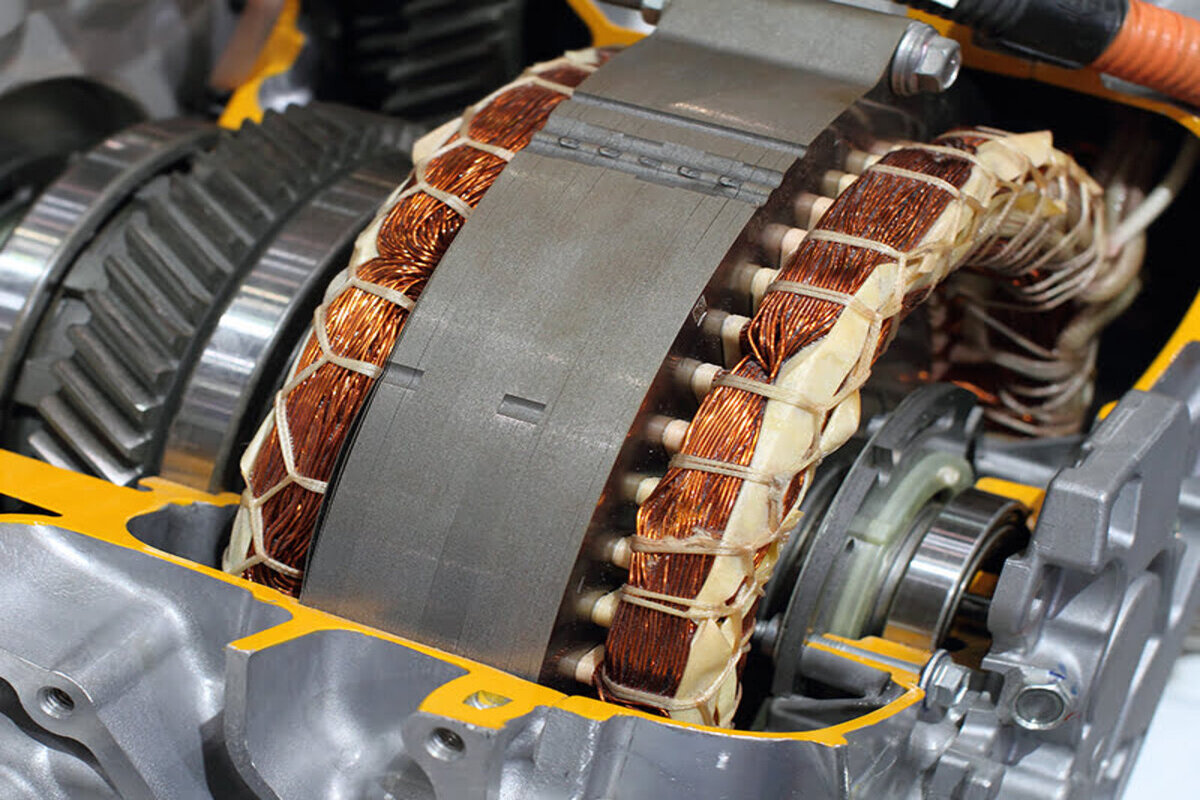
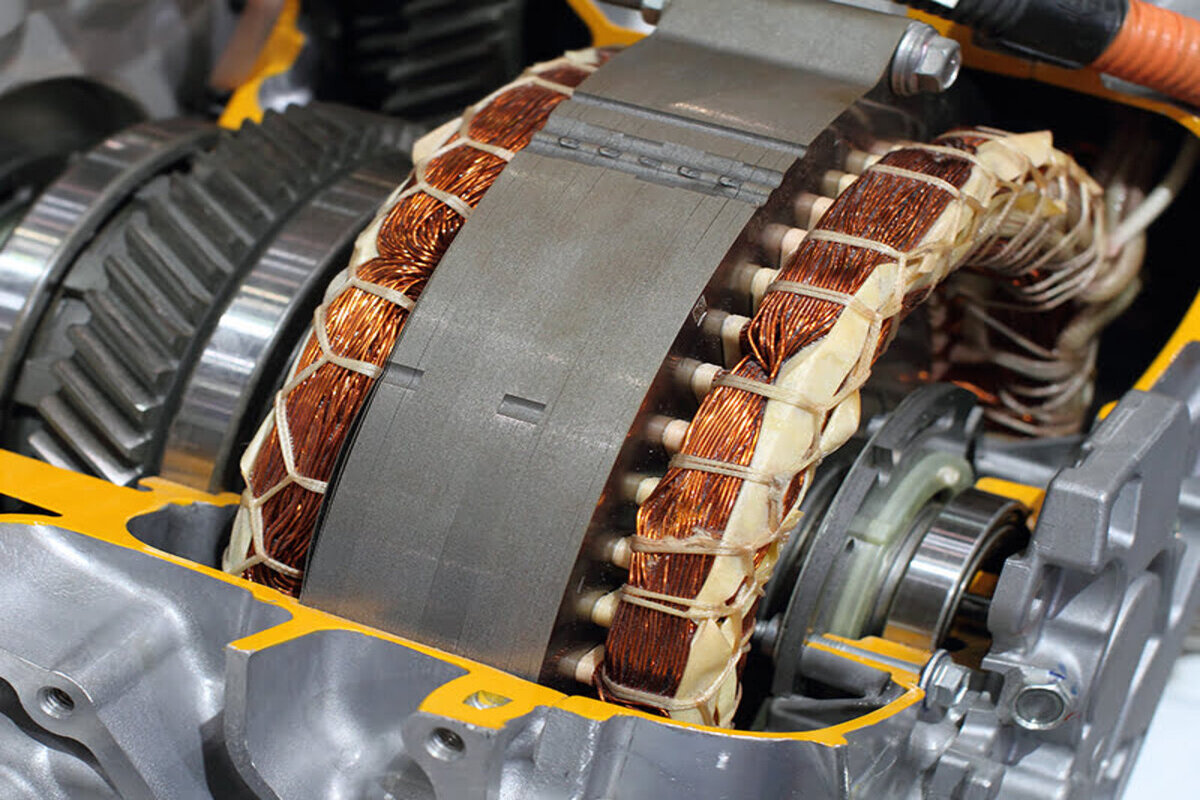
Articles
How To Test A Electric Motor
Modified: January 5, 2024
Looking for articles on how to test an electric motor? Gain valuable insights and expert tips for troubleshooting and testing electric motors in this comprehensive guide.
(Many of the links in this article redirect to a specific reviewed product. Your purchase of these products through affiliate links helps to generate commission for Storables.com, at no extra cost. Learn more)
Introduction
Electric motors are crucial components in a wide range of devices and machinery, from household appliances to industrial equipment. As with any mechanical device, these motors can experience issues and malfunction over time. To determine whether a motor is functioning properly or if it requires repair or replacement, it is important to perform regular testing.
This article will guide you through the process of testing an electric motor, helping you identify potential problems and find solutions to keep it running smoothly. By following these steps, you can save time and money by avoiding unnecessary repairs and extend the lifespan of your motor.
Key Takeaways:
- Regular testing and maintenance of electric motors can prevent costly repairs and extend their lifespan. By following the outlined steps, you can diagnose issues early and keep your motors running efficiently.
- Prioritizing safety and seeking professional assistance when uncertain is crucial when testing electric motors. Incorporating these procedures into your maintenance routine can prevent unexpected breakdowns and ensure optimal motor performance.
Read more: How To Test A Small Electric Motor
Step 1: Visual Inspection
The first step in testing an electric motor is to perform a visual inspection. This allows you to identify any obvious issues that may contribute to the motor’s malfunction.
Begin by inspecting the motor’s exterior for any signs of damage, such as cracks, dents, or loose connections. Ensure that all bolts and screws are tightened properly and that there are no loose or exposed wires. Check for any excessive dirt or debris that may be obstructing the motor’s cooling vents.
Next, examine the motor’s bearings. Look for any signs of wear or damage, such as excessive noise, vibration, or leakage of lubricant. If you notice any of these issues, it may indicate that the bearings need to be replaced.
Additionally, inspect the motor’s power cables and terminals. Make sure they are securely connected and free from corrosion. Any loose or corroded connections can lead to poor performance or even electrical hazards.
If you observe any of these issues during the visual inspection, it is recommended to address them before proceeding with further testing. Sometimes, a simple fix or maintenance procedure can resolve the problem without the need for extensive repairs.
Remember, safety should always be a priority when working with electric motors. Ensure that the motor is unplugged or disconnected from its power source before conducting any visual inspections or tests. If necessary, seek assistance from a qualified professional to handle any complex issues.
