Home>Articles>How To Turn An Electric Motor Into A Generator
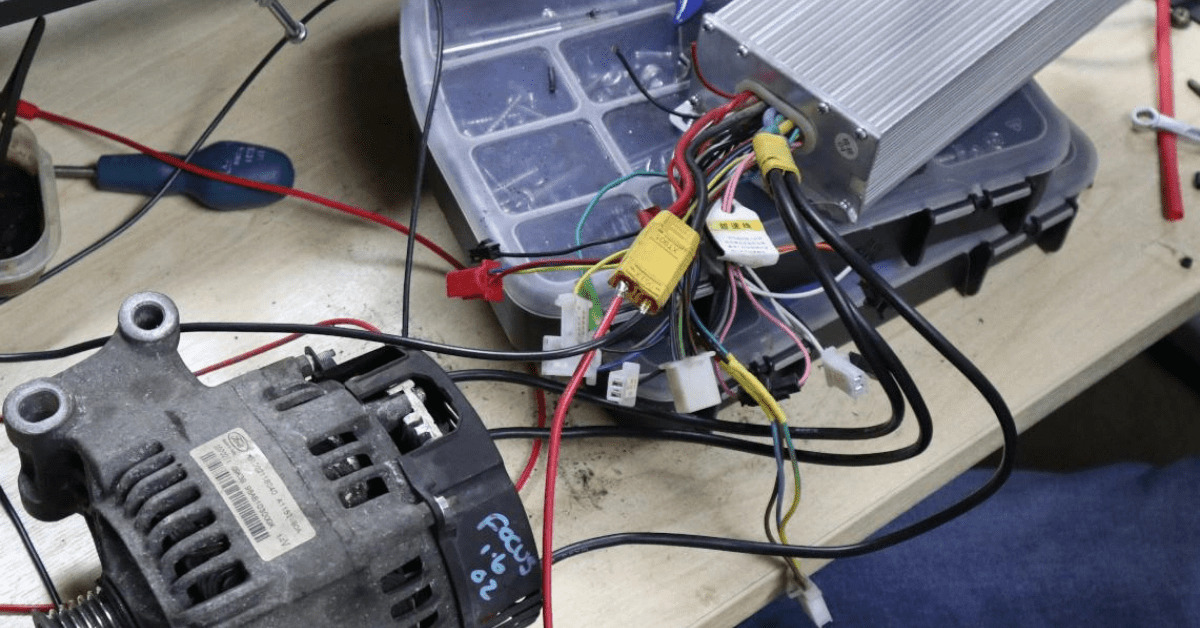
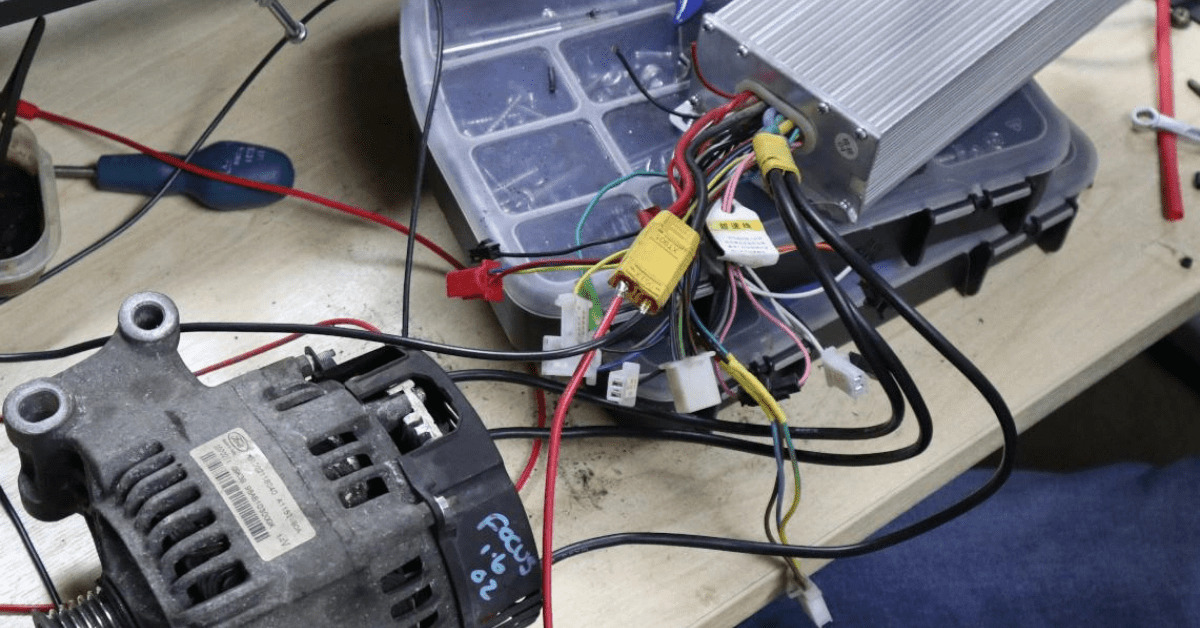
Articles
How To Turn An Electric Motor Into A Generator
Modified: February 22, 2024
Learn how to easily convert an electric motor into a generator with our informative articles. Discover step-by-step instructions and expert tips.
(Many of the links in this article redirect to a specific reviewed product. Your purchase of these products through affiliate links helps to generate commission for Storables.com, at no extra cost. Learn more)
Introduction
Electric motors and generators are two essential components of various industries and applications. While electric motors are primarily used to convert electrical energy into mechanical energy, generators perform the opposite function by converting mechanical energy into electrical energy.
However, did you know that it is possible to turn an electric motor into a generator? This process can be quite beneficial, allowing you to harness and utilize renewable energy sources or even keep the lights on during a power outage.
In this article, we will explore the fascinating world of electric motors and generators. We will delve into their functions, highlight the similarities between the two, and discover how to convert an electric motor into a generator. So, let’s dive in and unlock the secrets of this electrical transformation!
Key Takeaways:
- Converting an electric motor into a generator is a fascinating DIY project that allows you to harness renewable energy or create a backup power supply. However, it requires technical knowledge and expertise to ensure safety and optimal performance.
- Understanding the similarities and differences between electric motors and generators is crucial for successfully converting an electric motor into a functional generator. It’s a rewarding project that enables you to tap into renewable energy sources and explore sustainable energy solutions.
Read also: 15 Amazing Electric Motor Generator for 2024
