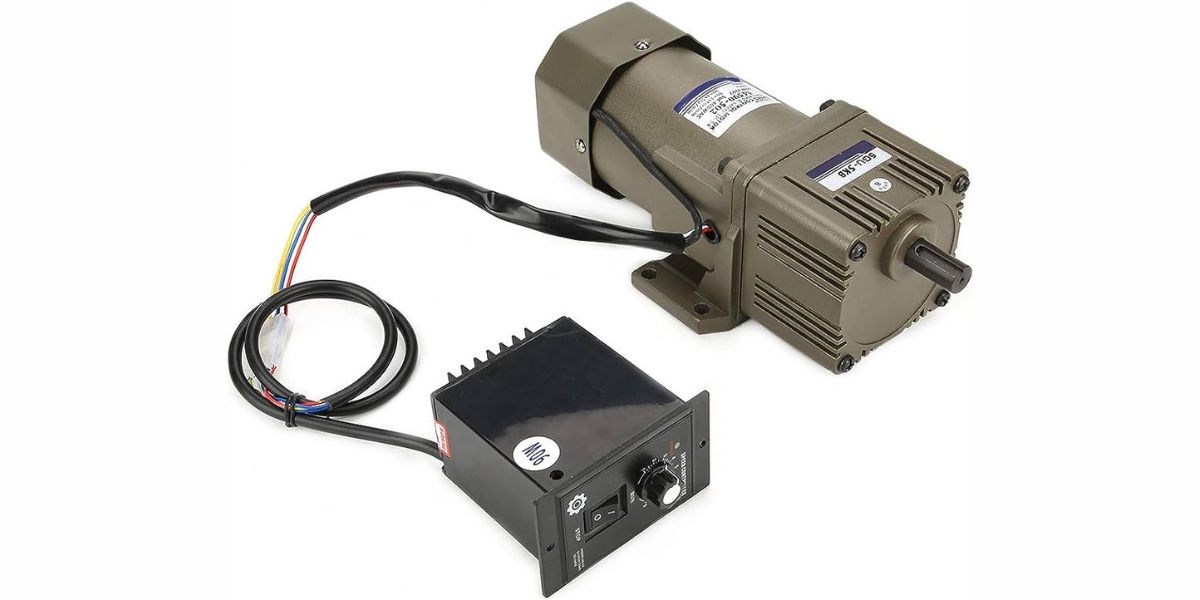
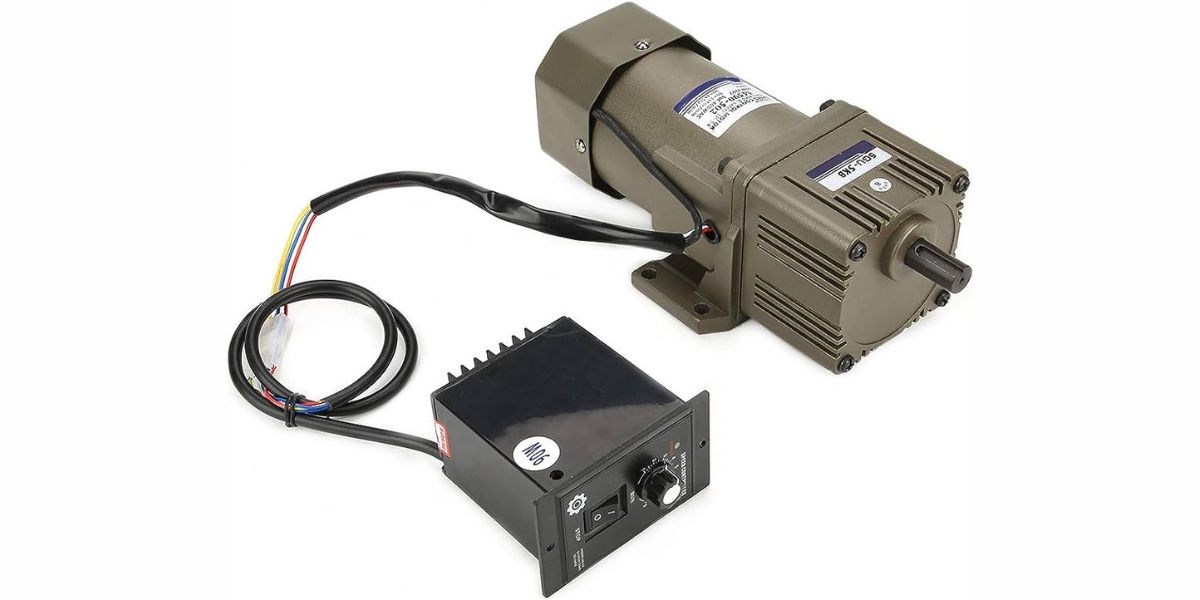
Articles
How To Control The Speed Of An Electric Motor
Modified: August 27, 2024
Discover effective techniques and methods to control the speed of an electric motor in this informative article. Learn how to optimize performance and achieve desired results.