Step 2: Check the Power Supply
After performing a visual inspection, the next step in testing an electric motor is to check the power supply. An inadequate or unstable power supply can cause motor issues or prevent the motor from functioning altogether.
Start by verifying that the power source is delivering the correct voltage and frequency as specified by the motor’s manufacturer. Use a voltmeter or multimeter to measure the voltage, ensuring that it matches the motor’s rated voltage. Similarly, check the frequency of the power supply to ensure it meets the motor’s requirements.
If the voltage or frequency is outside the acceptable range, it can lead to motor inefficiency, overheating, or even permanent damage. In such cases, consult an electrician or contact your local power utility to troubleshoot and rectify the power supply issues.
Furthermore, check if the power supply is stable and free from fluctuations. Voltage spikes or surges can harm the motor’s electronic components and contribute to premature failure. Consider installing surge protectors or voltage stabilizers to safeguard the motor against such irregularities.
It is also essential to examine the motor’s power cords and plugs. Look for any signs of damage, frayed wires, or loose connections. Ensure that the power cords are rated appropriately for the motor’s power requirements and that the plugs fit securely into the power outlet.
Once you have ensured a stable and appropriate power supply, you can move on to further testing to diagnose any potential issues with the motor itself.
Remember, always take necessary safety precautions while working with electricity. Avoid contact with live wires, and if uncertain, seek assistance from a qualified electrician.
Step 3: Measure the Motor’s Resistance
Measuring the resistance of an electric motor is an important step in testing its overall health and functionality. Resistance testing can help identify open or short circuits, faulty windings, or other electrical issues in the motor.
To measure the motor’s resistance, you will need a digital multimeter. Set the multimeter to the resistance or ohms function and ensure that it is properly calibrated.
Start by disconnecting the motor from its power source and any external circuits. Ensure that the motor is completely isolated and not connected to any other electrical components or devices.
Next, locate the motor’s terminal connections. These are typically labeled as “A,” “B,” and “C” for three-phase motors or “T1” and “T2” for single-phase motors. Use the multimeter’s probes to measure the resistance between each terminal combination.
For a three-phase motor, measure the resistance between terminals A and B, B and C, and C and A. The resistance values should be relatively equal within a small tolerance range. If there is a significant deviation in resistance values, it may indicate a problem with one or more windings.
For a single-phase motor, measure the resistance between terminals T1 and T2. Again, the resistance should be within an acceptable range, typically specified by the motor’s manufacturer.
If the measured resistance is too high or infinite (open circuit), it may indicate a broken winding or a damaged connection. On the other hand, a very low resistance (short circuit) suggests a wiring issue or a fault in the motor’s insulation.
Keep in mind that resistance measurements can vary depending on the motor’s design and specifications. Consult the motor’s documentation or contact the manufacturer for specific resistance values or acceptable tolerance ranges.
By measuring the motor’s resistance, you can gain valuable insights into the integrity of its electrical components and diagnose potential faults or issues. However, if you are unsure about reading the resistance values or interpreting the results, it’s recommended to consult a qualified electrician or technician for further guidance.
Step 4: Test for Continuity
Continuity testing is another crucial step in testing an electric motor. It helps identify any breaks or interruptions in the motor’s circuits or connections. By checking for continuity, you can ensure that the electrical current can flow freely throughout the motor’s various components.
To perform a continuity test, you will again need a digital multimeter set to the continuity or “beep” mode. This mode emits a sound when a circuit is closed and there is a continuous path for the electrical current.
Start by disconnecting the motor from the power source and any external devices. Ensure that the motor is isolated and not connected to any other electrical components.
Using the multimeter’s probes, touch one probe to a motor terminal and the other probe to another terminal. If you hear a beep or see a continuity symbol on the multimeter’s display, it indicates that there is a complete path for the electrical current between the terminals.
Repeat this process for all possible terminal combinations in the motor. Check the continuity between terminals A and B, B and C, and C and A for a three-phase motor. For a single-phase motor, test the continuity between terminals T1 and T2.
If the multimeter does not emit a sound or indicates an open circuit (no continuity), it suggests a break or interruption in the motor’s circuits. This could be due to a faulty connection, a broken wire, or a damaged component.
In some cases, continuity issues can be resolved by inspecting and securing loose connections or repairing damaged wires. However, if the problem persists, it may require a closer examination or professional assistance to diagnose and rectify the underlying cause.