Understanding Electric Motors
Before we delve into the process of converting an electric motor into a generator, let’s first understand what an electric motor is and how it works.
An electric motor is a device that converts electrical energy into mechanical energy. It relies on the principles of electromagnetism to operate. Inside an electric motor, there are coils of wire, referred to as windings, which are wrapped around a metal core known as the armature. When an electric current passes through the windings, it creates a magnetic field that interacts with the field produced by permanent magnets or electromagnets.
This interaction between the magnetic fields causes the armature to rotate. The rotation of the armature generates mechanical energy, which is then used to power various devices or machinery. Electric motors are widely used in a multitude of applications, ranging from home appliances and automobiles to industrial machinery and HVAC systems.
There are different types of electric motors available, including DC (direct current) motors and AC (alternating current) motors. DC motors operate on DC power and are commonly found in battery-operated devices or applications that require precise speed control. AC motors, on the other hand, run on AC power and are typically used in household appliances, industrial machinery, and compressors.
Electric motors are known for their efficiency, reliability, and versatility. They play a crucial role in our daily lives, powering everything from ceiling fans and pumps to electric vehicles and elevators.
Now that we have a basic understanding of electric motors, let’s move on to exploring the world of generators and their functionalities.
Understanding Generators
Generators, like electric motors, are essential devices that play a vital role in various applications. Unlike electric motors that convert electrical energy into mechanical energy, generators do the opposite by converting mechanical energy into electrical energy.
