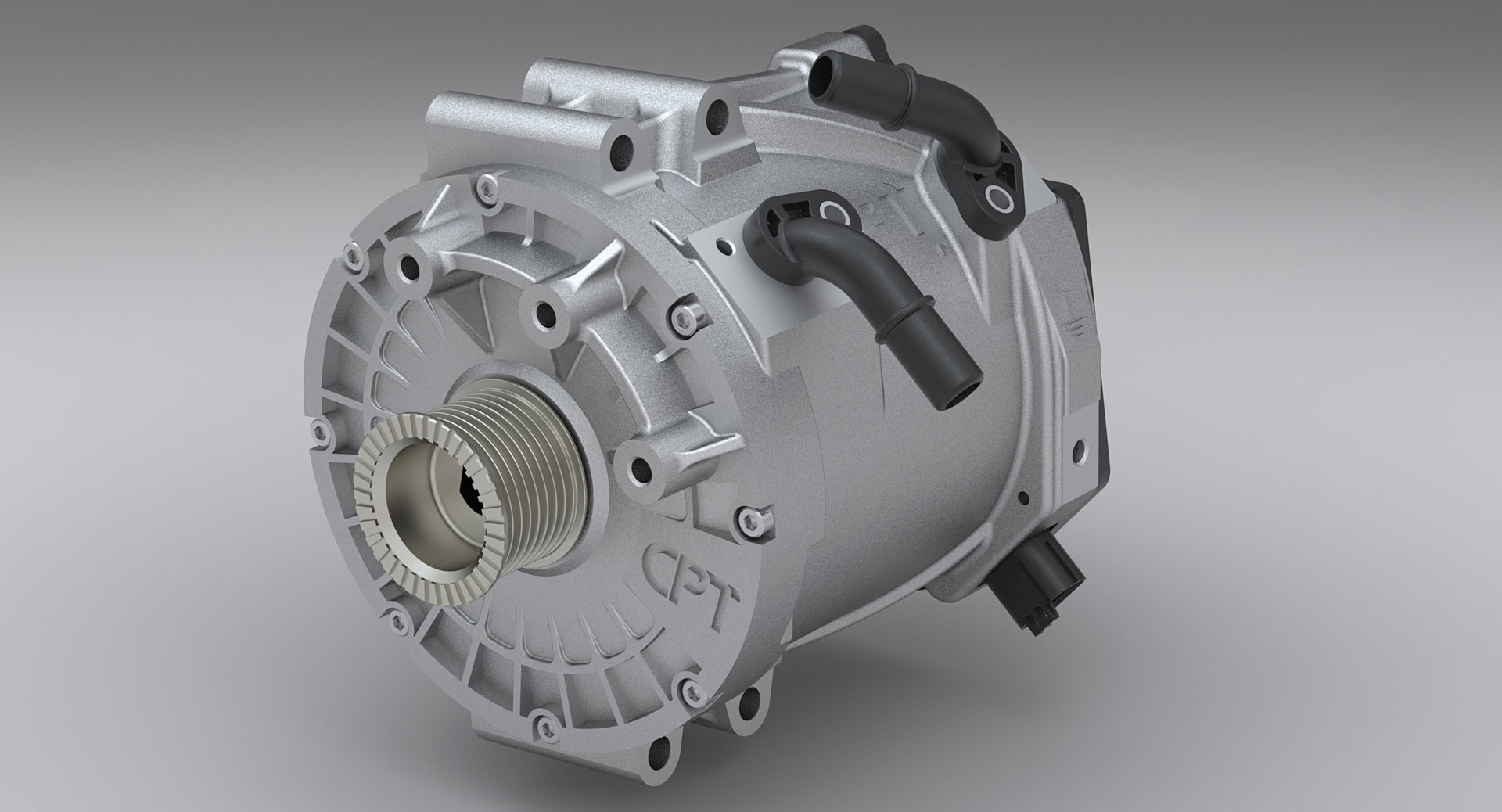
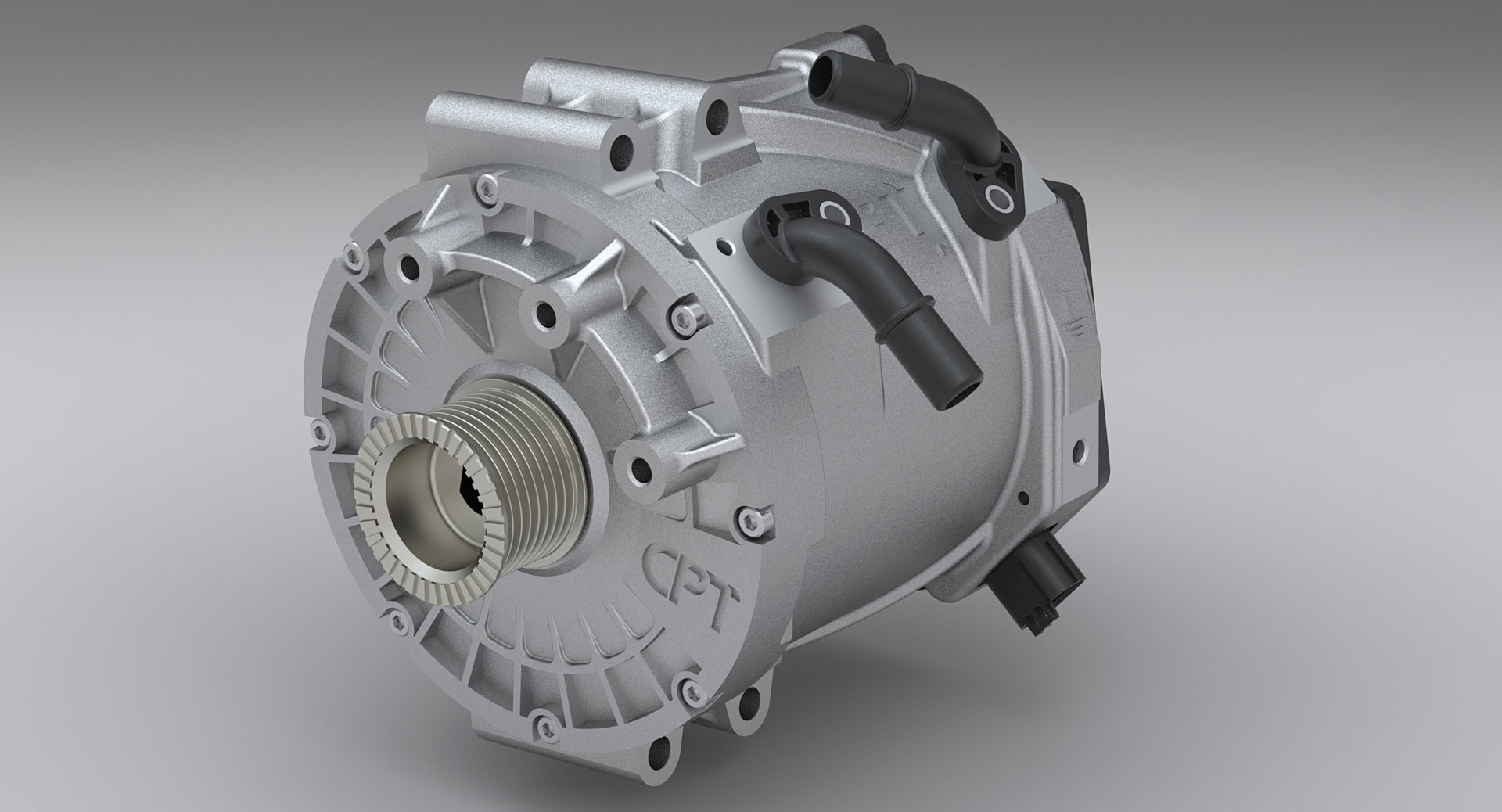
Articles
How To Reduce The Speed Of An Electric Motor
Modified: May 6, 2024
Learn effective techniques to reduce the speed of an electric motor in this informative article that covers various methods and tips.
(Many of the links in this article redirect to a specific reviewed product. Your purchase of these products through affiliate links helps to generate commission for Storables.com, at no extra cost. Learn more)
Introduction
Electric motors play a crucial role in various industries and applications, powering a wide range of machines and equipment. They are used in everything from household appliances to industrial machinery. While electric motors are designed to run at specific speeds, there are instances where it becomes necessary to reduce their speed.
In this article, we will explore the different methods to reduce the speed of an electric motor effectively. We will delve into the technical aspects of electric motors, discuss the factors that affect motor speed, and provide practical solutions to adjust motor speed according to specific requirements.