Continuity testing is a valuable tool to identify electrical continuity issues in an electric motor. By ensuring that the circuits are properly connected and free from breaks, you can mitigate the risk of poor performance, overheating, or other motor malfunctions.
Always exercise caution and observe necessary safety measures when performing continuity tests or any electrical work. If you are unsure about the readings or need further assistance, consult an electrician or a qualified technician.
Step 5: Check the Motor’s Voltage Supply
Checking the voltage supply to an electric motor is essential in ensuring it receives the correct amount of power to operate efficiently. Insufficient or excessive voltage can lead to motor performance problems or premature failure. Therefore, it is crucial to verify the motor’s voltage supply to diagnose potential issues.
Begin by measuring the voltage at the motor terminals using a digital multimeter. Set the multimeter to the voltage measurement mode and ensure it is properly calibrated.
Start by disconnecting the motor from the power source and any external circuits. Make sure the motor is isolated and not connected to any other electrical components.
Using the multimeter’s probes, touch one probe to the motor’s live (hot) terminal and the other probe to the neutral terminal. This will allow you to measure the voltage supply to the motor.
Read the multimeter’s display to determine the voltage. It should match the motor’s rated voltage specified by the manufacturer. If the voltage is too low or too high, it can affect the motor’s performance and cause issues.
If the voltage is significantly lower than the motor’s rated voltage, it may indicate a problem with the power supply or a faulty wiring connection. Consider checking the electrical panel, circuit breakers, and any external transformers to ensure they are providing the correct voltage.
On the other hand, if the voltage is higher than the motor’s rated voltage, it can lead to overheating, increased wear and tear, and potential damage to the motor’s components. In such cases, consult an electrician to investigate and correct the high voltage issue.
It is crucial to maintain a stable and consistent voltage supply to the motor for optimal performance. Fluctuating or unstable voltages can result in motor inefficiency, increased energy consumption, and potential damage to the motor’s internal components.
By regularly checking the motor’s voltage supply, you can identify any electrical issues and ensure that the motor is receiving the correct amount of power to operate efficiently.
Remember to exercise caution and observe safety protocols while working with electrical equipment. If you are uncertain about the readings or need professional assistance, consult an electrician or a qualified technician.
When testing an electric motor, always check for any signs of damage or wear on the motor casing, wiring, and connections. Use a multimeter to test for continuity and insulation resistance to ensure the motor is functioning properly.
Step 6: Inspect Motor Capacitors
Motor capacitors play a crucial role in the operation of many electric motors. They store electrical energy and help provide the necessary starting torque or improve motor efficiency. Inspecting and testing motor capacitors can help identify any issues that may affect the motor’s performance.
Start by disconnecting the motor from the power source and allow it to discharge any residual energy. Capacitors can store electrical charge even when the motor is not powered, so it’s important to take precautionary measures to avoid any electrical shocks.
Visually inspect the motor capacitors for any signs of bulging, leaking, or damaged casing. A swollen or bulging capacitor usually indicates a failure and needs to be replaced. Similarly, if you notice any leakage or electrolyte residue around the capacitor, it indicates a leak and the capacitor should be replaced immediately.
Next, check the capacitor terminals for any signs of corrosion or loose connections. Ensure that the terminals are clean and securely tightened. Corroded or loose terminals can impact the capacitor’s performance and may require cleaning or replacement.
Once the visual inspection is complete, you can proceed to test the capacitors using a digital capacitance meter. Set the meter to the capacitance measurement mode and connect the meter probes to the capacitor terminals. The meter will display the capacitance value of the capacitor.
The measured capacitance should match the rated capacitance specified by the manufacturer. If the capacitance reading deviates significantly from the rated value, it may indicate a faulty or damaged capacitor. In such cases, it is recommended to replace the capacitor with a new one of the same rating.
Motor capacitors are critical components for the proper operation of electric motors. By inspecting and testing capacitors regularly, you can ensure their functionality and prevent any potential motor performance issues.
If you are uncertain about inspecting or testing capacitors, it is advisable to consult a qualified technician or electrician for assistance. They have the expertise and knowledge to handle capacitors safely and accurately diagnose any issues.
Step 7: Test Motor Windings
The windings are an integral part of an electric motor that converts electrical energy into mechanical energy. Testing the motor windings can help identify any faults or abnormalities that may impede the motor’s performance.
Before proceeding with the winding test, ensure that the motor is disconnected from the power source and any external circuits. Make sure the motor is isolated and not connected to any other electrical components.
