Home>diy>Building & Construction>How Long Does It Take To Build A Foundation
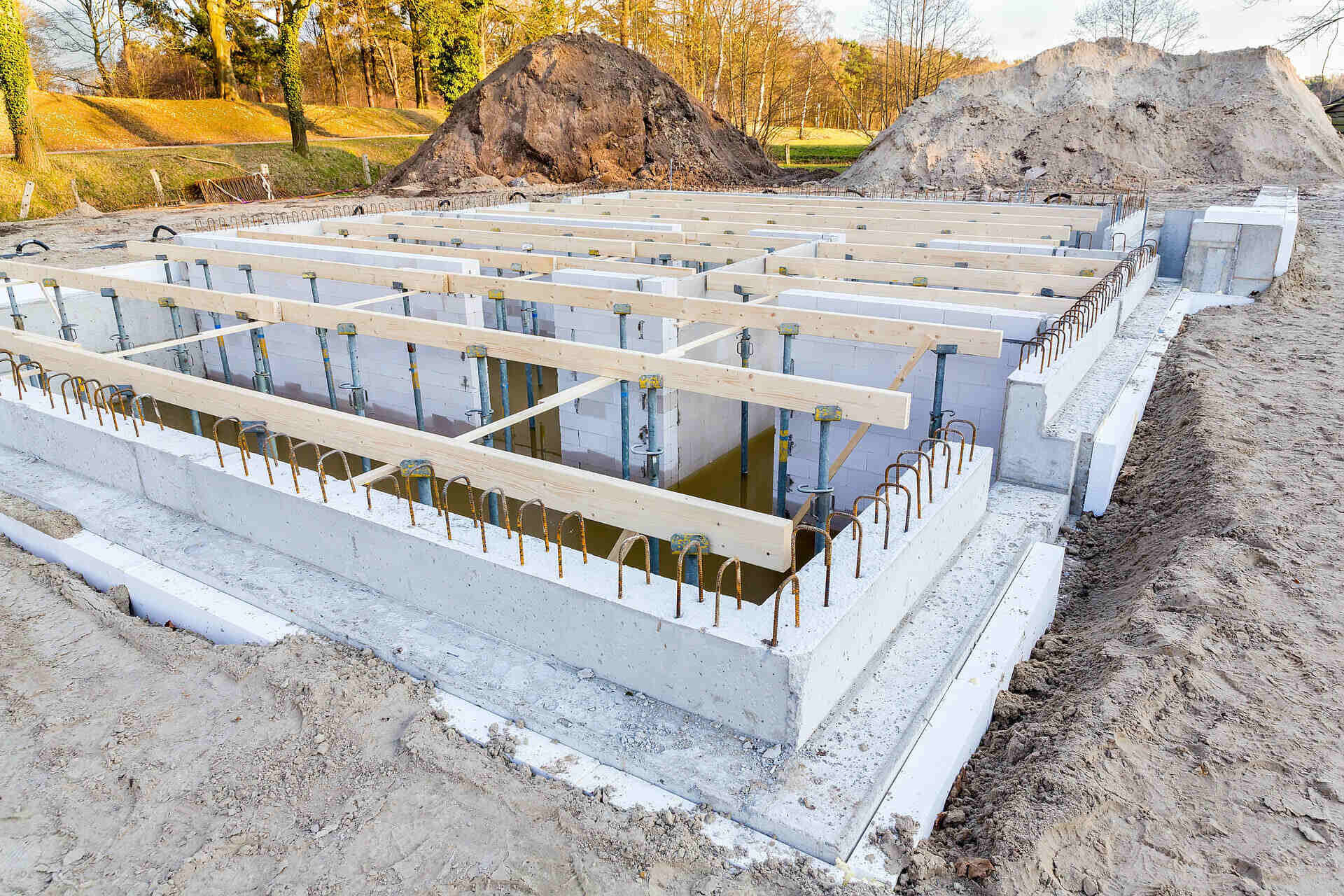
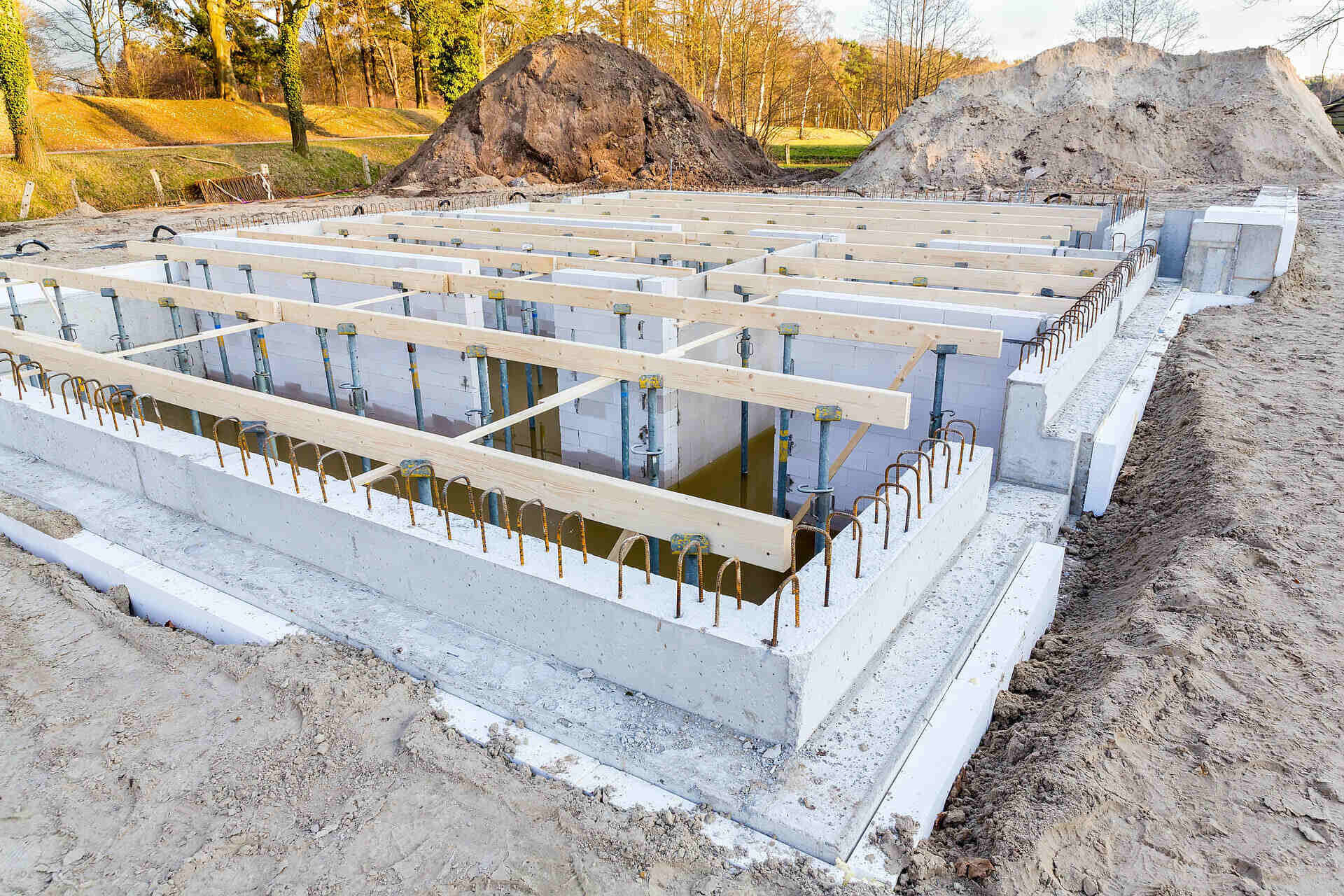
Building & Construction
How Long Does It Take To Build A Foundation
Modified: February 27, 2024
Learn about the time it takes to build a solid foundation in the construction industry. Find out the key factors that impact the duration and efficiency of the building process.
(Many of the links in this article redirect to a specific reviewed product. Your purchase of these products through affiliate links helps to generate commission for Storables.com, at no extra cost. Learn more)
Introduction
Building a solid foundation is essential for any construction project. It is the very first step in erecting a sturdy and durable structure. However, one common question that arises in the minds of homeowners and builders is how long it takes to build a foundation. The answer to this question depends on various factors and considerations.
In this article, we will explore the factors that affect foundation construction time and the steps involved in building a foundation. By understanding these aspects, you can better plan and manage your construction project.
Key Takeaways:
- Building a solid foundation involves various factors such as soil conditions, building size, and access constraints, impacting construction timelines. Proper planning and collaboration with experts are crucial for a successful construction project.
- The foundation construction process includes site preparation, footing installation, formwork, concrete pouring, backfilling, and waterproofing. Each step requires attention to detail, adherence to regulations, and collaboration with experienced professionals for a robust foundation.
Read more: How Long Does It Take To Repair A Foundation
Factors That Affect Foundation Construction Time
Several factors influence the duration of foundation construction. These factors can vary from one project to another and have a significant impact on the overall timeline. Let’s delve into the main factors that affect foundation construction time:
- Type of Foundation: Different types of foundations, such as slab-on-grade, crawl space, or basement, have varying complexities and construction methods. Each type requires different preparation and construction time, with basements typically taking the longest due to excavation and waterproofing requirements.
- Soil Conditions: The nature and stability of the soil play a crucial role in foundation construction. If the soil requires extensive excavation, stabilization, or geotechnical measures, the construction time can be significantly longer. Additionally, poor soil conditions may necessitate additional foundation strengthening, further extending the construction timeframe.
- Building Size and Complexity: The size and complexity of the building directly affect the foundation construction time. Larger structures or buildings with intricate designs and structural requirements may take longer to build a suitable foundation. This is because they often require more extensive excavation, reinforcement, and intricate formwork.
- Access and Site Constraints: The accessibility of the construction site and any existing site constraints can impact the speed of foundation construction. Difficulties in accessing the site or limited space to maneuver construction equipment may slow down the construction process. Additionally, if there are nearby structures that need protection or if there are utility lines that need to be relocated, it can further delay the foundation construction.