Understanding how electric motors work is essential before diving into the methods of speed reduction. Electric motors convert electrical energy into mechanical energy, generating rotational movement. They consist of two main components: the stator and the rotor. The stator comprises fixed coils that create a magnetic field, while the rotor consists of conductive bars or coils that rotate within the magnetic field.
The speed of an electric motor is typically determined by the frequency of the alternating current (AC) power supply and the number of poles on the motor. However, there are external factors that can influence motor speed.
Factors such as load, voltage, and motor windings can affect the speed performance of an electric motor. In situations where the motor speed needs to be reduced, there are several methods that can be employed.
The most common methods to reduce motor speed include using gear reduction, employing a Variable Frequency Drive (VFD), changing motor windings, controlling power supply voltage, and adjusting motor pulley size.
Each method has its own advantages and considerations, and the choice depends on various factors such as the application, available resources, and desired level of speed reduction.
In the following sections, we will delve into each of these methods, exploring their working principles, applications, and benefits. By the end of this article, you will have a comprehensive understanding of how to effectively reduce the speed of an electric motor based on your specific requirements.
Key Takeaways:
- Gear reduction offers precise speed control and increased torque, making it ideal for heavy load applications like conveyor systems.
- Variable Frequency Drives (VFDs) provide energy-efficient and versatile speed control, enabling soft starting and process optimization in various industrial applications.
Read more: How To Reduce Electric Motor Noise
Understanding Electric Motors
Electric motors are the backbone of many industrial applications, powering a wide range of machinery and equipment. They work based on the principle of electromagnetic induction.
The main components of an electric motor are the stator and the rotor. The stator is the stationary part of the motor and consists of a series of wire windings that create a magnetic field when an electrical current passes through them. The rotor, on the other hand, is the rotating part of the motor and contains conductive bars or coils that interact with the magnetic field generated by the stator.
When an electric current flows through the windings of the stator, it creates a rotating magnetic field. This magnetic field interacts with the conductive bars or coils in the rotor, causing the rotor to rotate. As the rotor rotates, it generates mechanical energy that can be used to perform work.
The speed at which an electric motor operates is determined by the frequency of the electrical current supplied to it. In most industrial applications, motors are designed to operate at a specific speed, known as the synchronous speed. The synchronous speed is determined by the frequency of the alternating current (AC) supply and the motor’s pole configuration.
However, there are instances where it becomes necessary to reduce the speed of an electric motor. This may be due to operational requirements or to ensure efficient performance in specific applications. Let’s explore the factors that can affect motor speed and the methods to reduce it effectively.
Factors Affecting Motor Speed
The speed of an electric motor is influenced by several factors. Understanding these factors is crucial to determine the best method for reducing motor speed effectively.
1. Load: The load refers to the mechanical resistance or work that the motor must overcome to perform its intended function. The higher the load on the motor, the slower the speed tends to be. Factors that contribute to the load include friction, inertia, and the mechanical characteristics of the equipment being driven by the motor.
2. Voltage: Voltage plays a significant role in motor speed. Most electric motors are designed to operate within a specific voltage range. If the voltage supplied to the motor is higher than its rated voltage, it can cause the motor to run faster. On the other hand, a lower voltage can result in a decrease in motor speed.
3. Motor Windings: The design of the motor windings also affects its speed. Electric motors can have different winding configurations, such as single-phase or three-phase windings. The number of poles in the motor and the arrangement of the windings determine the synchronous speed. Changing the motor windings can alter the speed characteristics of the motor.
4. Frequency: The frequency of the alternating current (AC) power supply is directly related to motor speed. The synchronous speed is determined by the frequency of the AC supply and the motor’s pole configuration. Higher frequencies result in higher speeds, while lower frequencies lead to slower speeds.
5. Mechanical Constraints: The physical constraints of the machinery or equipment driven by the motor can affect its speed. Friction, mechanical resistance, and other factors in the mechanical system can cause a decrease in motor speed.
6. Control Mechanisms: The control mechanisms used to regulate motor speed can also impact its operating speed. For example, variable speed drives such as Variable Frequency Drives (VFDs) can provide precise control over motor speed by varying the frequency of the supplied power.
Understanding these factors is essential in determining the appropriate method to reduce the speed of an electric motor. By addressing the specific factors influencing motor speed, it is possible to choose the most effective solution for achieving the desired speed reduction.