A generator operates on the principle of electromagnetic induction. It consists of a rotor, which is connected to a mechanical power source, and a stator, which contains the windings. When the rotor is driven by a mechanical force, such as a turbine or an engine, it produces a rotating magnetic field.
This rotating magnetic field induces a current in the windings of the stator, generating an electrical output. The output voltage and frequency produced by the generator depend on factors such as the speed of the rotor and the number of poles in the generator.
Generators are commonly used in various scenarios where electrical power is required but a reliable grid connection is not available. They serve as a backup power source during blackouts or in remote areas where electricity is inaccessible. Generators are also extensively used in industries, construction sites, and events to provide temporary power supply.
Similar to electric motors, there are different types of generators, including diesel generators, gasoline generators, and natural gas generators. The choice of generator depends on factors such as power requirements, fuel availability, and portability.
Generators are not just limited to emergency backup power. They are also utilized in renewable energy systems, such as wind turbines and hydroelectric power plants, where mechanical energy from natural sources is converted into electrical energy.
Now that we have explored the functionalities of both electric motors and generators, let’s take a closer look at some of the similarities between them.
Similarities Between Electric Motors and Generators
Electric motors and generators share several similarities due to their underlying principles and components. Understanding these similarities can help us better comprehend the process of converting an electric motor into a generator.
1. Magnetic Field: Both electric motors and generators rely on the interaction between magnetic fields to function. In an electric motor, the magnetic field produced by the windings interacts with the field created by permanent magnets or electromagnets, causing the armature to rotate. Similarly, in a generator, the rotating magnetic field induces a current in the windings of the stator, producing an electrical output.
2. Armature and Stator: Both electric motors and generators have an armature and a stator. The armature is the rotating component that generates the mechanical energy, while the stator is the stationary component that contains the windings. The interaction between the armature and the stator is crucial for the conversion of energy.
3. Windings: Electric motors and generators both utilize windings, which are coils of wire, to create the magnetic fields necessary for their operation. The windings are designed to carry the electrical current and generate the magnetic forces needed for the conversion of energy.
4. Electrical Connections: Both electric motors and generators require proper electrical connections to function. In an electric motor, the windings are connected to a power source, providing the necessary electricity for the conversion of electrical energy into mechanical energy. In a generator, the electrical load is connected to the output terminals to receive the converted electrical energy.
5. Energy Conversion: One of the most significant similarities between electric motors and generators is the ability to convert energy from one form to another. Electric motors transform electrical energy into mechanical energy, allowing the devices they power to perform various tasks. Generators, on the other hand, convert mechanical energy into electrical energy, providing a source of power in different applications.
Understanding the similarities between electric motors and generators lays the foundation for transforming an electric motor into a generator. In the next section, we will discuss the step-by-step process of converting an electric motor into a functional generator.
Converting an Electric Motor into a Generator
Converting an electric motor into a generator can be a rewarding project that allows you to harness renewable energy or provide backup power in emergency situations. While the process may vary depending on the type and model of the electric motor, the general steps remain the same. Here is a step-by-step guide:
- Step 1: Choosing the Right Electric Motor: Start by selecting a suitable electric motor for conversion. Look for motors that are heavy-duty and have a high horsepower rating. DC motors are often preferred for generator conversion projects due to their simplicity.
- Step 2: Removing the Power Supply: Disconnect the power supply to the electric motor. This typically involves disconnecting the motor from any electrical wires or cables. Make sure to follow proper safety precautions and consult the motor’s user manual for guidance.
- Step 3: Adding a Shaft and Pulley System: Install a shaft and pulley system to the electric motor. This will allow you to connect the motor to an external power source, such as a turbine or an engine, which will provide the mechanical force needed to generate electricity. Ensure that the shaft and pulley are securely attached to the motor.
- Step 4: Connecting Wires and Terminals: Connect the output terminals of the generator, usually located on the stator, to a power distribution panel or directly to the load. This will allow you to utilize the generated electricity to power your devices or systems. Use proper wiring techniques and ensure that all connections are secure and well-insulated.