- Weather and Seasonal Considerations: Construction projects are subject to weather conditions, and certain seasons may be more challenging for foundation construction. Adverse weather conditions such as heavy rain, extreme cold, or high winds can delay foundation work and increase the overall construction time. In such cases, it may be necessary to wait for favorable weather conditions or implement additional precautions to ensure the quality of the foundation.
- Available Resources and Workforce: The availability of resources and workforce can significantly impact the timeline of foundation construction. Sufficient manpower, skilled workers, and the availability of construction materials and equipment are crucial for efficient and timely construction. Lack of resources or delays in material deliveries can extend the foundation construction time.
These factors collectively determine the duration required to build a foundation. It is important to consider all these aspects during the planning phase of your construction project to set realistic expectations and ensure smooth progress throughout the process.
Type of Foundation
The type of foundation chosen for a construction project is a crucial factor that affects the overall timeline of construction. Different types of foundations have varying complexities and construction methods, which directly impact the time required for completion.
Here are some common types of foundations and their associated construction times:
- Slab-on-Grade: A slab-on-grade foundation is a concrete slab poured directly on the ground. It is the simplest and quickest type of foundation to construct. The process involves site preparation, compacting the soil, installing a vapor barrier, placing the reinforcement, and pouring and curing the concrete. On average, this type of foundation can be completed within a few days to a week, depending on the size and intricacy of the project.
- Crawl Space: A crawl space foundation involves supporting the building on short walls, creating a space between the ground and the floor of the building. This type of foundation requires excavation, footings, the installation of support walls, and the implementation of proper ventilation and insulation. The construction time for a crawl space foundation can range from a few weeks to a couple of months, depending on the size and complexity of the project.
- Basement: Building a basement foundation is the most time-consuming type of foundation construction. It involves more extensive excavation, including digging down to the desired basement depth, creating walls and footings, installing drainage systems, and waterproofing the foundation. Basement construction can take several months to complete, with the exact duration depending on the size of the basement, site conditions, and weather factors.
- Pile Foundation: Pile foundations are used in areas with poor soil conditions or when a deeper foundation is required. This type of foundation involves driving or drilling piles into the ground and then constructing beams or slabs on top of these piles. The construction time for pile foundations can vary significantly depending on factors such as the number of piles, the depth required, and the type of piles used.
It’s important to note that the construction time mentioned above is an estimate and can vary depending on various factors specific to each project. Additionally, unforeseen challenges or changes in design can also impact the construction timeline. Therefore, it is essential to work closely with your contractor and architects to develop a realistic schedule for foundation construction.
Soil Conditions
The soil conditions at a construction site play a significant role in determining the time required to construct a foundation. The stability and characteristics of the soil can impact the construction process and may require additional steps to ensure a solid foundation.
Here are some ways in which soil conditions can affect foundation construction time:
- Excavation: The nature of the soil can determine the ease or difficulty of excavation. Hard or rocky soil may require more time and effort to excavate, especially if specialized equipment or techniques are needed. Conversely, loose or sandy soil may be easier to excavate, but it might require additional measures to ensure stability and prevent shifting.
- Stabilization: In some cases, the soil may need to be stabilized before foundation construction can begin. This is particularly true if the soil is too soft or has a high water content. Stabilization methods, such as soil compaction, soil grouting, or the use of geotextiles, may be necessary, and these additional steps can extend the overall construction time.
- Geotechnical Measures: Poor soil conditions, such as expansive clay or areas with a high water table, may require additional geotechnical measures to ensure the stability of the foundation. This can include installing deep pilings, creating a specialized foundation design, or implementing soil improvement techniques. These measures typically add complexity to the construction process and can significantly increase the time required to complete the foundation.
- Testing and Analysis: Before starting foundation construction, it is crucial to assess the soil conditions thoroughly. This involves conducting soil tests to determine its composition, strength, and load-bearing capacity. The testing and analysis process can take time, but it is essential for designing an appropriate foundation that will withstand the soil conditions and prevent future issues.
Since soil conditions can vary greatly from one site to another, it is essential to conduct a thorough soil investigation before beginning foundation construction. This will help in understanding the specific soil conditions and implementing appropriate measures to ensure a stable and long-lasting foundation.
Working with experienced geotechnical engineers and foundation contractors is crucial to assess and address any soil-related challenges effectively. By investing time and effort to properly manage soil conditions, you can minimize potential issues and optimize the construction timeline.
Building Size and Complexity
The size and complexity of a building have a direct impact on the time required for foundation construction. Larger buildings or structures with intricate designs and structural requirements typically require more time and effort to construct a suitable foundation.
Here are some key factors related to building size and complexity that can affect the foundation construction time:
- Excavation: The size of the building will determine the extent of excavation required for the foundation. Larger buildings may require deeper and wider excavations to accommodate the necessary footings and foundation structures. This process can take longer, especially if there are site constraints or challenging soil conditions.
- Reinforcement: Complex or larger buildings often require additional reinforcement within the foundation structure. This can involve the installation of more steel rebar or the use of specialized reinforcement techniques. The process of planning, fabricating, and installing the reinforcement can add considerable time to the construction process.
- Formwork: Buildings with intricate designs may require complex formwork systems to shape the foundation. Formwork refers to the temporary molds or structures used to hold freshly poured concrete in place until it hardens. The design and installation of complex formwork can be time-consuming, especially when dealing with unique shapes or unconventional architectural features.