(Many of the links in this article redirect to a specific reviewed product. Your purchase of these products through affiliate links helps to generate commission for Storables.com, at no extra cost. Learn more)
Introduction
Electric motors are a vital component in various industries and applications. They are responsible for powering machinery and equipment, enabling efficient operations. One important aspect of electric motors is their speed control. The ability to control the speed of an electric motor allows for flexibility and optimization in different scenarios.
In this article, we will explore the fundamentals of electric motor speed control and the various methods used to achieve it. Understanding these concepts will provide valuable insights into how motors operate and how to harness their potential.
Before delving into motor speed control, let’s briefly discuss the basics of electric motors. Electric motors are devices that convert electrical energy into mechanical energy, providing rotational motion. They consist of two main components: the stator, which houses the stationary windings, and the rotor, which contains the rotating windings.
The speed at which an electric motor operates is determined by the frequency of the electrical power supplied to it. Typically, electric motors are designed to operate at a specific speed dependent on the application requirements. However, there are instances where variable speed control is necessary to optimize performance.
Controlling the speed of an electric motor offers numerous advantages. It allows for precise control, energy efficiency, and improved overall system performance. By adjusting the motor speed, we can match it to the load requirements, resulting in reduced energy consumption and increased equipment longevity.
There are several factors that influence motor speed. These include the applied load, the motor’s design parameters, and the power supply frequency. Depending on the application, different methods can be employed to maintain and control the desired speed.
In the following sections, we will explore the most commonly used methods for controlling electric motor speed. These methods include direct voltage control, pulse width modulation (PWM), and variable frequency drives (VFD). Each method has its own advantages and suitability depending on the specific application.
By understanding and implementing appropriate speed control strategies, we can maximize the efficiency and performance of electric motors, ensuring optimal operation in a wide range of industrial and commercial applications.
Key Takeaways:
- Efficient motor speed control methods such as PWM and VFDs offer precise regulation, energy savings, and improved performance, enhancing the potential of electric motors in various industrial and commercial applications.
- Understanding factors influencing motor speed and implementing appropriate control strategies are crucial for optimizing motor performance, achieving energy efficiency, and driving productivity in diverse settings.
Understanding Electric Motors
Before diving into the details of motor speed control, it is essential to have a basic understanding of electric motors and their key components.
Electric motors are devices that convert electrical energy into mechanical energy, generating rotational motion. They are widely used in various industries, including manufacturing, automotive, HVAC, and robotics. Electric motors consist of two primary components: the stator and the rotor.
The stator is the stationary part of the motor and is responsible for producing a rotating magnetic field. It is composed of multiple coils or windings made of insulated copper wire. These windings are arranged in specific patterns to create the desired magnetic field when energized by an electrical power source.
The rotor, on the other hand, is the rotating part of the motor. It is typically made of a series of laminated iron cores, with conducting bars or coils embedded in them. The rotor is located inside the stator and is free to rotate when subjected to the magnetic field produced by the stator windings.
When an electric current flows through the stator windings, it generates a rotating magnetic field. This field induces currents in the rotor conductors, resulting in a torque that causes the rotor to rotate. The speed at which the rotor rotates is determined by the frequency of the current supplied to the motor.
Electric motors are designed to operate at specific speeds depending on the intended application. In some cases, fixed-speed motors are sufficient, as the load requirements do not vary. However, there are numerous applications where the ability to control the motor speed is crucial.
Motor speed control offers several advantages. It enables precise control over the motor’s output, allowing it to adapt to varying load conditions. By adjusting the motor speed, we can match it to the required torque, ensuring optimal performance and energy efficiency.
