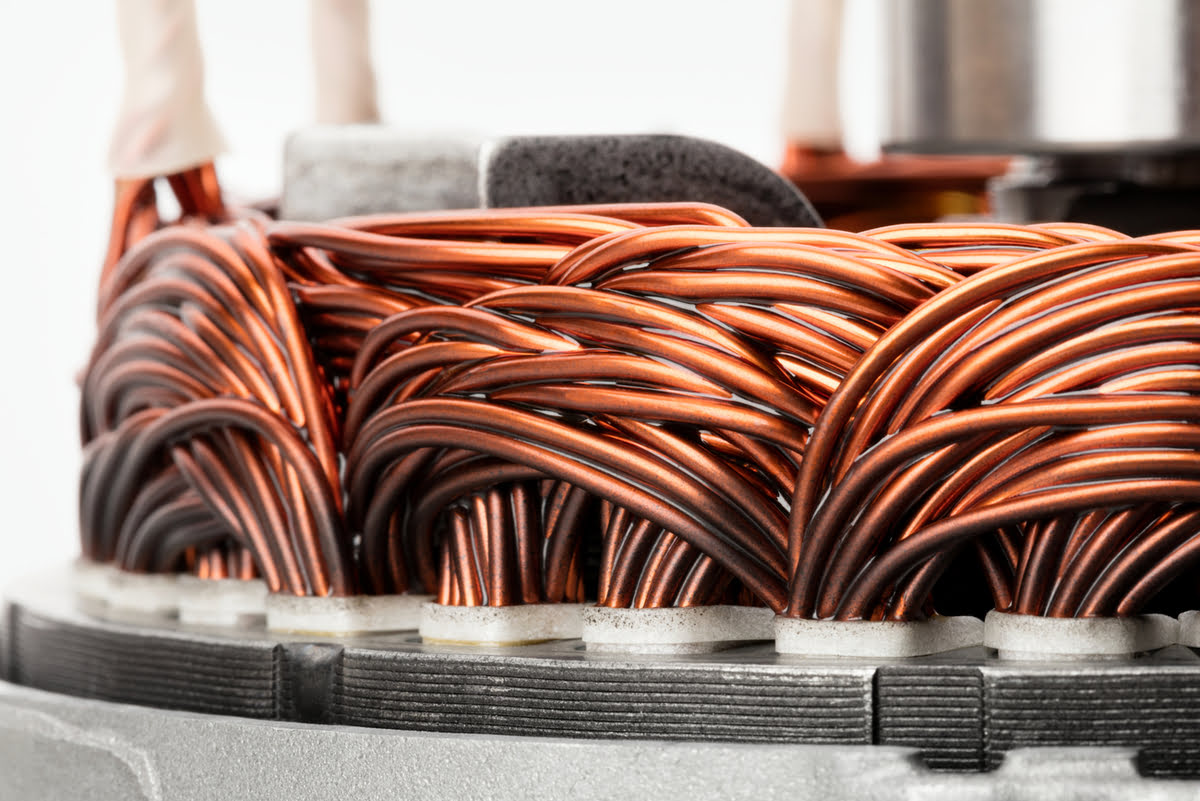
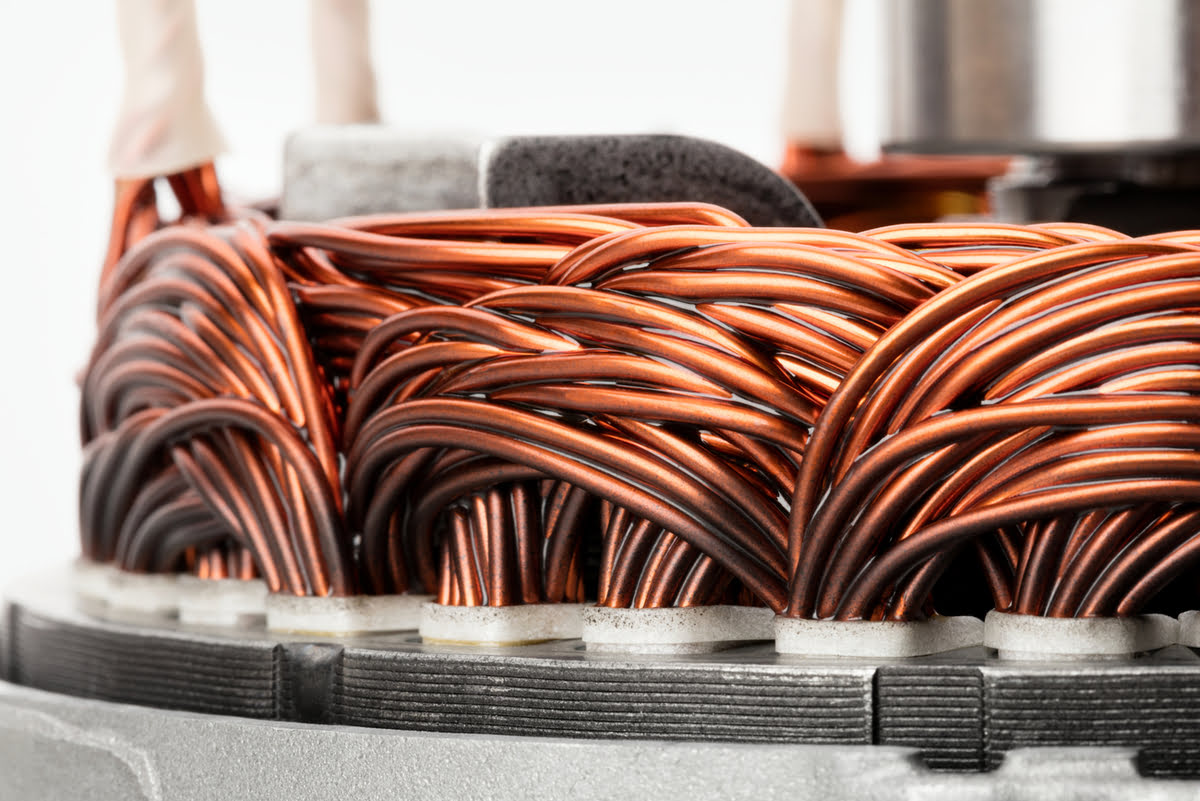
Articles
How Much Copper Is In An Electric Motor
Modified: May 6, 2024
Discover the amount of copper found in an electric motor with informative articles.
(Many of the links in this article redirect to a specific reviewed product. Your purchase of these products through affiliate links helps to generate commission for Storables.com, at no extra cost. Learn more)
Introduction
Welcome to our article on the fascinating world of electric motors and the role that copper plays within them. Electric motors are vital components found in countless devices, from household appliances to industrial machinery. These devices rely on the power generated by electric motors to function efficiently and effectively.
In this article, we will explore the significance of copper in electric motors and delve into the various copper components that are crucial to their operation. Furthermore, we will discuss how the amount of copper in an electric motor is determined and the factors that can affect its content. Finally, we will examine the importance of recycling copper from electric motors to minimize waste and promote sustainability.
So, let’s delve into the world of electric motors and uncover the important role that copper plays within them.
Key Takeaways:
- Copper is a crucial element in electric motors, enhancing their performance and efficiency through its exceptional electrical and thermal conductivity, mechanical properties, and resistance to corrosion. Its role in power transmission and heat dissipation is indispensable.
- Recycling copper from electric motors is essential for conserving resources, reducing waste, and promoting environmental sustainability. By recovering and reusing valuable copper components, we can minimize the need for new copper extraction and contribute to a more circular and efficient use of this valuable material.
Read more: How Much Copper Is In A 50 HP Electric Motor
What is an Electric Motor?
An electric motor is a device that converts electrical energy into mechanical energy. It is comprised of several essential components that work together to create rotational motion. Electric motors are widely used in various applications, including industrial machinery, automobiles, household appliances, and even small electronic devices.
The primary principle behind the functioning of an electric motor is electromagnetic induction. This process involves the interaction of magnetic fields and electrical currents to produce motion. Electric motors consist of a stationary component called the stator and a rotating component known as the rotor.
The stator contains a series of wire coils that are evenly spaced around the motor’s circumference. These wire coils, also known as windings, are often made of copper due to its excellent conductivity properties. When an electric current flows through the stator windings, a magnetic field is generated.
The rotor, on the other hand, consists of a series of permanent magnets or electromagnets. When the stator’s magnetic field interacts with the rotor’s magnetic field, it creates a force that causes the rotor to rotate. This rotational motion is then transmitted to the machinery or device being powered by the motor.