- Poor Ground Conditions: In some cases, the size and complexity of a building may require additional measures to mitigate the potential risks associated with poor ground conditions. This can include special foundation designs, such as deep pilings, or the use of specialized materials to improve the stability of the foundation. These additional steps can extend the construction time to ensure a solid and safe foundation.
It is crucial to consider the size and complexity of the building during the initial planning and design stages to accurately estimate the foundation construction time. Working closely with architects, structural engineers, and foundation contractors will help in identifying any unique challenges or requirements that may impact the timeline.
While larger or more complex buildings may require additional time for the foundation construction, it is essential to prioritize quality and structural integrity. Cutting corners to save time can lead to long-term issues and costly repairs. By investing the necessary time and effort into the foundation construction, you can ensure a strong and stable base for your building.
Access and Site Constraints
The access to a construction site and any existing site constraints can have a significant impact on the time required for foundation construction. Difficulties in accessing the site or limited space to maneuver construction equipment can slow down the construction process and extend the overall timeline.
Here are some factors related to access and site constraints that can affect foundation construction time:
- Site Location: The location of the construction site plays a crucial role in determining the accessibility and ease of construction. Sites located in remote or hard-to-reach areas may require additional time for transporting equipment, materials, and workforce. In contrast, sites located in urban areas with traffic congestion or limited parking space can add delays and logistical challenges to the construction process.
- Existing Structures: If there are existing structures adjacent to the construction site, precautions must be taken to ensure their protection during the foundation construction. This may involve reinforcing adjacent structures, installing temporary support systems, or implementing vibration and noise control measures. These steps can extend the construction time but are necessary to prevent any damage to nearby properties.
- Utility Lines and Services: The presence of utility lines, such as water, gas, electricity, or sewage lines, can significantly impact the foundation construction time. In some cases, utility lines may need to be relocated or temporarily disconnected to allow for excavation and construction. Coordinating with utility companies and obtaining the necessary permits can add time to the construction process.
- Site Geometry and Grading: The shape and topography of the construction site can affect the construction process. Irregular site geometry or steep slopes may require additional excavation and leveling, which can add time to the foundation construction. Special retaining walls or erosion control measures may also be necessary to ensure stability during the construction process.
- Space Constraints: Limited space on the construction site can pose challenges for equipment storage, material handling, and maneuvering construction machinery. This can slow down the foundation construction process and necessitate creative solutions, such as using smaller equipment or coordinating deliveries and storage off-site.
It is crucial to conduct a thorough site assessment before commencing foundation construction to identify any access or site constraints. This will allow the project team to plan and strategize accordingly, ensuring efficient and timely construction.
Coordinating with local authorities, utility companies, and neighboring property owners is also important to address any potential issues related to access and site constraints. By proactively managing these challenges, you can minimize delays and streamline the construction process.
Weather and Seasonal Considerations
Weather conditions and seasonal factors have a significant impact on foundation construction timelines. Adverse weather can affect the construction process, resulting in delays and potential complications. It is essential to consider weather conditions and plan construction activities accordingly to minimize setbacks.
Here are some weather and seasonal considerations that can affect foundation construction time:
- Heavy Rain: Rainy weather can significantly impact foundation construction, particularly during the excavation and concrete pouring stages. Excessive rainfall can make the site muddy and unstable, making it challenging to excavate and pour concrete properly. It is important to wait for suitable weather conditions to ensure the quality of the foundation.
- Extreme Cold: Extremely low temperatures can affect the setting and curing of concrete, leading to potential strength issues. Cold weather may require additional precautions, such as using insulating blankets or heaters, to ensure proper concrete curing. In some cases, construction may need to be delayed until temperatures are more favorable for successful curing.
- High Winds: Strong winds can pose a safety hazard during foundation construction. It may be necessary to halt construction activities if winds reach dangerous levels, particularly when working at heights or handling large construction materials. Construction schedules may need to be adjusted to avoid high-wind periods.
- Frost and Thaw: In colder climates, the ground may freeze during the winter, making it difficult to dig and pour footings. Frost can also cause heaving and shifting of the soil, which can compromise the stability of the foundation. Construction during the winter months may require special techniques, such as using heated enclosures or thawing the ground, to ensure successful foundation construction.
- Seasonal Restrictions: Some regions may have specific seasonal restrictions or regulations that impact construction activities. For example, certain areas may have restrictions on construction during bird nesting season or environmentally sensitive periods. It is essential to be aware of and adhere to any local regulations to avoid potential delays or penalties.
Considering weather and seasonal factors during the planning phase of the project is crucial. Construction schedules should be developed with contingency plans to account for potential weather-related delays. Monitoring weather forecasts regularly and coordinating construction activities accordingly can help minimize the impact of adverse weather conditions.
Working with experienced contractors who are familiar with local weather patterns and construction practices can also help in effectively managing weather-related challenges during foundation construction.
Available Resources and Workforce
The availability of resources and a skilled workforce is a crucial factor that can significantly impact the timeline of foundation construction. Sufficient manpower, construction materials, and equipment are essential for efficient and timely construction.
