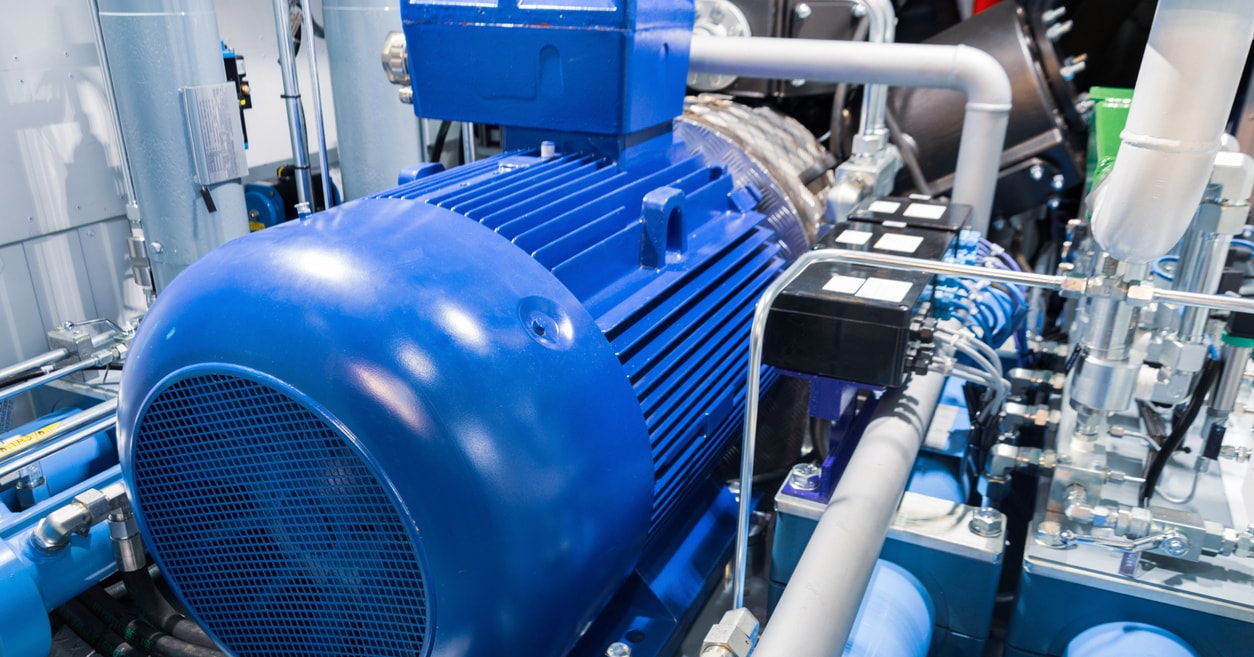
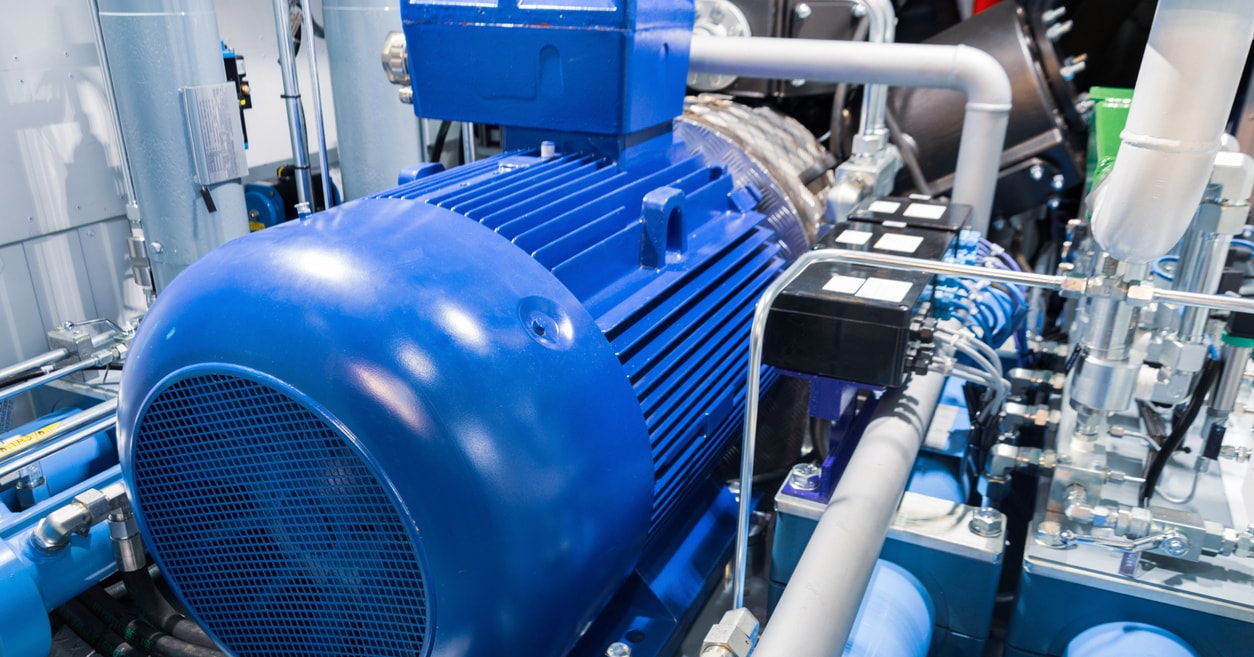
Articles
How To Calculate Electric Motor Torque
Modified: August 27, 2024
Learn how to calculate electric motor torque with our informative articles. Gain a better understanding of motor performance and efficiency.
(Many of the links in this article redirect to a specific reviewed product. Your purchase of these products through affiliate links helps to generate commission for Storables.com, at no extra cost. Learn more)
Introduction
Electric motors are a fundamental component of countless devices and industrial applications. Understanding and calculating electric motor torque is essential for ensuring optimal performance and efficiency. Torque, in simple terms, refers to the rotational force generated by an electric motor. It determines the motor’s ability to exert rotational force and is crucial for tasks like lifting heavy loads, driving machinery, and powering vehicles.
In this article, we will dive into the world of electric motor torque, exploring its significance and providing you with a step-by-step guide on how to calculate it. Whether you are an engineer, technician, or simply curious about the inner workings of electric motors, this article will equip you with the knowledge to better understand and harness the power of torque.
But first, let’s delve into the basics and understand what exactly electric motor torque is.
Key Takeaways:
- Understanding electric motor torque is crucial for optimizing performance, ensuring safety, and promoting energy efficiency in various applications. Factors like load requirements, motor design, and efficiency correction play key roles in accurate torque calculation.
- By following a step-by-step guide and considering factors like load requirements, safety margins, and efficiency correction, you can accurately calculate electric motor torque. Understanding the significance of torque and seeking professional advice can lead to efficient and reliable motor operation.
Read more: How To Calculate HP Of Electric Motor
Understanding Electric Motor Torque
Electric motor torque is the rotational force or moment of force exerted by an electric motor. It is what enables the motor to perform tasks such as lifting, rotating, or moving objects. The torque produced by an electric motor is directly proportional to its ability to generate rotational force and is typically measured in units of Newton meters (Nm).
To visualize electric motor torque, imagine a wrench tightening a bolt. The force applied to the wrench causes it to rotate, exerting torque on the bolt. Similarly, in an electric motor, torque is the force that causes the motor shaft to rotate.
The amount of torque an electric motor can generate is determined by several factors. These factors include the electrical power supplied to the motor, the motor’s design and construction, and the load or resistance the motor has to overcome. Generally, the larger and more powerful the motor, the greater its torque capacity.