Electric motors come in various sizes and types, depending on the specific application they are designed for. Some common types include AC (alternating current) motors, DC (direct current) motors, synchronous motors, and induction motors. Each type has its own advantages and is suited for specific tasks.
In summary, an electric motor harnesses electrical energy and converts it into mechanical energy through the interaction of magnetic fields and electrical currents. Copper plays a crucial role in the construction of electric motors, specifically in its windings, due to its superior conductivity properties.
The Importance of Copper in Electric Motors
Copper is an essential component in electric motors and plays a vital role in their overall performance and efficiency. Its unique properties make it the preferred choice for the construction of motor windings, which are responsible for generating the magnetic fields necessary for motor operation.
One of the primary reasons copper is used in electric motors is its exceptional electrical conductivity. Copper is one of the best conductors of electricity, allowing for efficient flow of electrical current through the motor windings. This high conductivity minimizes energy losses and maximizes the motor’s power output, resulting in improved performance and reduced energy consumption.
In addition to its conductivity, copper also has excellent thermal conductivity properties. This means that it effectively conducts heat away from the motor windings, preventing overheating and ensuring the motor operates within safe temperature limits. This thermal management capability is critical for maintaining the longevity and reliability of electric motors.
Copper’s mechanical properties also contribute to its importance in electric motors. It is a highly malleable and ductile metal, allowing for easy shaping and forming of the motor windings. This flexibility enables manufacturers to create complex and precise winding configurations, resulting in more efficient electromagnetic interactions and increased motor performance.
Another significant advantage of copper is its resistance to corrosion. The protective oxide layer that forms on the surface of copper helps prevent degradation and ensures the motor’s longevity, even in challenging environments or exposure to moisture.
Furthermore, copper is readily available and relatively cost-effective compared to other conductive metals. Its abundance, combined with its excellent electrical and thermal properties, makes it the preferred choice for electric motor applications in various industries.
In summary, the importance of copper in electric motors cannot be overstated. Its superior electrical and thermal conductivity, along with its mechanical properties and resistance to corrosion, make it the ideal material for motor windings. Copper enables efficient power transmission, effective heat dissipation, and overall enhanced performance and reliability of electric motors.
Copper Components in Electric Motors
Copper is a fundamental component in electric motors, and its presence can be found in various parts of the motor’s construction. Let’s explore some of the key copper components in electric motors:
- Motor Windings: The motor windings, also known as coils or windings, are where copper is predominantly found in electric motors. These windings consist of insulated copper wire that is wound into multiple layers. The copper wire’s high electrical conductivity allows for efficient current flow, generating the necessary magnetic fields for motor operation.
- Rotor Bars: In some types of electric motors, such as induction motors, the rotor consists of copper bars or conductive aluminum alloy bars. These bars, often referred to as rotor windings or rotor conductors, are typically installed in the rotor slots. The electrical current induced in the rotor bars interacts with the stator’s magnetic field, resulting in rotational motion.
- Busbars: Busbars are large, flat strips or bars made of copper or copper alloys. These bars are responsible for distributing electrical current between various motor components, such as the windings, brushes, and other electrical connections. Busbars provide a low-resistance pathway for current flow, minimizing energy losses.
- Brushes and Commutators: In DC motors, copper is present in the brushes and commutators, which enable the flow of electrical current to the rotor. The brushes, typically made of carbon or graphite, apply pressure to the commutator, a segmented copper ring, providing electrical connections to different rotor windings as the rotor rotates.
- Connection Wires: Copper wires are used to connect various motor components, such as the windings, terminals, and brushes. These wires ensure reliable electrical connections and efficient transmission of current throughout the motor system.
The use of copper in these components is crucial to the motor’s functioning, as copper’s excellent electrical conductivity allows for efficient transmission of electrical energy and optimal performance.
In summary, copper plays a significant role in various components of electric motors, including the motor windings, rotor bars, busbars, brushes, commutators, and connection wires. These copper components enable efficient power transmission, effective magnetic field generation, and reliable electrical connections, all contributing to the overall performance and functionality of electric motors.
When determining the amount of copper in an electric motor, consider the size and type of motor. Larger motors typically contain more copper, while smaller motors may have less. Additionally, copper content can vary based on the motor’s design and efficiency.
