Home>Technology>Smart Home Devices>How To Make 3D Printer Designs
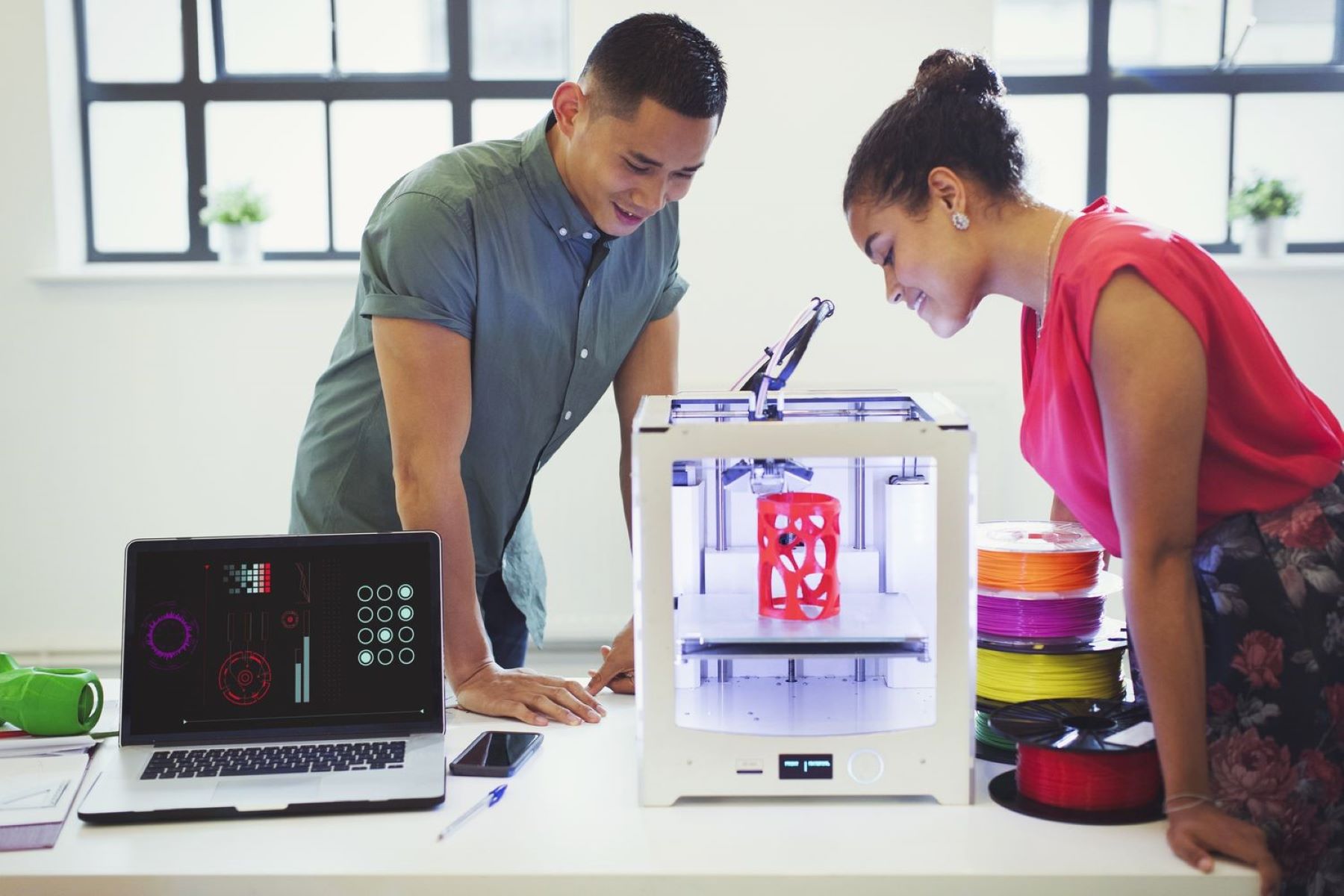
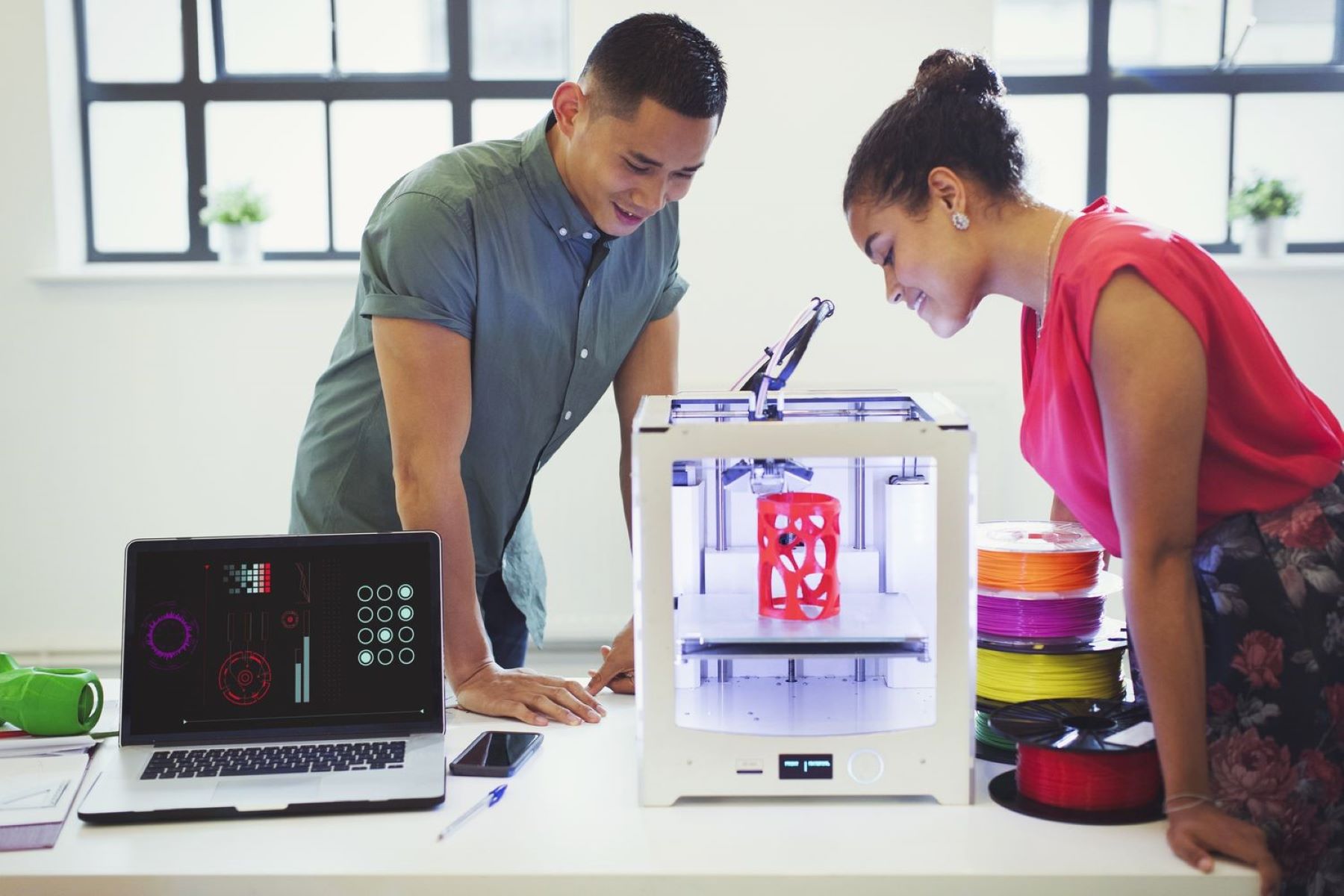
Smart Home Devices
How To Make 3D Printer Designs
Modified: August 20, 2024
Discover how to create custom 3D printer designs for smart home devices with our step-by-step guide. Learn the tips and tricks for successful printing.