It’s important to note that electric motor torque can be categorized into two types: starting torque and running torque. Starting torque is the torque required to initiate the rotation of the motor’s shaft from a stationary position. Running torque, on the other hand, is the torque required to maintain the continuous rotation of the motor’s shaft under load.
Now that we have a basic understanding of electric motor torque, let’s explore why it is important to calculate it accurately.
Importance of Calculating Electric Motor Torque
Calculating electric motor torque is crucial for several reasons, primarily related to ensuring the efficient and safe operation of the motor and the equipment it is powering. Let’s take a look at the importance of accurately calculating electric motor torque:
1. Motor Performance Optimization
By accurately calculating the required torque for a specific application, you can select an electric motor that meets the necessary torque requirements. This ensures that the motor operates within its optimal range, maximizing performance efficiency and minimizing energy waste. A properly sized motor will deliver the required torque without being oversized, saving both energy and costs.
2. Equipment Safety and Durability
Applying the correct torque to a load is essential for the safety and longevity of both the motor and the equipment it is driving. Insufficient torque may lead to motor stalling or failure, while excess torque can cause mechanical damage or excessive wear on the motor and connected components. By accurately calculating torque, you can prevent these issues, ensuring the longevity and reliability of the system.
Read also: 8 Best High Torque Electric Motor for 2024
3. Load Capacity Determination
Calculating electric motor torque enables you to determine the motor’s load capacity. By understanding the torque requirements of different loads, you can determine the maximum load an electric motor can handle without compromising its performance and safety. This information is crucial when selecting a motor for specific applications like lifting heavy loads, driving conveyor belts, or powering vehicles.
4. Energy Efficiency Considerations
Accurate torque calculation helps optimize energy consumption. An overly large motor operating at a fraction of its torque capacity will consume more energy than required, leading to unnecessary energy waste and increased operating costs. On the other hand, an electric motor operating at or near its maximum torque efficiency point will deliver optimal performance, minimizing energy consumption and environmental impact.
In summary, calculating electric motor torque accurately is vital for optimizing motor performance, ensuring equipment safety and durability, determining load capacity, and promoting energy-efficient operation. By understanding and calculating torque, you can make informed decisions when selecting and operating electric motors, leading to improved efficiency, cost savings, and overall productivity.
Factors Affecting Electric Motor Torque
Several factors influence the torque output of an electric motor. Understanding these factors is essential for accurately calculating and predicting the motor’s torque capacity. Let’s explore the key factors that affect electric motor torque:
1. Electrical Power Supply
The electrical power supplied to the motor plays a significant role in determining the torque it can generate. The voltage and current supplied to the motor affect the magnetic field strength and current flow within the motor’s windings. Higher voltage and current levels generally result in increased torque output, allowing the motor to exert greater rotational force.
Read more: How To Build A Electric Motor
2. Motor Design and Construction
The design and construction of the electric motor itself play a crucial role in determining its torque characteristics. Factors such as the size of the motor, the number and arrangement of its windings, the type of rotor construction, and the use of additional torque-boosting mechanisms (e.g., gearboxes) can all impact the motor’s torque output. Motors designed specifically for high torque applications will have different internal configurations compared to motors optimized for speed or efficiency.
3. Load and Resistance
The nature of the load or resistance that the electric motor has to overcome significantly affects its torque requirements. The torque required to lift a heavy load, for example, will be higher compared to rotating a small gear. Friction, inertia, and other external forces acting on the motor also impose resistance, which affects the torque needed to overcome these forces. Understanding the characteristics of the load and the resistance it imposes is crucial for accurately calculating the required motor torque.
4. Speed and Torque Relationship
The relationship between speed and torque is important when calculating electric motor torque. Electric motors typically exhibit an inverse relationship between speed and torque. In other words, higher torque output will result in lower speed, and vice versa. This relationship is governed by the motor’s torque-speed curve, which provides valuable insights into the motor’s performance capabilities at different operating points.