There are various factors that can affect the speed of an electric motor. These include the mechanical load applied to the motor shaft, the design characteristics of the motor, and the frequency of the power supply. Understanding these factors is crucial in implementing effective speed control strategies.
In the following sections, we will explore the different methods used to control motor speed, ranging from basic voltage control to more advanced techniques like pulse width modulation (PWM) and variable frequency drives (VFD). Each method has its own advantages and considerations, and the choice depends on the specific application and requirements.
By gaining a deeper understanding of electric motors and the factors that influence their speed, we can make informed decisions about the appropriate speed control method to implement, leading to improved efficiency and performance in various industrial and commercial applications.
Factors Affecting Motor Speed
Understanding the factors that influence motor speed is crucial in effectively controlling and optimizing the performance of electric motors. Several key factors can impact motor speed, and being aware of them allows for precise control and efficient operation.
1. Load: The applied load on the motor shaft significantly affects its speed. As the load increases, the motor may slow down as it needs to exert more torque to overcome the resistance. Conversely, when the load decreases, the motor speed may increase. It is important to consider the variation in load conditions when implementing speed control methods.
2. Motor Design: The design and characteristics of the motor itself play a significant role in determining its speed. The physical properties such as the number of poles, winding configuration, and magnetic flux density influence the motor’s speed-torque characteristics. Motors can have different speed ranges depending on their design, and understanding these parameters is essential for efficient control.
3. Power Supply Frequency: In alternating current (AC) motors, the power supply frequency directly affects the motor speed. Most AC motors are designed to operate at a specific frequency, such as 50 or 60 Hz. Altering the frequency can result in a change in motor speed. However, it’s important to note that the speed-torque relationship of AC motors may not be linear, and special control methods are required to achieve precise speed control.
4. Voltage: Voltage plays a critical role in determining motor speed, especially in direct current (DC) motors. The speed of a DC motor is directly proportional to the voltage applied to it. By varying the voltage, the motor speed can be adjusted accordingly. However, it is important to consider the motor’s limitations and the maximum voltage it can handle.
5. Control Method: The control method used to regulate motor speed also affects its performance. Different control methods, such as direct voltage control, pulse width modulation (PWM), and variable frequency drives (VFD), offer varying degrees of precision and efficiency. The choice of control method depends on the specific application requirements and desired outcomes.
6. Environmental Factors: Environmental conditions, such as temperature and humidity, can impact motor performance and speed. Extreme temperatures or high humidity levels can affect the motor’s efficiency and lifespan. It’s important to consider the environmental factors and take appropriate measures to ensure optimal operation and speed control.
By considering these factors and their impact on motor speed, we can implement effective control strategies to optimize motor performance. Whether it’s adjusting the load conditions, selecting the appropriate control method, or ensuring suitable environmental conditions, a comprehensive understanding of these factors is crucial for successful motor speed control.
Methods to Control Motor Speed
Controlling the speed of an electric motor is essential for optimizing its performance and adapting to varying load requirements. Several methods can be employed to achieve motor speed control, each with its own advantages and considerations. Let’s explore some of the commonly used methods:
1. Direct Voltage Control: In DC motors, speed control can be achieved by varying the input voltage. By adjusting the voltage supplied to the motor, the speed can be increased or decreased. This method is simple and cost-effective, but it may not provide precise speed control and can generate heat in the motor due to increased power dissipation.
2. Pulse Width Modulation (PWM): PWM is a widely used technique for speed control in both DC and AC motors. It involves rapidly switching the power supply on and off, with the ratio of on time to off time controlling the effective voltage applied to the motor. By varying the duty cycle of the PWM signal, the average voltage and thus the motor speed can be regulated. PWM offers precise control and reduces power dissipation, making it an efficient method for motor speed control.
3. Variable Frequency Drives (VFD): VFDs are commonly used for speed control in AC induction motors. They allow for precise control over motor speed by varying the frequency of the power supply. VFDs convert the incoming AC power into DC and then generate a variable-frequency AC output to the motor. This method provides flexible and efficient speed control, enabling motor operation across a wide range of speeds.