(Many of the links in this article redirect to a specific reviewed product. Your purchase of these products through affiliate links helps to generate commission for Storables.com, at no extra cost. Learn more)
Introduction
Welcome to the exciting world of 3D printing! Whether you are a hobbyist, an entrepreneur, or a professional designer, creating your own 3D printer designs can be a rewarding and fulfilling endeavor. With the rapid advancement of technology, 3D printing has become more accessible than ever, allowing individuals to bring their innovative ideas to life in the form of tangible, three-dimensional objects.
In this comprehensive guide, we will explore the process of designing and creating 3D printer models, from understanding the fundamentals of 3D printing to selecting the right software, designing your model, testing and adjusting the design, and finalizing your 3D printer design. By the end of this journey, you will have the knowledge and confidence to embark on your own 3D printing projects and unleash your creativity in the realm of additive manufacturing.
So, let's dive into the fascinating realm of 3D printer design and discover the tools, techniques, and skills needed to transform your concepts into physical reality. Whether you are interested in crafting custom prototypes, personalized accessories, or intricate art pieces, 3D printing offers a world of possibilities, and this guide will serve as your roadmap to success.
Key Takeaways:
- Understanding 3D printing is essential for creating amazing designs. It involves depositing layers of material to bring digital models to life, offering endless possibilities for innovation and creativity.
- Choosing the right software and testing and adjusting your design are crucial steps in creating successful 3D printer designs. These processes ensure that your designs are optimized for printing and ready to become physical objects.
Read more: How To Make 3D Printer Faster
Understanding 3D Printing
Before delving into the intricacies of 3D printer design, it is essential to grasp the foundational principles of 3D printing technology. At its core, 3D printing, also known as additive manufacturing, involves the creation of three-dimensional objects from digital models by depositing successive layers of material, such as plastic, metal, or resin. This revolutionary process enables the production of complex geometries and customized designs with remarkable precision and efficiency.
There are several methods of 3D printing, including Fused Deposition Modeling (FDM), Stereolithography (SLA), Selective Laser Sintering (SLS), and Digital Light Processing (DLP), each offering unique advantages and applications. FDM, for instance, utilizes thermoplastic filaments that are extruded layer by layer to form the desired object, making it one of the most widely used and cost-effective 3D printing technologies.
Furthermore, understanding the role of 3D modeling software and digital design tools is crucial in the 3D printing process. These software applications enable users to create and manipulate 3D models, optimize geometries for printing, and ensure structural integrity and feasibility. From parametric design software like SolidWorks and Fusion 360 to user-friendly platforms such as TinkerCAD and Blender, the choice of software depends on the complexity of the design and the user’s proficiency.
Moreover, the material selection plays a pivotal role in 3D printing, as different materials exhibit varying properties, such as strength, flexibility, and heat resistance. Common 3D printing materials include PLA (Polylactic Acid), ABS (Acrylonitrile Butadiene Styrene), PETG (Polyethylene Terephthalate Glycol), and resin-based materials, each catering to specific applications and performance requirements.
By comprehending the fundamentals of 3D printing processes, technologies, software, and materials, aspiring designers and enthusiasts can embark on their 3D printer design journey with a solid understanding of the underlying mechanics and considerations involved in bringing their concepts to fruition.
Choosing the Right Software
When venturing into the realm of 3D printer design, selecting the appropriate software is a critical decision that significantly influences the design process and the quality of the final output. The choice of software hinges on the complexity of the design, the user’s familiarity with 3D modeling tools, and the specific requirements of the intended 3D print.
For beginners and casual designers, user-friendly software such as TinkerCAD and SketchUp provides a gentle learning curve and intuitive interfaces, allowing individuals to create basic 3D models without the steep learning curve associated with professional-grade software. These platforms are ideal for crafting simple prototypes, decorative objects, and personalized trinkets, catering to a broad audience seeking to explore the possibilities of 3D printing.