There are several methods to test motor windings, but one commonly used technique is the “Ohm’s Law” method. Here’s how you can perform this test:
- Set your digital multimeter to the resistance or ohms mode and ensure that it is properly calibrated.
- Identify the motor’s winding connections. It could be labeled as “U,” “V,” and “W” for three-phase motors or “M,” “S,” and “C” for single-phase motors.
- Measure the resistance between each winding using the multimeter probes. Start by measuring the resistance between U to V, V to W, and W to U for three-phase motors. For single-phase motors, measure the resistance between M and S, M and C, and S and C.
- The resistance readings should be relatively equal within a certain tolerance range. Any significant deviation in resistance values may indicate an issue with the windings.
- A reading that shows infinite resistance (open circuit) suggests a broken or disconnected winding. On the other hand, a reading that shows very low or zero resistance (short circuit) indicates a shorted winding.
It’s important to note that resistance values may vary depending on the motor’s design and specifications. Consult the motor’s documentation or contact the manufacturer for specific resistance values or acceptable tolerance ranges.
Testing the motor windings can help identify faults such as open or short circuits, damaged insulation, or faulty connections. If you encounter any abnormalities during the winding test, it is recommended to consult a qualified electrician or technician for further diagnosis and repair.
Remember to exercise caution and follow safety protocols while working with electric motors and conducting tests. If you are uncertain about the readings or require expert assistance, seek professional help.
Step 8: Evaluate Motor Current
Evaluating the motor current is a crucial step in testing an electric motor as it provides insights into its electrical performance and efficiency. Monitoring the current can help identify any overloading, imbalance, or abnormality in the motor’s operation.
Before proceeding with the current evaluation, ensure that the motor is disconnected from the power source and any external circuits. Make sure the motor is isolated and not connected to any other electrical components.
To measure the motor current, you will need a current clamp meter or a digital multimeter with a current measurement function:
- Set your current clamp meter or multimeter to the appropriate amperage range and ensure that it is properly calibrated.
- Identify the motor’s power cable or lead wires. These are usually labeled as “L1,” “L2,” and “L3” for three-phase motors or “L” and “N” for single-phase motors.
- Wrap the current clamp around one of the motor’s power cables or lead wires. Ensure that the clamp is properly secured and making good contact.
- Energize the motor and observe the current reading on the meter’s display. The measured current should be within the motor’s rated current specified by the manufacturer.
- Repeat this process for each power cable or lead wire to evaluate the current across all phases.
Comparing the measured current values across the different phases of a three-phase motor can help identify any imbalance or deviation. If there is a significant difference in current readings, it may indicate issues such as an unbalanced load, a fault in the motor windings, or a faulty connection.
In addition to evaluating the current magnitude, it’s important to monitor the current over time. Excessive or irregular fluctuations in current can indicate problems with the motor, such as excessive mechanical load, overheating, or issues with the motor’s control circuitry.
If you notice any abnormalities, such as excessively high current or erratic fluctuations, it is recommended to consult a qualified electrician or technician for further investigation and necessary repairs.
Evaluating the motor current provides valuable information about the motor’s electrical performance and can help detect any potential problems. By addressing these issues promptly, you can prevent further damage and ensure the motor’s optimal operation.
Always prioritize safety while working with electric motors. Use appropriate protective gear and follow all safety guidelines. If you are uncertain about interpreting the current readings or need professional assistance, consult a qualified electrician or technician.
Read more: How To Test Fan Motor
Step 9: Monitor Motor Temperature
Monitoring the motor’s temperature is a critical step in testing and maintaining an electric motor. Temperature is a key indicator of the motor’s health and can help identify any potential issues or abnormal operating conditions.
Start by allowing the motor to run for some time to reach its normal operating temperature. Then, using a temperature measurement device such as an infrared thermometer or a temperature probe, measure the temperature of various parts of the motor, including the housing and the windings.
Compare the measured temperatures with the motor’s rated temperature limits provided by the manufacturer. If the measured temperature exceeds the specified limits, it may indicate an overheating condition. Overheating can be caused by various factors such as an overloaded motor, inadequate ventilation, or a malfunctioning cooling system.
It is important to note that different parts of the motor may have different temperature limits. The windings, for example, usually have a lower temperature limit compared to the motor housing. Consult the motor’s documentation or contact the manufacturer for specific temperature limits and guidelines.