Methods to Reduce Motor Speed
There are several effective methods to reduce the speed of an electric motor, depending on the specific requirements and constraints of the application. Let’s explore the most common methods used in practice:
1. Using Gear Reduction: Gear reduction involves connecting the motor to a set of gears with different sizes. By using gears with a smaller size on the output side, the motor’s speed can be effectively reduced while increasing the torque. This method is commonly used in applications where precise speed control and high torque are required, such as conveyor systems and heavy machinery.
2. Using VFD (Variable Frequency Drive): A Variable Frequency Drive, or VFD, is an electronic device that allows for precise control of motor speed by adjusting the frequency of the supplied power. By varying the frequency, the VFD can change the speed of the motor to the desired level. This method is widely used in industrial applications where speed control is essential and offers flexibility and energy efficiency.
3. Changing Motor Windings: Altering the motor windings is another method to reduce motor speed. By rewiring the motor’s coils or changing the connection configuration, the speed characteristics of the motor can be modified. This method requires technical expertise and is typically used in applications where specific speed requirements need to be met.
4. Controlling Power Supply Voltage: The voltage supplied to an electric motor affects its speed. By adjusting the power supply voltage, either manually or using a voltage regulator, it is possible to reduce the motor’s speed. This method is relatively simple and can be used in applications where a moderate speed reduction is required.
5. Adjusting Motor Pulley Size: In applications that utilize a belt-driven system, changing the size of the motor pulley can effectively reduce motor speed. By using a larger pulley on the output side, the motor speed can be decreased while increasing the torque. This method is commonly used in conveyor systems, where speed adjustment is necessary for optimal operation.
Each method has its own advantages and considerations, and the choice depends on various factors such as the specific application requirements, available resources, and desired level of speed reduction. It is crucial to carefully evaluate the options and select the method that best meets the needs of the motor-driven system.
In the following sections, we will delve into each of these methods, exploring their working principles, applications, and benefits, providing you with a comprehensive understanding of how to effectively reduce the speed of an electric motor.
Method 1: Using Gear Reduction
Using gear reduction is a popular method for reducing the speed of an electric motor while increasing torque. It involves connecting the motor to a set of gears with different sizes. By using gears with a smaller size on the output side, the motor’s speed can be effectively reduced.
The gear reduction mechanism works based on the principle of gear ratios. A gear ratio is the ratio between the number of teeth on the driving gear (input gear) and the driven gear (output gear). The gear ratio determines how many times the output gear will rotate for each rotation of the input gear.
In the context of reducing motor speed, gear reduction is achieved by using gears with a higher number of teeth on the input side and gears with a lower number of teeth on the output side. This setup creates a mechanical advantage, as the larger input gear rotates at a higher speed but with lower torque, while the smaller output gear rotates at a lower speed but with increased torque.
This method is commonly used in applications where precise speed control and high torque output are required. For example, in conveyor systems, where a consistent and controlled material flow is essential, gear reduction ensures that the conveyor operates at the desired speed while handling heavy loads.
The benefits of using gear reduction include:
- Precision Speed Control: Gear reduction allows for precise control over the motor’s speed by adjusting the gear ratios. This enables fine-tuning the speed to match specific application requirements.
- Increased Torque: By reducing the motor’s speed and increasing the gear ratio, the torque output of the system is effectively amplified. This is particularly useful in applications that require high starting torque or the handling of heavy loads.
- Stable Operation: Gear reduction ensures a steady and consistent rotational speed, reducing the chances of speed fluctuations or instability in the motor-driven system.
- Longer Motor Lifespan: By reducing the motor’s speed, gear reduction can help in prolonging the lifespan of the motor by reducing wear and tear on its components.
It’s important to consider the gear ratio, gear quality, and compatibility with the motor when using gear reduction. Proper maintenance and lubrication of the gears are also crucial to ensure optimal performance and longevity.
Overall, gear reduction is a reliable method for reducing motor speed while maintaining high torque output. With its precision control and suitability for various applications, gear reduction is widely used across industries to meet specific speed requirements and ensure efficient operation of motor-driven systems.
To reduce the speed of an electric motor, you can use a variable frequency drive (VFD) to control the motor’s speed by adjusting the frequency of the electrical supply. This allows for precise speed control and energy savings.
Method 2: Using VFD (Variable Frequency Drive)
A Variable Frequency Drive (VFD) is an electronic device that allows for precise control of motor speed by adjusting the frequency of the supplied power. This method of speed reduction offers flexibility, energy efficiency, and precise control over motor speed.