Conversely, professionals and experienced designers may opt for advanced 3D modeling software like Autodesk Fusion 360, SolidWorks, or Blender, which offer robust features for intricate design projects, engineering applications, and artistic endeavors. These sophisticated tools empower users to sculpt complex geometries, simulate mechanical assemblies, and perform finite element analysis, thereby catering to a diverse range of industries and design disciplines.
Furthermore, the compatibility of the software with the 3D printer and its file format requirements is a crucial factor to consider. Most 3D printers accept STL (Stereolithography) files, a standard format for 3D printing, but certain printers may have specific file format preferences or require additional plugins or slicer software for seamless integration with the chosen 3D modeling software.
Additionally, the availability of online resources, tutorials, and a supportive community can greatly influence the software selection process. Platforms with extensive documentation, video tutorials, and active user forums contribute to a conducive learning environment, enabling designers to enhance their skills, troubleshoot challenges, and stay updated with the latest trends and techniques in 3D printing and design.
By carefully evaluating the features, learning curves, compatibility, and support resources of various 3D modeling software, designers can make an informed decision and choose the right tool that aligns with their proficiency, project requirements, and long-term aspirations in the dynamic landscape of 3D printer design.
When designing for a 3D printer, make sure to consider the printer’s capabilities and limitations. Pay attention to details like overhangs, support structures, and print orientation to ensure a successful print.
Designing Your 3D Model
Embarking on the journey of designing a 3D model for printing is an exhilarating process that demands creativity, precision, and a keen understanding of the intended application. Whether crafting a functional prototype, an artistic sculpture, or a custom accessory, the design phase serves as the canvas for transforming ideas into tangible forms through the power of additive manufacturing.
The initial step in designing a 3D model involves conceptualization and visualization of the intended object. This phase often entails sketching ideas on paper, creating digital concept art, or leveraging 2D design software to outline the basic structure and features of the model. Clear visualization and planning lay the foundation for the subsequent stages of detailed modeling and refinement.
Subsequently, transitioning from conceptualization to 3D modeling entails the use of specialized software to sculpt, extrude, and manipulate geometric shapes, curves, and surfaces, giving rise to the digital representation of the envisioned object. Whether employing parametric modeling, sculpting, or polygonal modeling techniques, the goal is to iteratively refine the design, ensuring structural integrity, aesthetic appeal, and manufacturability.
During the design phase, considerations such as wall thickness, support structures, and assembly features play a pivotal role in optimizing the model for 3D printing. Designing with the printing process in mind involves strategically orienting the model, incorporating fillets and chamfers for strength and aesthetics, and integrating features that facilitate post-processing and assembly, if applicable.
Moreover, the choice of materials influences the design approach, as different materials exhibit distinct properties and constraints. For instance, designing a model intended for FDM 3D printing may necessitate accommodating layer adhesion and support material considerations, while designing for SLA printing may emphasize intricate details and resin compatibility.
Iterative refinement, feedback gathering, and virtual simulations, if applicable, contribute to honing the 3D model, ensuring that it meets the envisioned specifications and performance criteria. Collaborating with peers, leveraging design feedback platforms, and seeking expert advice can enrich the design process and lead to innovative solutions and enhancements.
By embracing a meticulous and iterative approach to 3D model design, creators can unleash their imagination, surmount design challenges, and ultimately materialize their concepts into physical objects that embody their ingenuity and vision.
Testing and Adjusting Your Design
As you progress through the iterative process of 3D printer design, the phase of testing and adjusting your design assumes paramount importance in ensuring the viability, functionality, and quality of the intended 3D print. This phase involves comprehensive evaluation, validation, and refinement of the 3D model to address potential issues, optimize performance, and prepare it for seamless translation into a physical object.
One of the fundamental aspects of testing the design involves conducting virtual simulations and analyses to assess structural integrity, stress distribution, and fluid dynamics, if applicable. Utilizing simulation software or integrated analysis tools within 3D modeling platforms enables designers to subject the model to real-world conditions, identify weak points, and iteratively reinforce critical areas to enhance durability and performance.