In addition to monitoring the absolute temperature, it is essential to observe any temperature differentials within the motor. Significant temperature variations between different parts of the motor or uneven distribution of heat could indicate issues such as insulation breakdown, poor cooling, or a faulty component.
Regularly monitoring the motor’s temperature can help identify problems early on, prevent potential damage, and prolong the motor’s lifespan. If you notice any abnormal temperature readings or temperature differentials, it is recommended to consult a qualified technician or electrician for further investigation and necessary repairs.
Remember to prioritize safety while handling electric motors. Always follow proper safety protocols and allow the motor to cool down before touching any parts. If you are uncertain about interpreting the temperature readings or need professional assistance, seek guidance from a qualified electrician or technician.
Step 10: Perform Load Test
Performing a load test is the final step in testing an electric motor. This test helps assess the motor’s performance under operating conditions and determines its ability to handle the designated load or workload.
Before conducting a load test, ensure that the motor is safely isolated from the power source and any external circuits. Make sure the motor is not connected to any other electrical components.
To perform a load test, follow these steps:
- Select a suitable load for the motor based on its intended application. This could involve connecting the motor to the equipment it is designed to power or using a load bank to simulate the expected workload.
- Energize the motor and gradually increase the load to the desired level. Monitor the motor’s performance, including its speed, current draw, and temperature.
- Observe the motor’s behavior under the load. It should run smoothly, without significant vibrations, excessive noise, or signs of struggling.
- Measure and record important parameters such as the motor’s current consumption, voltage, and rotational speed.
- Compare the measured values with the motor’s rated specifications provided by the manufacturer. Ensure that the motor operates within the specified limits to ensure safety and optimal performance.
A load test helps evaluate the motor’s ability to handle the expected workload and reveals any performance issues or abnormalities. It also aids in determining whether the motor is operating efficiently and within its rated capacity.
During the load test, pay attention to any unusual behavior or deviations from the expected performance. Excessive current draw, overheating, or a significant drop in speed can indicate problems such as mechanical issues, electrical malfunctions, or an overloaded motor.
If you notice any concerning issues during the load test, it is advisable to consult a qualified technician or electrician for further investigation and necessary repairs.
Performing a load test provides valuable insights into the motor’s capabilities and ensures its reliability and efficiency under normal operating conditions. It is an important step in validating the motor’s performance and determining if it meets the specifications and requirements of its intended application.
Always prioritize safety during load testing. Adhere to safety guidelines, use appropriate personal protective equipment, and consult professionals if needed. If you are uncertain about conducting the load test or interpreting the results, seek assistance from a qualified technician or electrician.
Conclusion
Testing an electric motor is a vital process to ensure its proper functioning, identify potential issues, and prevent costly repairs or replacements. By following the steps outlined in this article, you can effectively diagnose and evaluate the health of your electric motor.
Beginning with a visual inspection, you can identify any visible damage or loose connections that may impede the motor’s performance. Checking the power supply helps ensure that the motor is receiving the correct voltage and frequency to operate efficiently.
Measuring the motor’s resistance and testing for continuity allows you to identify any open or short circuits, faulty connections, or damaged windings. Evaluating the motor’s current and monitoring its temperature gives insight into its electrical performance and helps detect overheating or abnormal operating conditions.
Inspecting motor capacitors is crucial as they contribute to the motor’s starting torque and efficiency. Faulty capacitors can impact the motor’s performance and should be replaced if necessary.
Lastly, performing a load test determines the motor’s ability to handle the designated workload. This test helps validate the motor’s performance and ensures it operates within its specified limits.
Throughout the testing process, it is important to prioritize safety and consult professionals if needed. If you are uncertain about any step or require expert assistance, do not hesitate to seek guidance from a qualified electrician or technician.
Regular testing and maintenance of your electric motor can extend its lifespan, improve its efficiency, and prevent unexpected breakdowns. By incorporating these testing procedures into your maintenance routine, you can keep your electric motor running smoothly and avoid costly repairs or replacements.
Remember, each motor is unique, and it is essential to refer to the manufacturer’s guidelines and specifications for specific testing procedures and recommendations.
Frequently Asked Questions about How To Test A Electric Motor
Was this page helpful?
At Storables.com, we guarantee accurate and reliable information. Our content, validated by Expert Board Contributors, is crafted following stringent Editorial Policies. We're committed to providing you with well-researched, expert-backed insights for all your informational needs.
0 thoughts on “How To Test A Electric Motor”