- Step 5: Testing the Generator: Before putting your converted generator into full operation, conduct a thorough testing phase. Start by manually turning the shaft of the motor to simulate the mechanical force. Measure the voltage and frequency of the generated electricity using a multimeter or a power analyzer. Make any necessary adjustments or modifications to ensure optimal performance.
It is important to note that converting an electric motor into a generator may require advanced electrical knowledge and skills. If you are unsure, it is recommended to seek assistance from a professional or experienced individual to ensure safety and efficiency.
By following these steps, you can transform an electric motor into a functional generator, giving you the ability to harness renewable energy or provide backup power when needed. However, always remember to prioritize safety and adhere to electrical standards and guidelines throughout the conversion process.
Step 1: Choosing the Right Electric Motor
The first step in converting an electric motor into a generator is selecting the right motor for the project. Choosing a suitable electric motor is crucial as it will impact the efficiency and performance of the generator. Here are some factors to consider when selecting an electric motor for conversion:
- Type of Motor: There are different types of electric motors available, including DC motors and AC motors. DC motors are often preferred for generator conversion projects due to their simplicity and ease of control. However, AC motors can also be used, depending on the specific requirements of your project.
- Power Rating: Consider the power rating of the motor, typically measured in horsepower (HP). The higher the power rating, the more electricity the generator will be able to produce. Choose a motor with a power rating suitable for your intended application to ensure it meets your power needs.
- Motor Efficiency: Look for a motor with high efficiency as this will contribute to the overall efficiency of the generator. Higher efficiency motors will convert more mechanical energy into electricity, resulting in better energy conversion and reduced power losses.
- Motor Size and Weight: Consider the physical size and weight of the motor as this will impact the portability and installation of the generator. Choose a motor that is compact and lightweight, making it easier to handle and maneuver.
- Motor Condition and Age: Inspect the condition of the motor before purchasing or using it for conversion. Look for signs of wear and tear, damage, or any issues that may affect its performance. Additionally, consider the age of the motor, as older motors might have outdated technology and may not be as efficient as newer ones.
It is also advisable to consult with experts or individuals experienced in generator conversion projects. They can provide valuable insights and guidance in selecting the right motor for your specific needs.
Once you have chosen the appropriate electric motor, you can proceed with the next steps of the conversion process. Remember, each motor may have its own unique specifications and requirements, so it is essential to carefully follow the manufacturer’s instructions and safety guidelines throughout the conversion process.
In the next step, we will discuss how to remove the power supply from the electric motor, laying the groundwork for the conversion process.
To turn an electric motor into a generator, simply rotate the shaft of the motor by an external force, such as a hand crank or a wind turbine. This will induce a current in the motor’s coils, effectively turning it into a generator.
Step 2: Removing the Power Supply
After selecting the right electric motor for your generator conversion project, the next step is to remove the power supply from the motor. This step is crucial to ensure the motor operates as a generator rather than an electrical motor. Here’s how you can remove the power supply:
- Disconnect the Motor: Start by disconnecting the electric motor from any power sources, such as electrical wires or cables. This may involve turning off the power supply or unplugging the motor, depending on the specific setup. Always follow proper safety procedures and guidelines to avoid electrical hazards during this process.
- Remove the Motor Cover: If the motor has a cover or casing, remove it to gain access to the internal components. This may require using appropriate tools such as screwdrivers or wrenches. Take caution to avoid damaging any parts of the motor during the removal process.
- Identify Power Supply Connections: Once the motor is exposed, identify the power supply connections. This typically includes wires or cables that are connected to the motor’s terminals or connectors. Different motors may have varying configurations, so consult the motor’s user manual or documentation for specific instructions.
- Disconnect Power Supply Wires: Carefully disconnect the power supply wires from the motor’s terminals. This may involve loosening screws or plugs that secure the wires in place. Take note of the wire colors and terminal markings for reconnection later if needed.
- Secure Power Supply Wires: After removing the power supply, ensure the wires are safely secured and isolated to prevent accidental contact or short circuits. You can use electrical tape or wire nuts to cover the exposed ends of the wires.