4. Electronic Commutation: Electronic commutation is used in brushless DC (BLDC) motors to control speed. BLDC motors rely on electronic circuitry to switch the current in the motor windings, eliminating the need for mechanical brushes and commutators. By controlling the timing and sequence of current switching, the motor speed and direction can be adjusted accurately.
5. Gearboxes: In some cases, mechanical gearboxes are used to control motor speed. Gearboxes consist of a series of gears that transmit power and torque from the motor to the driven load. By varying the gear ratio, the motor speed can be adjusted accordingly. Gearboxes provide precise control but may introduce mechanical losses and require additional space and maintenance.
6. Motor Rewinding: In certain situations, motor speed control can be achieved by rewinding the motor windings to change the number of poles. This method allows for a different motor speed without changing the power supply frequency or voltage. However, motor rewinding is a complex and specialized process that may not be suitable for all motors or applications.
When selecting a speed control method, it is crucial to consider factors such as cost, precision, efficiency, and compatibility with the motor type and application requirements. Choosing the right method ensures optimal motor performance and energy efficiency, leading to improved productivity and cost savings in various industrial and commercial settings.
Direct Voltage Control
Direct voltage control is a simple and commonly used method for controlling the speed of DC motors. It involves varying the input voltage to the motor, thereby adjusting its speed. By increasing or decreasing the voltage supplied to the motor, the speed can be regulated accordingly.
In direct voltage control, a power supply with variable voltage output is used. This can be achieved through a potentiometer or a variable resistor connected to the power supply. By adjusting the position of the potentiometer or altering the resistance value of the variable resistor, the voltage supplied to the motor can be changed.
The principle behind direct voltage control is that the speed of a DC motor is directly proportional to the voltage applied to it. As the voltage increases, the motor speed increases, and as the voltage decreases, the speed decreases. This allows for flexible and easy control of motor speed to match specific application requirements.
Direct voltage control is especially effective in applications where precise speed control is not of utmost importance. It is commonly used in simple DC motor systems, such as in small appliances, fans, toys, and certain industrial applications where a constant speed is sufficient.
However, it is important to note that there are limitations and considerations when using direct voltage control. Firstly, as the voltage is increased, the motor draws more current, which can lead to increased power dissipation and heat generation in the motor. This may require additional cooling measures to prevent overheating.
Secondly, direct voltage control may not provide absolute precision in speed control. Variation in load conditions or changes in motor parameters can cause slight deviations in speed, which may not be desired in certain applications that require high precision.
Moreover, direct voltage control is more suitable for low-power DC motors. For larger motors or applications that require precise and efficient speed control, other methods like pulse width modulation (PWM) or variable frequency drives (VFD) are preferred.
In summary, direct voltage control is a straightforward and cost-effective method for controlling the speed of DC motors. It offers simplicity and flexibility but may have limitations in terms of precision and efficiency. It is commonly employed in applications where basic speed control is sufficient, but for more advanced requirements, alternative methods should be considered.
To control the speed of an electric motor, use a variable frequency drive (VFD) to adjust the frequency and voltage supplied to the motor, allowing for precise speed control.
Read more: How To Reduce The Speed Of An Electric Motor
Pulse Width Modulation (PWM)
Pulse Width Modulation (PWM) is a widely used technique for controlling the speed of both DC and AC motors. It offers precise and efficient control over motor speed by adjusting the average voltage applied to the motor.
The PWM method involves rapidly switching the power supply on and off at a fixed frequency. The duration or width of the “on” time in each cycle is varied to control the average voltage supplied to the motor. This is accomplished through a Pulse Width Modulator circuit, which generates a PWM signal with a controllable duty cycle.
The duty cycle represents the percentage of time the power supply is “on” compared to the total cycle time. A higher duty cycle corresponds to a longer “on” time and a higher average voltage applied to the motor, resulting in increased speed. Conversely, a lower duty cycle corresponds to a shorter “on” time and a lower average voltage, leading to decreased speed.
The main advantage of PWM control is that it regulates the motor speed with high precision and efficiency. By rapidly switching the power supply, PWM minimizes the power dissipation and heat generation in the motor. This makes it a more energy-efficient method compared to other speed control techniques.
PWM is commonly used in various applications, including DC motor speed control, LED dimming, and audio amplification. It offers a smooth and continuous range of speed control, allowing for fine adjustments to match specific load requirements.