5. Efficiency and Losses
Efficiency and losses also impact the effective torque output of an electric motor. Motors are not 100% efficient, and losses occur in the form of heat, electrical resistance, and other factors. These losses reduce the available torque output of the motor. Understanding the motor’s efficiency and losses is essential for accurately estimating the effective torque that can be delivered to the load.
By considering these factors and their impact on electric motor torque, you can make more informed decisions and calculations when selecting and operating motors for various applications.
Read more: How To Clean An Electric Motor
Step-by-Step Guide: Calculating Electric Motor Torque
Calculating electric motor torque involves understanding the specific requirements of your application and making precise calculations based on the motor’s specifications and the load it needs to overcome. Follow this step-by-step guide to accurately calculate electric motor torque:
Step 1: Determine Load Requirements
Start by understanding the specific requirements of your application. Identify the load that the motor needs to overcome, such as lifting a weight or rotating a particular object. Consider factors such as the weight or resistance of the load and any external forces acting on it.
Step 2: Gather Motor Specifications
Collect the necessary specifications of the electric motor you will be using. This includes information such as the rated power (in watts or horsepower), rated speed (in RPM), and any additional information provided by the motor manufacturer. These specifications can typically be found on the motor nameplate or in the motor’s documentation.
Step 3: Calculate Speed-Torque Required
Based on the load requirements, determine the desired speed and torque for your application. Consider the relationship between speed and torque, as higher torque output will result in lower speed, and vice versa. Use this information to establish the torque-speed curve desired for your application.
Read more: How Efficient Is An Electric Motor
Step 4: Apply Efficiency Correction
Take into account the efficiency of the motor to determine the effective torque that can be delivered to the load. Multiply the desired torque by the motor’s efficiency to adjust for losses and calculate the corrected torque value.
Step 5: Incorporate Safety Factors
Consider any safety factors or margins that need to be applied to ensure safe and reliable operation. This can include factors such as a safety margin for unexpected variations in load or operating conditions.
Step 6: Calculate Torque
Finally, use the gathered information and formulas specific to your motor type and application to calculate the torque. Consult resources such as motor manufacturer documentation or industry references for specific formulas and calculations.
Step 7: Verify the Calculated Torque
Once you have calculated the torque, it is essential to verify its compatibility with the motor’s specifications. Ensure that the calculated torque does not exceed the maximum torque capability of the motor. If the calculated torque is higher than the motor’s capacity, you may need to consider selecting a more powerful or suitable motor for your application.
By following this step-by-step guide, you can accurately calculate electric motor torque for your specific application and ensure the motor’s efficient and reliable operation.
Read more: How To Cool An Electric Motor
Example Calculation
To solidify our understanding of calculating electric motor torque, let’s consider an example scenario:
Suppose we have a DC electric motor with the following specifications:
- Rated power: 1.5 kW
- Rated speed: 3000 RPM
- Efficiency: 90%
We want to use this motor to lift a weight of 500 kilograms. To calculate the torque required for this task, follow these steps:
Step 1: Determine Load Requirements
The load in this case is the weight of 500 kilograms that needs to be lifted.
Step 2: Gather Motor Specifications
We have the specifications of the motor mentioned above.
Step 3: Calculate Speed-Torque Required
Based on the desired speed and the load requirement, we determine that a torque speed of 1000 Nm is necessary for this application.
Read more: How Efficient Is An Electric Motor
Step 4: Apply Efficiency Correction
Multiply the desired torque by the motor’s efficiency to adjust for losses:
Corrected torque = Desired torque / Efficiency
Corrected torque = 1000 Nm / 0.90
Corrected torque = 1111.11 Nm
Step 5: Incorporate Safety Factors
In this example, let’s assume a safety factor of 20% is applied for unexpected load variations.