Here are some key considerations related to available resources and workforce that can affect foundation construction time:
- Manpower: The availability of skilled labor is vital for the smooth progress of foundation construction. Having an adequate number of workers with the necessary skills and experience can help expedite the construction process. A shortage of skilled labor can lead to delays in completing critical tasks, including excavation, concrete pouring, and reinforcement installation.
- Construction Materials: Timely availability of construction materials, such as concrete, reinforcement bars, formwork, and waterproofing materials, is essential for uninterrupted foundation construction. Delays in material deliveries can significantly impact the construction schedule, potentially leading to project delays. Effective coordination with suppliers and proactive material procurement planning are crucial to ensure a smooth construction process.
- Construction Equipment: The right equipment is necessary to perform various tasks during foundation construction. Excavators, concrete mixers, cranes, and other specialized machinery are often needed. Having access to properly maintained and functioning equipment not only improves efficiency but also reduces the risk of delays caused by equipment breakdowns.
- Specialized Skills: Some foundation construction projects may require specialized skills or expertise, such as working with complex formwork systems or implementing advanced foundation techniques. Ensuring that the project team has access to individuals with the necessary expertise is crucial. If specialized skills are not readily available, additional time may be required for training or subcontracting work to external experts.
- Project Management: Effective project management is essential for coordinating resources and ensuring smooth progress throughout the construction process. Efficient scheduling, clear communication, and proactive problem-solving are key factors that can help optimize the use of available resources and reduce potential bottlenecks that may slow down foundation construction.
Managing resources and workforce effectively requires careful planning and coordination. It is important to assess resource availability at the initial stages of the project and continually monitor and adjust as needed to keep the construction timeline on track.
Collaborating with experienced contractors, subcontractors, and suppliers who have a proven track record in foundation construction can be beneficial. Their expertise and established network of resources can help ensure that the necessary manpower, materials, and equipment are available when needed, ultimately contributing to a more efficient and timely foundation construction process.
The time it takes to build a foundation can vary depending on factors such as the size of the building, soil conditions, and weather. Generally, it can take anywhere from a few days to a few weeks to complete the foundation construction.
Steps Involved in Building a Foundation
Building a solid foundation involves a series of essential steps that ensure the stability and durability of a structure. While the specific details may vary depending on the type of foundation and site conditions, the following steps provide a general overview of the foundation construction process:
- Site Preparation and Excavation: The first step is to prepare the construction site by clearing any vegetation, debris, or obstacles. Then, excavation takes place to remove the topsoil and create a level surface for the foundation. This stage may also involve establishing the layout and dimensions of the foundation.
- Footing Installation: Footings are essential components that distribute the weight of the structure and provide stability. This step involves excavating trenches for the footings and then constructing and installing them according to the structural design and building code requirements. The footings are typically made of reinforced concrete and extend below the frost line.
- Formwork and Reinforcement: The next step is to create formwork, which is a temporary structure that holds the concrete in place as it is poured. The formwork is designed to ensure the desired shape and dimensions of the foundation. Reinforcement, such as steel rebar, is then installed within the formwork to provide additional strength and support to the foundation.
- Concrete Pouring and Curing: Once the formwork and reinforcement are in place, the next step is to pour the concrete into the prepared area. The concrete is carefully poured and spread evenly, taking care to prevent voids or unevenness. After pouring, the concrete needs to cure, which involves allowing it to harden and gain strength over time. Curing typically takes several days, during which proper moisture and temperature control are essential.
- Backfilling and Compaction: After the concrete has adequately cured, the excavation trenches around the foundation can be backfilled with soil or other approved materials. This step helps to provide additional support and stability to the foundation. Proper compaction of the backfilled material is crucial to minimize the risk of settlement or shifting.
- Foundation Waterproofing: Depending on the site conditions and building requirements, applying a waterproofing membrane or coating to the foundation may be necessary. This step helps to protect the foundation from the intrusion of water and moisture, preventing potential issues such as leaks or damage to the structure.
It’s important to note that each of these steps requires careful planning, adherence to building codes and regulations, and the involvement of skilled professionals, including architects, engineers, and contractors. Accurate execution of each step ensures the stability and integrity of the foundation, laying the groundwork for a successful construction project.
The timeline for completing these steps can vary depending on factors such as the size and complexity of the building, soil conditions, site constraints, and weather conditions. Efficient project management and coordination with the construction team are crucial to ensure smooth progress and timely completion of the foundation construction process.
Site Preparation and Excavation
Before construction of a foundation can begin, the site must undergo thorough preparation and excavation. This initial stage sets the groundwork for the construction process and involves several important steps:
- Site Survey: The first step in site preparation is to conduct a detailed survey of the land. This involves assessing the topography, identifying any potential obstacles or hazards, and determining the most suitable location for the foundation. A survey helps ensure that the foundation is built on stable ground and that any site-specific considerations are taken into account.
- Clearing and Demolition: Once the survey is complete, the construction site needs to be cleared of any existing structures, vegetation, or debris. This typically entails demolishing any existing buildings or structures and removing trees, rocks, or other obstructions that could interfere with the foundation construction process.