When implementing PWM control for DC motor speed, a microcontroller or dedicated PWM controller is often used. The control algorithm calculates the desired duty cycle based on the user input or feedback from sensors, and the PWM signal is generated accordingly. The pulse frequency is typically in the range of several kilohertz to tens of kilohertz, depending on the motor and application requirements.
For AC motors, PWM is used in combination with Variable Frequency Drives (VFDs) to control both voltage and frequency. VFDs convert the incoming AC power into DC and then generate a variable-frequency AC output. PWM control is applied to modulate the AC output voltage, allowing for precise control over the motor speed.
Overall, Pulse Width Modulation (PWM) is a versatile and efficient method for controlling motor speed. Its ability to provide precise control over the average voltage applied to the motor makes it valuable in a wide range of applications. By choosing the appropriate duty cycle and pulse frequency, PWM enables smooth and accurate speed control, improving the performance and energy efficiency of electric motors.
Variable Frequency Drives (VFD)
Variable Frequency Drives (VFDs) are advanced electronic devices used for controlling the speed of AC induction motors. They provide precise and efficient speed control by varying the frequency and voltage of the power supply that drives the motor.
VFDs have become increasingly popular in industrial and commercial applications where accurate speed control is essential for optimal performance. They offer numerous benefits, including energy efficiency, improved motor protection, and reduced wear and tear on mechanical components.
The operation of a VFD involves converting the incoming AC power from the mains supply into DC power. This is accomplished using a rectification process, which converts the AC to DC by using diodes or thyristors. The rectified DC power is then converted back into variable-frequency AC through an inverter circuit.
The inverter circuit in a VFD utilizes pulse width modulation (PWM) to precisely control the frequency and voltage of the output AC power. By adjusting the frequency and voltage, the motor speed can be varied to meet the specific requirements of the application. The use of PWM enables smooth and precise control without generating excessive heat or power losses.
One of the main advantages of VFDs is their ability to provide a wide range of speed control. By adjusting the frequency of the output AC power, VFDs can drive motors at varying speeds, allowing for optimized operation according to load requirements. This results in energy savings as the motor only operates at the required speed, reducing unnecessary power consumption.
Additionally, VFDs offer precise control over motor acceleration and deceleration rates, which helps to mitigate mechanical stresses and extend the lifespan of the motor. They also allow for soft starting and stopping of the motor, reducing wear on mechanical components and preventing sudden torque surges that could damage the motor or connected equipment.
VFDs offer various control modes, including open-loop and closed-loop control. In open-loop control, the VFD adjusts the motor speed based on the set frequency, without feedback from sensors. In closed-loop control, the VFD continuously monitors the actual motor speed using feedback from sensors, allowing for more accurate speed control and better performance in dynamic load conditions.
It is important to note that implementing VFDs requires proper installation, setup, and programming to ensure optimal performance and protection for the motor and connected equipment. Additionally, VFDs generate harmonics that may affect other electrical components in the system, requiring appropriate filtering and mitigation measures.
In summary, Variable Frequency Drives (VFDs) are advanced electronic devices that provide precise and efficient speed control for AC induction motors. By adjusting the frequency and voltage of the power supply, VFDs enable optimized motor operation, resulting in energy savings, improved motor protection, and extended equipment lifespan. When properly implemented, VFDs offer a powerful tool for achieving precise and reliable motor speed control in a wide range of industrial and commercial applications.
Control Strategies for Motor Speed
Controlling the speed of electric motors requires implementing effective control strategies that take into account the specific application requirements and motor characteristics. These strategies ensure precise speed control, optimal performance, and energy efficiency. Let’s explore some commonly used control strategies:
1. Open-Loop Control: Open-loop control is the simplest form of motor speed control. In this strategy, the motor speed is set based on the desired frequency or voltage input without the use of feedback from sensors. This method is suitable for applications where speed variations are minimal or where cost is a primary consideration. However, open-loop control may not be suitable for applications that require high accuracy or adaptability to varying load conditions.
2. Closed-Loop Control: Closed-loop control involves using feedback from sensors to continuously monitor and adjust the motor speed. Speed feedback can be obtained from encoders, tachometers, or other speed sensing devices. The actual motor speed is compared to the desired speed, and adjustments are made to the control signal accordingly. Closed-loop control offers higher accuracy and adaptability, making it suitable for applications that require precise speed control or operation in changing load conditions.