Determining the Amount of Copper in an Electric Motor
The amount of copper in an electric motor can vary depending on the motor’s size, design, and specific application. Determining the exact amount of copper in a motor is essential for various reasons, such as assessing its value for recycling or analyzing its efficiency and performance. There are several methods used to determine the amount of copper in an electric motor:
- Weighing Method: One of the simplest ways to estimate the copper content in a motor is by weighing it. This method involves weighing the motor before and after removing the non-copper components, such as the iron casing and other non-metal parts. The weight difference provides an approximate estimation of the copper content in the motor.
- Disassembly and Analysis: Another method is to disassemble the motor and visually inspect its components. By separating the motor windings, rotor bars, and other copper parts from the non-copper materials, it becomes possible to measure and weigh the copper parts separately. This method provides a more accurate assessment of the copper content but requires the motor to be taken apart.
- X-ray Fluorescence (XRF) Spectrometry: XRF spectrometry is a non-destructive and precise method for analyzing the elemental composition of materials. This technique involves using X-ray radiation to excite the atoms in the motor, causing them to emit characteristic X-rays. By measuring the emitted X-rays, the amount of copper and other elements in the motor can be accurately determined.
- Chemical Analysis: Chemical analysis methods, such as acid digestion and atomic absorption spectroscopy, can be used to determine the copper content in electric motors. These methods involve dissolving the motor components in a suitable acid solution, followed by analyzing the concentration of the dissolved copper using specialized equipment.
It’s important to note that the level of accuracy and complexity of these methods can vary. Some methods, such as weighing and visual inspection, provide a rough estimation of the copper content, while techniques like XRF spectrometry and chemical analysis offer more precise results.
In summary, determining the amount of copper in an electric motor can be done through various methods, including weighing, disassembly and analysis, X-ray fluorescence spectrometry, and chemical analysis. Selecting the appropriate method depends on the accuracy required and the accessibility to specialized equipment. Accurately assessing the copper content in an electric motor is beneficial for recycling purposes, evaluating efficiency, and analyzing performance.
Read more: How Much Does An Electric Motor Cost
Factors Affecting Copper Content in Electric Motors
The copper content in an electric motor can be influenced by several factors that are dependent on the motor’s design, application, and efficiency requirements. Understanding these factors can provide insights into why copper content may vary among different motors. Here are some key factors that affect copper content in electric motors:
- Motor Size and Power: Larger motors typically require more copper in their windings to handle higher electrical currents and generate the necessary magnetic fields. This is especially true for motors with higher power ratings, as they need a greater amount of copper to ensure optimal performance and power transmission.
- Motor Type and Design: Different types of electric motors have varying copper requirements. For example, induction motors typically have copper rotor bars, while permanent magnet motors may have copper windings or coils. The design and construction of the motor determine the amount and placement of copper components within it.
- Efficiency Standards: Motors designed for high efficiency often require additional copper in their windings. This is because copper’s excellent electrical conductivity helps to minimize energy losses and improve overall efficiency. Motors adhering to stringent efficiency standards, such as those set by regulatory bodies, may have higher copper content to meet the efficiency requirements.
- Operating Conditions and Environment: The operating conditions and environment in which a motor operates can impact the amount of copper used. Motors exposed to extreme temperatures, corrosive atmospheres, or demanding industrial applications may require additional copper for improved thermal management, corrosion resistance, and reliability.
- Design Optimization: Motor design optimization techniques can also influence copper content. By utilizing advanced design methodologies, engineers can minimize copper losses, reduce winding resistance, and optimize magnetic field distribution. These optimizations can result in more efficient motors that require less copper while maintaining performance.
- Copper Price and Availability: The cost and availability of copper can also impact the copper content in electric motors. Fluctuations in copper prices or availability may encourage manufacturers to find innovative ways to optimize the use of copper or explore alternative materials with comparable properties.
It’s important to note that these factors are interdependent, and a combination of these factors ultimately determines the copper content in electric motors. Motor designers and manufacturers carefully consider these factors to strike a balance between performance, efficiency, cost, and environmental considerations.
In summary, factors such as motor size and power, motor type and design, efficiency standards, operating conditions, design optimization, and copper price and availability all play a role in determining the copper content in electric motors. By considering these factors, motor manufacturers can design and produce motors that meet specific performance requirements while optimizing the use of copper.