It is important to emphasize that removing the power supply from the electric motor should be done with caution and only by individuals with proper knowledge and experience. If you are unsure or uncomfortable with this step, it is advisable to seek guidance from a professional electrician or consult with experts in generator conversions.
Once the power supply is disconnected, you can proceed to the next step of the conversion process, which involves adding a shaft and pulley system to the electric motor.
Step 3: Adding a Shaft and Pulley System
Adding a shaft and pulley system is an essential step in converting an electric motor into a functional generator. This system allows you to connect the motor to an external power source, such as a turbine or an engine, which will provide the mechanical force required to generate electricity. Here’s how you can add a shaft and pulley system to your electric motor:
- Assess the Motor: Begin by assessing the motor to determine the appropriate location for adding the shaft and pulley. Identify a suitable spot on the motor where the shaft can be securely attached without interfering with other components or impeding the motor’s operation.
- Choose the Shaft: Select a shaft that is compatible with your motor and the external power source you plan to connect to. The shaft should be able to withstand the rotational forces and transmit the mechanical energy effectively. Consider factors such as diameter, length, and material when choosing the shaft.
- Attach the Shaft: Firmly attach the selected shaft to the motor using appropriate hardware, such as screws or fasteners. Ensure that the shaft is aligned with the motor’s axis of rotation, allowing for smooth and efficient operation.
- Select a Pulley: Choose a pulley that matches the specifications of both the shaft and the external power source. The pulley should be compatible in terms of diameter, belt size, and design. It should provide a secure and efficient connection to transfer mechanical energy.
- Mount the Pulley: Mount the pulley onto the shaft, ensuring that it is securely fastened. Pay attention to proper alignment to minimize vibrations and optimize energy transfer. Double-check the tightness of bolts or set screws to ensure they are secure.
- Check for Smooth Operation: Rotate the shaft by hand to verify that the pulley moves smoothly. Check for any unusual noises or obstructions. If any issues are detected, make adjustments as necessary to ensure proper operation.
Adding a shaft and pulley system to your electric motor is a critical step that enables the conversion of mechanical energy into electricity. It is important to ensure that all connections are secure and properly aligned to prevent any potential hazards or inefficiencies.
Once the shaft and pulley system are in place, you can move on to the next step, which involves connecting the wires and terminals to prepare the motor for generator functionality.
Step 4: Connecting Wires and Terminals
After adding the shaft and pulley system to your electric motor, the next step in converting it into a generator is connecting the wires and terminals. This step involves establishing the necessary electrical connections to enable the generation and transfer of electricity. Here’s how you can connect the wires and terminals:
- Prepare the Wires: Ensure that the wires you will be using are in good condition and free from any damage or fraying. Strip off a small portion of the wire insulation at the ends to expose the conductive copper wire.
- Identify the Output Terminals: Locate the output terminals on the motor, usually located on the stator. These terminals will serve as the connection points for the generated electricity. Refer to the motor’s documentation or user manual to identify the specific terminals designated for output.
- Connect the Negatives (Ground): Connect the negative (ground) wire from your load or power distribution panel to the corresponding negative terminal on the motor. Ensure a solid and secure connection using appropriate techniques such as crimping, soldering, or using terminal blocks.
- Connect the Positives: Connect the positive wires from your load or power distribution panel to the positive terminals on the motor. Again, ensure a secure connection to allow for efficient transfer of electricity.
- Double-Check Connections: Before finalizing the connections, double-check all the wire connections to ensure they are correctly attached to the appropriate terminals. Avoid any loose connections or exposed wires that may cause short circuits or other electrical issues.
- Insulate and Secure Connections: Once all the connections are in place, use electrical tape, heat shrink tubing, or wire nuts to insulate and protect the exposed wire connections. Ensure that the connections are safely covered to prevent accidental contact or damage.
It is crucial to ensure that all electrical connections are made properly and securely. Inaccurate or loose connections can lead to inefficient energy transfer, overheating, or even safety hazards. If you are unsure about the wiring process, it is recommended to consult with an expert or seek assistance from a professional electrician.