- Marking and Layout: After clearing the site, the next step is to mark and layout the foundation’s dimensions on the ground. This is typically done using stakes and string lines, ensuring that the placement of the foundation aligns with the architectural and engineering plans. Accurate marking and layout are crucial to ensure the foundation is built in the correct position.
- Excavation: Excavation involves digging the ground to create a space for the foundation. This process is done using heavy machinery such as excavators, backhoes, or bulldozers. Excavation depth and dimensions are determined by the type of foundation being constructed, local building codes, and site-specific requirements.
- Soil Removal and Disposal: During excavation, the soil that is dug up needs to be removed from the site. The soil may be taken off-site for disposal or repurposed for other purposes if deemed suitable. Proper soil disposal ensures a clean and well-prepared construction site.
- Site Grading: After excavation, the site may need to be graded to create a level and even platform for the foundation. This involves adding or removing soil where necessary to achieve the desired slope and to ensure proper drainage away from the structure.
- Site Stabilization: In some cases, the soil at the construction site may require stabilization to enhance its load-bearing capacity. This can involve techniques such as soil compaction, adding geotextiles or geogrids, or implementing ground improvement methods to make the soil more stable and suitable for the foundation.
Site preparation and excavation are critical steps that lay the foundation (pun intended) for a successful construction project. Accurate surveying, thorough clearing, and precise excavation set the stage for the subsequent stages of foundation construction. It is important to work with experienced professionals who are familiar with local building codes and regulations to ensure compliance and optimal execution of these initial site preparation steps.
The duration of site preparation and excavation can vary depending on factors such as the size and complexity of the project, site conditions, and the efficiency of the construction team. Proper management of these stages is essential to keep the construction timeline on track and ensure a solid foundation for the rest of the building.
Footing Installation
One of the crucial steps in building a solid foundation is the installation of footings. Footings provide a stable base that supports the weight of the structure and helps distribute the load evenly to the underlying soil. The process of footing installation involves several key steps:
- Excavation and Trench Preparation: The first step in footing installation is to excavate trenches in the soil where the footings will be placed. The depth and width of the trenches depend on the design and structural requirements of the foundation. The soil in the trenches must be carefully compacted to provide a stable foundation for the footings.
- Footing Design: Prior to the installation, the footing design is carefully planned and engineered to ensure it can support the load of the structure. The design takes into account factors such as the type of foundation, soil conditions, and the anticipated load the footings will bear to determine the appropriate dimensions and reinforcement requirements.
- Formwork Construction: Once the trenches are prepared, formwork is constructed to provide a temporary mold or structure that will contain the concrete during the pouring and curing process. The formwork must be properly aligned and secured to ensure the footings are poured to the desired dimensions and shape.
- Reinforcement Placement: Reinforcing steel bars, commonly referred to as rebar, are installed within the formwork before the concrete is poured. The rebar provides added strength and helps withstand tension and structural forces. The proper placement and spacing of the rebar are essential to ensure the structural integrity of the footings.
- Concrete Pouring: Once the formwork and reinforcement are in place, the next step is to pour the concrete into the trenches. The concrete mixture should meet the specified strength and composition requirements. Care should be taken to evenly distribute the concrete within the formwork, ensuring that it fills all areas completely without voids or gaps.
- Finishing and Curing: After the concrete has been poured, it is necessary to finish the surface of the footings and ensure they are properly cured. Finishing may involve smoothing the top surface, removing any excess material, and ensuring proper slope or grading. Curing involves providing the right conditions, such as maintaining moisture and temperature levels, to allow the concrete to harden and gain strength over time.
It is crucial to ensure that the footing installation is carried out in accordance with local building codes, regulations, and engineering specifications. Choosing the appropriate footing design, using high-quality materials, and adhering to proper installation procedures are key factors in creating a strong and stable foundation for the structure.
The duration of footing installation can vary depending on factors such as the size and complexity of the project, soil conditions, and the efficiency of the construction team. It is important to work with experienced professionals who have a strong understanding of structural engineering and foundation construction to ensure that the footings are installed correctly and can adequately support the structure for years to come.
Formwork and Reinforcement
Formwork and reinforcement are integral components in the construction of a solid foundation. Formwork serves as a temporary mold or structure that contains the poured concrete, while reinforcement provides additional strength and structural integrity. The process of formwork and reinforcement involves several key steps:
- Formwork Design and Construction: The formwork is designed to shape the concrete into the desired dimensions and contours of the foundation. This involves determining the size, shape, and alignment of the formwork components. Formwork can be made from various materials such as wood, metal, or prefabricated plastic panels. It is essential to ensure that the formwork is adequately designed to withstand the pressure of the concrete as it is poured and to maintain the desired shape.
- Formwork Installation: Once the formwork design is finalized, it is time to install the formwork. This process involves carefully positioning and securing the formwork in the excavated area where the foundation will be poured. The formwork needs to be properly aligned, leveled, and checked for stability. It is crucial to ensure that the formwork is rigid and well-supported to prevent any movement or deformation during the pouring and curing of the concrete.
- Reinforcement Placement: Reinforcing steel bars, commonly known as rebar, are laid inside the formwork before the concrete is poured. The rebar provides strength, tensile capacity, and durability to the foundation. The placement and spacing of the rebar are determined by engineering calculations and the structural design requirements. The rebar is tied together using wire or steel ties to create a mesh grid or framework that will reinforce the concrete.