Recycling Copper from Electric Motors
Recycling copper from electric motors is an important practice for several reasons, including resource conservation, waste reduction, and environmental sustainability. Electric motors contain valuable copper components that can be recovered and reused, minimizing the need for new copper extraction. Here’s an overview of the recycling process and its benefits:
- Collection and Disassembly: The recycling process begins with the collection of electric motors for recycling. Once collected, the motors are disassembled to separate the copper components from other materials. This involves removing non-copper elements, such as the iron casing, plastic housing, and other non-metal components.
- Copper Recovery: After disassembly, the copper components, such as the windings and rotor bars, are further processed to extract the copper. This typically involves shredding the components and using mechanical or electromagnetic separators to separate the copper from other metals or contaminants.
- Copper Refining: Once the copper is separated, it undergoes a refining process to remove impurities and improve its quality. This refining process involves melting the copper and purifying it through various techniques, such as electrolysis, to achieve a high-purity copper product.
- Copper Reuse and Recycling: The recovered copper can then be reused or sold for various applications. It can be used as raw material to produce new copper products, including new motors. By reusing the copper from electric motors, the demand for new copper extraction is reduced, leading to significant resource conservation.
- Environmental Benefits: Recycling copper from electric motors offers several environmental benefits. Firstly, it helps reduce the need for mining and refining of new copper, which requires significant energy and can lead to environmental pollution. Additionally, recycling reduces the amount of waste sent to landfills, minimizing the environmental impact associated with disposal.
- Economic Considerations: Recycling copper from electric motors can also have economic advantages. It helps create job opportunities in the recycling industry and reduces raw material costs for copper manufacturers. Additionally, it reduces reliance on imported copper, enhancing domestic supply and promoting local economic growth.
Recycling copper from electric motors is an integral part of the circular economy, where materials are recycled and reused to minimize waste and conserve resources. It is crucial to raise awareness and encourage proper disposal and recycling practices to maximize the environmental and economic benefits of copper recycling.
In summary, the recycling of copper from electric motors involves collecting, disassembling, and extracting the copper components for reuse or refining. This practice conserves resources, reduces waste, and has environmental and economic advantages. Recycling copper from electric motors contributes to a more sustainable and efficient use of this valuable material.
Conclusion
Electric motors are essential components found in a wide range of devices, from everyday household appliances to industrial machinery. Copper plays a critical role in these motors, contributing to their performance, efficiency, and overall functionality. The copper windings, rotor bars, busbars, and other components enable efficient power transmission, effective heat dissipation, and reliable electrical connections.
Determining the amount of copper in electric motors can be done through various methods, such as weighing, disassembly and analysis, X-ray fluorescence spectrometry, and chemical analysis. Understanding the factors that affect copper content, including motor size, design, efficiency requirements, and operating conditions, provides insights into the variability in copper quantities among different motors.
Recycling copper from electric motors is a crucial practice that promotes resource conservation, waste reduction, and environmental sustainability. By collecting, disassembling, and refining the copper components, valuable copper can be recovered and reused, reducing the need for new copper extraction. Recycling not only conserves resources but also has economic benefits and reduces environmental impacts associated with mining and disposal.
In conclusion, copper is a vital element in electric motors, enabling efficient energy conversion and reliable motor operation. Its high electrical and thermal conductivity, mechanical properties, and resistance to corrosion make it an ideal material for motor components. Through proper recycling practices, we can maximize the reuse of copper from electric motors, contributing to a more sustainable and efficient use of this valuable resource.
Curious about how much more there is to learn after discovering the copper content in electric motors? Dive into our next feature where we focus on how well these machines perform their tasks. In the upcoming article, we unpack the secrets behind electric motor efficiency, shedding light on what makes some motors outshine others in terms of performance. Don't miss out on understanding the intricacies that contribute to making an electric motor not just good, but great at what it does.
Frequently Asked Questions about How Much Copper Is In An Electric Motor
Was this page helpful?
At Storables.com, we guarantee accurate and reliable information. Our content, validated by Expert Board Contributors, is crafted following stringent Editorial Policies. We're committed to providing you with well-researched, expert-backed insights for all your informational needs.
0 thoughts on “How Much Copper Is In An Electric Motor”