With the wires and terminals properly connected, you are now ready to move on to the final step, which involves testing the generator to ensure its functionality and performance.
Step 5: Testing the Generator
After completing the previous steps to convert your electric motor into a generator, the final step is to conduct a thorough testing phase. This will help ensure that your generator is functioning properly and capable of generating the desired amount of electricity. Here’s how you can test your generator:
- Mechanical Inspection: Start by visually inspecting the generator for any loose connections, damaged components, or signs of abnormal wear. Check that all parts, including the shaft, pulley, and terminals, are securely in place.
- Rotational Testing: Manually rotate the generator’s shaft to simulate the mechanical force that would be supplied by an external power source. Observe the rotation and listen for any unusual noises or vibrations. The rotation should be smooth and consistent.
- Electrical Testing: Use a multimeter or a power analyzer to measure the voltage and frequency of the electricity generated by the generator. Connect the testing device to the output terminals of the generator and record the readings. Ensure that the voltage and frequency are within the range required for your intended application.
- Load Testing: Gradually introduce a load to the generator to see how it performs under various operating conditions. Start with a smaller load, such as a lightbulb or a small appliance, and gradually increase the load. Monitor the generator’s output voltage and frequency to ensure they remain stable within acceptable limits.
- Efficiency Assessment: Evaluate the efficiency of the generator by comparing the mechanical energy input (rotation of the shaft) with the electrical energy output (measured voltage and current). Calculate the efficiency using the formula: Efficiency = (Electrical Output Power / Mechanical Input Power) x 100%. Higher efficiency indicates better energy conversion.
- Safety Considerations: During testing, prioritize safety by following electrical safety guidelines. Avoid touching exposed wires, ensure proper grounding, and use protective gloves and eyewear. If you encounter any issues or concerns, stop the testing immediately and seek professional assistance.
By thoroughly testing your generator, you can identify any potential issues or areas for improvement. If necessary, make adjustments to the generator’s components or connections to optimize its performance and efficiency.
Remember that converting an electric motor into a generator requires technical knowledge and skills. If you are not familiar with electrical systems, it is advisable to seek assistance from a professional electrician or someone experienced in generator conversions.
Once you are satisfied with the testing results, congratulations! You have successfully converted your electric motor into a functional generator, ready to provide electrical power for your intended applications.
Conclusion
Converting an electric motor into a generator can be a rewarding project that allows you to harness renewable energy or provide backup power in emergency situations. Throughout this article, we explored the process of converting an electric motor into a generator, step by step.
We began by understanding electric motors and generators, highlighting their functions and the similarities between them. Electric motors efficiently convert electrical energy into mechanical energy, while generators do the reverse, transforming mechanical energy into electrical energy.
We then discussed the important steps in converting an electric motor into a generator. Starting with choosing the right motor, we moved on to removing the power supply, adding a shaft and pulley system, connecting wires and terminals, and finally, testing the generator for functionality and performance.
It is crucial to emphasize that generator conversion projects require technical knowledge and expertise. If you are not confident in your abilities or lack experience with electrical systems, it is recommended to seek assistance from professionals or experts in the field to ensure safety and optimal performance.
By converting an electric motor into a generator, you can tap into renewable energy sources, create a backup power supply, or even explore DIY projects and experiments. Remember to prioritize safety, follow manufacturer guidelines, and adhere to electrical standards and regulations throughout the process.
Now that you have a good understanding of converting an electric motor into a generator, you can embark on your own generator conversion project with confidence. Enjoy the process of harnessing and utilizing electrical energy in a unique and sustainable way!
Frequently Asked Questions about How To Turn An Electric Motor Into A Generator
Was this page helpful?
At Storables.com, we guarantee accurate and reliable information. Our content, validated by Expert Board Contributors, is crafted following stringent Editorial Policies. We're committed to providing you with well-researched, expert-backed insights for all your informational needs.
0 thoughts on “How To Turn An Electric Motor Into A Generator”