Furthermore, employing slicing software, which converts the 3D model into printable layers and generates toolpaths for the 3D printer, facilitates visualizing the print process, identifying potential printing challenges, and optimizing parameters such as layer height, infill density, and support structures. This step is crucial in preemptively addressing printing issues and ensuring the manufacturability of the design.
Conducting feasibility tests by simulating the printing process and evaluating the model’s compatibility with the chosen 3D printer and materials is essential. This entails verifying dimensional accuracy, wall thickness, overhang angles, and intricate features to ascertain the printability of the design and preemptively rectify any red flags that may compromise the print’s success.
Physical prototyping through the creation of test prints, especially for intricate or functional designs, provides tangible insights into the model’s form, fit, and functionality. Iteratively refining the design based on the observations and feedback from test prints empowers designers to fine-tune geometries, optimize tolerances, and address any unforeseen challenges that surface during the physical prototyping phase.
Iterative adjustments based on testing feedback, simulation results, and prototyping observations are instrumental in refining the 3D model, culminating in a design that embodies structural soundness, manufacturability, and adherence to the envisioned specifications. Embracing a rigorous testing and refinement process not only enhances the quality of the final 3D print but also nurtures a mindset of continuous improvement and innovation in the realm of 3D printer design.
Read more: How To Make Money With A 3D Printer
Finalizing Your 3D Printer Design
As you approach the culmination of your 3D printer design journey, the phase of finalization encompasses a series of critical steps aimed at ensuring the readiness, precision, and optimization of the model for the impending transition from digital representation to physical manifestation.
Validating the design against the intended application and performance criteria is paramount. This involves revisiting the initial design objectives, evaluating the model’s adherence to functional requirements, and confirming its aesthetic appeal in alignment with the envisioned purpose. Verifying that the design encapsulates the desired form, features, and usability sets the stage for the subsequent stages of pre-processing and preparation for printing.
Pre-processing the 3D model involves meticulous examination and optimization of the digital representation to address potential printing challenges, enhance printability, and streamline the printing process. Tasks such as repairing mesh errors, hollowing out solid structures, and optimizing support structures contribute to preparing the model for seamless translation into a physical object.
Optimizing print orientation and positioning within the build volume of the 3D printer is a crucial consideration. Strategically orienting the model to minimize overhangs, reduce support material requirements, and ensure dimensional accuracy plays a pivotal role in enhancing print quality and minimizing post-processing efforts. Moreover, nesting multiple components or optimizing the layout for batch printing can maximize efficiency and material utilization.
Generating the final print file, typically in the form of an STL (Stereolithography) file, entails configuring print settings, such as layer height, infill density, print speed, and support structures, to align with the chosen 3D printer and material specifications. This step involves leveraging slicing software to fine-tune printing parameters and generate G-code, the machine-readable instructions that orchestrate the 3D printing process.
Validating the final print file through a comprehensive review of slicing previews, layer-by-layer visualization, and print simulations ensures that the model is primed for a successful and high-quality print. Addressing any anomalies, such as potential printing artifacts or structural weaknesses, at this stage fortifies the readiness of the design for the physical manifestation.
By meticulously navigating the finalization phase, designers culminate their 3D printer design endeavor with a meticulously honed and optimized model, poised for seamless translation into a physical object. Embracing a methodical and detail-oriented approach to finalizing the design not only ensures the success of the impending 3D print but also fosters a mindset of precision, innovation, and excellence in the realm of additive manufacturing and design.
Frequently Asked Questions about How To Make 3D Printer Designs
Was this page helpful?
At Storables.com, we guarantee accurate and reliable information. Our content, validated by Expert Board Contributors, is crafted following stringent Editorial Policies. We're committed to providing you with well-researched, expert-backed insights for all your informational needs.
0 thoughts on “How To Make 3D Printer Designs”