Safety-adjusted torque = Corrected torque * Safety factor
Safety-adjusted torque = 1111.11 Nm * 1.20
Safety-adjusted torque = 1333.33 Nm
Step 6: Calculate Torque
In this example, we have determined the final torque requirement to be 1333.33 Nm.
Step 7: Verify the Calculated Torque
Verify that the calculated torque does not exceed the motor’s maximum torque capacity specified by the manufacturer. If the torque requirement exceeds the motor’s capacity, you may need to select a different motor or consider other alternatives.
By following these steps and performing the necessary calculations, you can determine the appropriate torque for specific applications and select a motor that can meet the requirements effectively.
Read more: How To Oil An Electric Motor
Tips and Considerations
Calculating electric motor torque involves careful analysis and consideration of various factors. Here are some tips and considerations to keep in mind when calculating and working with electric motor torque:
1. Understand the Load Requirements
Thoroughly understand the specific requirements of your application, including the nature of the load and any external forces acting on it. This understanding will help you accurately determine the torque needed to overcome the load.
2. Consult Motor Specifications
Refer to the motor’s specifications provided by the manufacturer. These specifications typically include rated power, rated speed, and efficiency. Having this information at hand is crucial for accurately calculating torque and selecting an appropriate motor.
3. Consider Safety Factors
Incorporate safety factors to account for unexpected variations in load or operating conditions. Applying a safety margin helps ensure the motor operates within a safe range, preventing possible damages and failures.
Read more: How To Rewind Electric Motor
4. Use Efficiency Correction
Take into account the efficiency of the motor when calculating torque. Efficiency correction adjusts for losses and provides a more accurate estimation of the effective torque that can be delivered to the load.
5. Select the Right Motor
Ensure that the selected motor can meet the torque requirements of your application. Be cautious not to exceed the motor’s maximum torque capacity, as this can lead to motor damage and reduced performance.
6. Seek Professional Advice
If you are unsure about the calculations or have complex requirements, consider consulting with an experienced engineer or motor specialist. Their expertise can help ensure accurate torque calculations and optimal motor selection for your specific application.
7. Regular Maintenance and Monitoring
Regularly inspect and maintain the electric motor to ensure its continued performance and longevity. Monitor the motor’s torque output and other operating parameters to identify any potential issues early and take corrective actions promptly.
By keeping these tips and considerations in mind, you can effectively calculate, utilize, and maintain electric motor torque for optimal performance and efficiency in your applications.
Read more: How to Size An Electric Motor
Conclusion
Understanding and calculating electric motor torque is essential for ensuring optimal performance, efficiency, and safety in various applications. Torque, the rotational force generated by an electric motor, determines its ability to perform tasks such as lifting heavy loads, driving machinery, and powering vehicles.
In this article, we have explored the fundamentals of electric motor torque, its importance in application performance, and the factors that affect torque output. We have also provided a step-by-step guide for accurately calculating electric motor torque, along with an example calculation to demonstrate the process.
By accurately calculating torque, you can optimize motor performance, ensure equipment safety and durability, and determine load capacities. Considerations like the electrical power supply, motor design, load requirements, and efficiency correction play crucial roles in the calculation process.
Additionally, we have provided some valuable tips, such as understanding load requirements, consulting motor specifications, applying safety factors, and selecting the right motor for your application. Seeking professional advice and implementing regular maintenance and monitoring practices can further enhance the overall performance and lifespan of your electric motor.
In conclusion, by leveraging the knowledge and techniques shared in this article, you can confidently calculate and utilize electric motor torque to drive successful and efficient operations in a wide range of industries and applications.
Frequently Asked Questions about How To Calculate Electric Motor Torque
Was this page helpful?
At Storables.com, we guarantee accurate and reliable information. Our content, validated by Expert Board Contributors, is crafted following stringent Editorial Policies. We're committed to providing you with well-researched, expert-backed insights for all your informational needs.
0 thoughts on “How To Calculate Electric Motor Torque”