- Additional Reinforcement Elements: In addition to the main rebar framework, other reinforcement elements may be needed depending on the design and requirements of the foundation. These may include dowel bars, anchor bolts, or additional supports to provide structural connectivity and integrity.
- Reinforcement Inspection and Quality Control: Before pouring the concrete, it is important to conduct a thorough inspection of the reinforcement placement. This ensures that the rebar is correctly positioned, adequately tied, and meets the design requirements. Quality control measures are implemented to check the rebar for cleanliness, proper size, and any potential defects that could compromise the integrity of the foundation.
The proper installation of formwork and reinforcement is crucial to the strength and stability of the foundation. It is essential to follow engineering design specifications, local building codes, and industry best practices to ensure that the formwork is accurately constructed and the reinforcement is precisely placed.
The duration of formwork and reinforcement installation can vary depending on factors such as the size and complexity of the project, the type of formwork material used, and the intricacy of the reinforcement design. It is vital to work with experienced professionals who have expertise in formwork and reinforcement installation to ensure the proper execution of these critical foundation construction steps.
Concrete Pouring and Curing
The process of concrete pouring and curing is a critical stage in the construction of a foundation. It involves the careful placement of concrete into the prepared formwork, followed by a controlled curing process to allow the concrete to harden and achieve its desired strength. The steps involved in concrete pouring and curing are as follows:
- Mixing the Concrete: The first step is to prepare the concrete mixture by combining cement, aggregates (such as sand and gravel), and water in the appropriate proportions. The mixture is thoroughly mixed using a concrete mixer truck or a batch plant to ensure a consistent and uniform blend.
- Preparing the Formwork: Prior to pouring the concrete, the formwork must be checked for proper alignment and stability. Any gaps or openings in the formwork must be sealed to prevent the concrete from leaking or spilling out.
- Pouring the Concrete: The mixed concrete is then poured into the formwork using buckets, chutes, or a concrete pump. It is essential to ensure that the concrete is evenly distributed throughout the formwork and that there are no voids or air pockets. Care should be taken not to dislodge the reinforcement or disturb the alignment of the formwork during the pouring process.
- Consolidating the Concrete: Once the concrete is poured into the formwork, it must be properly consolidated to remove any trapped air or voids. This is typically done using mechanical vibration or by manually using vibrating tools. Proper consolidation helps achieve a dense and homogeneous mixture that enhances the strength and durability of the foundation.
- Finishing the Surface: After consolidation, the surface of the concrete can be finished to achieve the desired texture and appearance. This can include smoothing the top surface, removing excess material, and creating proper slopes or grading. Finishing may be done using trowels, floats, or other tools, depending on the desired finish.
- Curing the Concrete: Curing is a crucial step that involves providing the necessary conditions for the concrete to gain strength and durability. This typically involves keeping the concrete moist and maintaining a favorable temperature for a specified period. Curing can be achieved by various methods, such as covering the concrete with plastic sheeting, using curing compounds, or continuously wetting the surface through a process known as wet curing.
- Curing Time: The duration of the curing process depends on several factors, including the type of concrete used, environmental conditions, and the desired strength of the foundation. Typically, the initial curing period lasts around seven days, during which the concrete gradually gains strength. However, full strength development can take several weeks or even months.
Proper concrete pouring and curing are vital to ensure the integrity and durability of the foundation. It is essential to follow proper construction practices, including accurate mixing ratios, adequate consolidation, and precise curing methods, to achieve optimal results.
The duration of concrete pouring and curing can vary depending on factors such as the size and complexity of the foundation, weather conditions, and the type of concrete mix used. Close monitoring of the curing process, including regular moisture checks, temperature control, and protection from adverse weather conditions, is crucial to ensure the successful development of a strong foundation.
Backfilling and Compaction
After the concrete has cured and the foundation is structurally sound, the next step in the foundation construction process is backfilling and compaction. Backfilling involves filling the area surrounding the foundation with soil or other approved materials, while compaction ensures that the backfilled material is properly packed and stabilized. The process of backfilling and compaction includes the following steps:
- Excavation Inspection: Before backfilling can begin, the excavated area and the foundation must be inspected to verify that it meets the required standards and construction plans. Any deficiencies or issues must be addressed before proceeding.
- Backfill Material Selection: The selection of the backfill material is critical to ensure stability and proper drainage around the foundation. Common materials used for backfilling include native soil, crushed stone, or a combination of both. The proper type and quality of backfill material should be determined based on soil conditions, engineering recommendations, and local building codes.
- Layered Backfilling: Backfilling is typically done in layers, with each layer compacted before the next one is added. This process helps to ensure even settlement and proper compaction throughout the backfilled area. The thickness of each layer may vary depending on the specific project requirements.
- Compaction: Compaction is the process of mechanically compressing the backfill material to increase its density and remove any voids or air pockets. Compaction can be achieved using vibrating compaction equipment, compaction rollers, or other appropriate tools. The specific compaction method and equipment used will depend on the type of backfill material being used.
- Moisture Control: Controlling moisture content is crucial for effective compaction. It is essential to ensure that the backfill material is neither too dry nor too wet; proper moisture content allows for optimal compaction. If the material is too dry, it may not compact properly, while excess moisture can lead to settlement issues or poor stability.
