provide valuable information for future maintenance, renovations, or property assessments.
Remember, timely maintenance and prompt repairs are essential to ensure the structural integrity and safety of the building. Regular inspections and proper care of joists can help prevent costly repairs, ensure a safe living or working environment, and extend the lifespan of the building.
Key Considerations for Joist Replacement
At some point, joists may require replacement due to damage, deterioration, or changes in building needs. Joist replacement is a critical process that requires careful consideration to ensure structural integrity and safety. Here are some key considerations to keep in mind when undertaking joist replacement:
- Evaluation by Professionals: Before considering joist replacement, it’s important to consult with a structural engineer or building professional. They can assess the severity of the damage, evaluate the condition of the joists, and determine if replacement is necessary. Their expertise will help ensure that the proper steps are taken and appropriate materials are selected.
- Identifying Causes of Damage: Identifying the underlying causes of damage or deterioration is crucial. Whether it’s due to water infiltration, insect infestation, structural overload, or other factors, addressing the root cause is essential to prevent similar issues from arising in the future. Correcting the source of the problem is crucial before replacing the joists to avoid repeating the same issues.
- Choosing the Right Replacement Material: The choice of replacement material will depend on various factors such as load requirements, building codes, and budget considerations. Consider whether the original material is still suitable or if an alternative, such as engineered wood products or steel, would be more appropriate. Consulting with a professional can help determine the best material for the specific project.
- Ensuring Structural Compatibility: When replacing joists, it is important to ensure that the new joists are structurally compatible with the existing components of the building. This includes considerations such as size, spacing, and load-bearing capabilities. The new joists should align with the existing structural elements to maintain overall stability and functionality.
- Proper Installation and Connections: The replacement joists need to be installed correctly with proper connections to the supporting walls or beams. Securely fastening the new joists and ensuring a strong connection is vital to maintain structural integrity. Following manufacturer guidelines and relevant building codes is essential when installing replacement joists.
- Minimizing Disruption: Joist replacement can be a disruptive process, especially in occupied buildings. Considerations should be made to minimize disruption to occupants or ongoing activities. This may include scheduling the replacement work during off-peak hours, establishing safety measures, and clearly communicating the project timeline and potential impacts to those involved.
- Obtaining Necessary Permits: Depending on local regulations and the scope of the replacement project, obtaining the necessary permits may be required. It’s important to check with the local building department and ensure compliance with permit requirements and any additional inspections that may be necessary during or after the replacement process.
- Professional Expertise: Joist replacement can be a complex task, requiring expertise in structural engineering and construction. It is advisable to engage professional contractors or experienced carpenters with a proven track record in joist replacement to ensure proper execution and adherence to safety standards.
Joist replacement is a significant undertaking that should be approached with careful planning and the guidance of professionals. By considering these key factors and seeking expert advice, you can ensure a successful joist replacement process that maintains the structural integrity and safety of the building.
Read more: What Is A Floor Joist
Conclusion
Joists are an integral part of building construction, providing essential support, stability, and load-bearing capabilities. Understanding the definition, purpose, types, materials, installation process, maintenance, and repair of joists is crucial for architects, contractors, and homeowners alike. By considering the key factors involved in joist design, installation, maintenance, and replacement, one can ensure the structural integrity and longevity of a building.
Joists come in various types, including traditional timber joists, engineered joists, steel joists, and composite joists. The choice of material for joists, such as wood, engineered wood products, steel, or concrete, depends on factors like load requirements, availability, cost, and desired characteristics. Proper design and installation of joists, while adhering to local building codes, ensure even weight distribution and prevent sagging, deflection, or collapse of floors and ceilings.
Maintenance and regular inspections are essential to identify and address any issues with joists early on. Treating wood joists, addressing water damage, ensuring proper ventilation, and supporting load redistribution are important steps in maintaining the structural integrity of the joists. Timely repairs, carried out by professionals, help prevent further damage and maintain the safety and functionality of the building.
When contemplating joist replacement, enlisting the expertise of a structural engineer or building professional is crucial. They can assess the condition of the joists, identify the cause of damage, and guide the selection of appropriate materials and installation techniques. Careful planning, consideration of structural compatibility, and adherence to proper installation practices are key to successful joist replacement.
In conclusion, joists are vital components in construction, providing support and stability to buildings. Understanding their role, the different types, materials, and the importance of proper installation, maintenance, and potential replacement is essential for maintaining safe and structurally sound buildings. By incorporating these considerations, one can ensure the longevity and integrity of the joists, contributing to the overall quality and performance of the constructed environment.
Frequently Asked Questions about What Is A Joist In Construction
Was this page helpful?
At Storables.com, we guarantee accurate and reliable information. Our content, validated by Expert Board Contributors, is crafted following stringent Editorial Policies. We're committed to providing you with well-researched, expert-backed insights for all your informational needs.
0 thoughts on “What Is A Joist In Construction”