3. Proportional-Integral-Derivative (PID) Control: PID control is a widely used control strategy that combines proportional, integral, and derivative actions to regulate motor speed. The proportional action adjusts the control signal based on the difference between the desired and actual speeds. The integral action integrates the error over time, eliminating steady-state error. The derivative action provides a damping effect, reducing overshoot and improving stability. PID control is highly versatile, providing effective speed regulation and stability in a variety of applications.
4. Adaptive Control: Adaptive control strategies continuously monitor the motor’s operating conditions and adjust the control parameters dynamically. These strategies adapt to changes in load conditions or motor characteristics and optimize the control algorithm accordingly. Adaptive control is particularly useful in situations where the motor is subjected to varying or uncertain conditions, allowing for optimal motor performance and energy efficiency.
5. Fuzzy Logic Control: Fuzzy Logic Control (FLC) is a control strategy that utilizes fuzzy logic to handle imprecise or uncertain input conditions. FLC incorporates linguistic variables and rules to make control decisions based on human-like reasoning. Fuzzy logic can be effective in motor speed control as it can handle non-linear relationships and variations in load conditions. FLC allows for flexible and adaptive control, making it suitable for applications where precise control is required.
6. Optimal Control: Optimal control strategies aim to minimize a specified cost function or maximize a performance criterion. These strategies use mathematical optimization techniques to determine the optimal control actions based on the system’s dynamics and constraints. Optimal control algorithms, such as Model Predictive Control (MPC) or Linear Quadratic Regulator (LQR), are commonly used for achieving optimal motor speed control in complex systems with multiple objectives.
Choosing the appropriate control strategy depends on the specific application requirements, available resources, and desired performance criteria. It is essential to evaluate the system dynamics, load conditions, and expected variations to select the most suitable control strategy. By implementing effective control strategies, motor speed can be controlled with precision, ensuring optimal performance, energy efficiency, and reliable operation in various industrial and commercial applications.
Conclusion
Controlling the speed of electric motors is a vital aspect of optimizing their performance and achieving operational efficiency. By understanding the fundamentals of electric motors and the factors that influence speed, we can implement appropriate control methods to meet specific application requirements.
In this article, we explored various methods for controlling motor speed, including direct voltage control, pulse width modulation (PWM), and variable frequency drives (VFD). Each method offers unique advantages and considerations, allowing for precise and efficient speed control.
Direct voltage control provides a simple and cost-effective solution, particularly for DC motors. By adjusting the voltage supplied to the motor, speed can be regulated. However, direct voltage control may not offer the precision required in certain applications and can generate heat in the motor.
Pulse width modulation (PWM) is a widely used technique for DC and AC motor speed control. By rapidly switching the power supply on and off, the average voltage can be adjusted. PWM control offers precise speed control, energy efficiency, and reduced power dissipation.
Variable frequency drives (VFDs) are advanced devices that allow for precise and efficient speed control in AC induction motors. By varying the frequency and voltage of the power supply, VFDs provide optimized motor operation, energy savings, and improved mechanical protection.
Additionally, we discussed control strategies for motor speed, including open-loop, closed-loop, PID control, adaptive control, fuzzy logic control, and optimal control. Each strategy offers different levels of accuracy, adaptability, and complexity, allowing for customized speed control based on specific needs.
In conclusion, understanding the factors that affect motor speed and employing appropriate control methods and strategies are essential for optimizing motor performance and achieving energy efficiency. By carefully selecting the right control method and strategy, motors can operate at the desired speed, adapt to varying load conditions, and improve overall system performance.
Whether it’s in industrial settings, automotive applications, or everyday appliances, motor speed control plays a crucial role in driving efficiency, productivity, and cost savings. By harnessing the power of speed control, we can unlock the full potential of electric motors and create a more sustainable and optimized future.
Frequently Asked Questions about How To Control The Speed Of An Electric Motor
Was this page helpful?
At Storables.com, we guarantee accurate and reliable information. Our content, validated by Expert Board Contributors, is crafted following stringent Editorial Policies. We're committed to providing you with well-researched, expert-backed insights for all your informational needs.
0 thoughts on “How To Control The Speed Of An Electric Motor”