- Special Considerations: Additional considerations may be necessary for specific situations, such as the presence of underground utilities or structures near the foundation. In such cases, it is important to take extra precautions to avoid damage to infrastructure or to protect against potential settlement issues.
- Final Grading: Once the backfilling and compaction are complete, the area surrounding the foundation is graded to direct water away from the structure. Proper grading helps to prevent pooling or improper drainage, which could potentially compromise the integrity of the foundation.
Backfilling and compaction are critical steps in the foundation construction process as they provide stability and support to the foundation. Proper backfilling ensures that the load from the structure is evenly distributed, helps prevent settling, and protects against potential damage from water accumulation around the foundation.
The duration of backfilling and compaction depends on various factors, including the size and complexity of the project, the type of backfill material, and the efficiency of the compaction equipment. It is crucial to work with experienced professionals who have a deep understanding of soil mechanics and compaction techniques to ensure the successful completion of these foundation construction tasks.
Foundation Waterproofing
Foundation waterproofing is a crucial step in the construction process that helps protect the foundation and the structure above from water damage. It involves applying waterproofing materials and implementing proper drainage systems to prevent the intrusion of water or moisture into the foundation. The process of foundation waterproofing typically involves the following steps:
- Surface Preparation: Before applying any waterproofing materials, the surface of the foundation walls must be thoroughly cleaned and prepared. Any dirt, debris, or loose materials should be removed to ensure proper adhesion of the waterproofing membrane or coating.
- Choosing Waterproofing Materials: There are several types of waterproofing materials available, including liquid membranes, sheet membranes, and cementitious coatings. The selection of the appropriate material depends on factors such as the type of foundation, soil conditions, and local building codes. It is essential to choose high-quality waterproofing products that are specifically designed for foundation applications.
- Applying Waterproofing Membrane or Coating: The selected waterproofing material is then applied to the exterior surface of the foundation walls. This can be done using various methods such as spraying, brushing, or rolling, depending on the specific product and application instructions. Multiple coats may be required to achieve the desired level of waterproofing protection.
- Ensuring Proper Sealing: Special care should be taken to seal any joints, gaps, or penetrations in the foundation, such as pipe entry points or utility connections. These areas are potential weak spots where water can infiltrate, so it is important to use appropriate sealants or flashing to ensure a watertight seal.
- Installing Drainage Systems: In addition to waterproofing the foundation walls, it is essential to have proper drainage systems in place to redirect water away from the foundation. This can include the installation of footing drains, French drains, or sump pump systems, depending on site conditions and local regulations. These drainage systems help prevent water from collecting around the foundation, reducing the risk of water damage.
- Regular Inspections and Maintenance: Foundation waterproofing requires regular inspections to ensure that the system remains intact and effective. Periodic checks for any signs of moisture intrusion or damage should be performed. In cases where repairs or maintenance are necessary, it is crucial to address them promptly to maintain the integrity of the waterproofing system.
Foundation waterproofing is essential to protect a structure from moisture-related issues such as water leakage, mold growth, and structural damage. By preventing water from seeping through the foundation walls, waterproofing helps to maintain a dry and stable environment within the structure.
The duration of foundation waterproofing depends on factors such as the size of the foundation, the chosen waterproofing method, and site-specific requirements. It is essential to work with experienced contractors or waterproofing specialists who have a thorough understanding of waterproofing techniques and products to ensure the proper execution of this critical step in foundation construction.
Conclusion
Building a strong and durable foundation is an essential step in any construction project, as it sets the stage for a stable and long-lasting structure. The duration of foundation construction is influenced by various factors, including the type of foundation, soil conditions, building size and complexity, access and site constraints, weather considerations, and the availability of resources and workforce.
Understanding these factors and their impact on the construction timeline is crucial for effective project planning and management. By considering these aspects from the outset, homeowners and builders can set realistic expectations and ensure smooth progress throughout the construction process. Working closely with experienced professionals, such as architects, structural engineers, and contractors, is key to ensuring the proper execution of each step in the foundation construction process.
The foundation construction process typically includes site preparation and excavation, footing installation, formwork and reinforcement, concrete pouring and curing, backfilling and compaction, and foundation waterproofing. Each of these steps requires careful attention to detail and adherence to building codes and regulations to ensure a structurally sound and watertight foundation.
In conclusion, building a foundation requires a combination of knowledge, skill, and careful planning. From evaluating soil conditions to selecting the appropriate foundation type, every aspect contributes to the overall timeline of construction. By prioritizing quality, following industry best practices, and collaborating with experienced professionals, homeowners and builders can create a solid foundation that serves as a robust base for their construction project.
Remember, a strong foundation lays the groundwork for a successful and resilient structure that will stand the test of time.
Frequently Asked Questions about How Long Does It Take To Build A Foundation
Was this page helpful?
At Storables.com, we guarantee accurate and reliable information. Our content, validated by Expert Board Contributors, is crafted following stringent Editorial Policies. We're committed to providing you with well-researched, expert-backed insights for all your informational needs.
0 thoughts on “How Long Does It Take To Build A Foundation”