With a VFD, the electrical power from the source is converted into direct current (DC) and then back to alternating current (AC) at the desired frequency. By adjusting the frequency, the speed of the motor can be effectively controlled without the need for mechanical gear reduction.
The main advantage of using a VFD is its ability to provide variable speed control over a wide range. This makes it ideal for applications where speed adjustment is frequently required, such as in HVAC systems, pumps, and fans.
Here’s how a VFD works:
- The AC power from the source is converted to DC power using a rectifier.
- The DC power is then passed through an inverter, which converts it back to AC at the desired frequency.
- The VFD monitors the load and adjusts the frequency of the AC power supply to control the motor’s speed.
By adjusting the frequency, the VFD can vary the speed of the motor smoothly and precisely. This allows for precise control over the motor’s speed, enabling it to meet the specific requirements of the application.
Using a VFD to reduce motor speed offers several benefits:
- Precision Speed Control: A VFD provides precise control over motor speed, allowing for fine-tuning to match the desired operating conditions.
- Energy Efficiency: VFDs can significantly improve energy efficiency by adjusting the motor speed to match the actual load requirements. This results in reduced energy consumption and cost savings.
- Soft Starting: VFDs allow for soft starting of the motor, gradually ramping up the speed to minimize stress and wear on the motor and mechanical components. This helps to extend the lifespan of the motor and reduce maintenance needs.
- Process Optimization: With the ability to adjust motor speed on-the-fly, VFDs enable optimization of processes by fine-tuning the speed to maximize efficiency and productivity.
However, it’s important to consider the compatibility between the motor and the VFD. Not all motors are suitable for use with a VFD, especially older or specialized motors. It’s crucial to consult the motor manufacturer’s specifications and ensure compatibility before implementing a VFD for speed reduction.
In summary, using a Variable Frequency Drive (VFD) is a versatile and efficient method for reducing motor speed. With its precise control, energy efficiency, and flexibility, a VFD offers an excellent solution for applications that require dynamic speed adjustments and optimal motor performance.
Method 3: Changing Motor Windings
Changing the motor windings is a method commonly used to alter the speed characteristics of an electric motor. By rewiring the motor’s coils or changing the connection configuration, the speed of the motor can be modified to meet specific requirements.
The speed of an electric motor is influenced by the design of the motor windings. Electric motors can have different winding configurations, such as single-phase or three-phase windings. The number of poles in the motor and the arrangement of the windings determine the synchronous speed.
To reduce the speed of a motor by changing the windings, there are a few possible approaches:
- Reconnecting Coils: By changing the connection pattern of the motor’s coils, the speed characteristics can be altered. This method involves rewiring the motor to achieve a different grouping or arrangement of the coils. It allows for customizing the speed reduction based on specific requirements.
- Adding Series or Parallel Connections: Another method involves adding or modifying the series or parallel connections of the motor’s coils. By changing the electrical configuration of the motor, the speed can be adjusted accordingly. This method allows for more flexibility in achieving the desired speed reduction.
- External Resistors: In some cases, external resistors can be added to the motor circuit to modify its speed characteristics. The resistors increase the total resistance in the circuit, which reduces the motor’s speed. However, this method may result in energy loss and decreased overall efficiency.
Changing motor windings to alter the speed typically requires technical expertise and knowledge of motor wiring diagrams and specifications. It is important to consult the motor manufacturer’s recommendations or seek assistance from a qualified electrician to ensure the modifications are done correctly and safely.
Depending on the motor design and winding configuration, changing motor windings can present certain challenges and limitations. Some motors may not be suitable for extensive modification, while others may require specific modifications to achieve the desired speed reduction.
It’s important to consider the specific needs of the application and consult with experts to determine if changing motor windings is a viable option for reducing motor speed.
In summary, changing motor windings is a method that allows for customizing the speed reduction of an electric motor. By rewiring the motor’s coils or modifying the connection configuration, the speed characteristics can be altered to meet specific requirements. However, it requires technical expertise and a thorough understanding of the motor’s design and specifications.
Method 4: Controlling Power Supply Voltage
Controlling the power supply voltage is a straightforward method for reducing the speed of an electric motor. By adjusting the voltage supplied to the motor, either manually or using a voltage regulator, the motor’s speed can be effectively reduced.
The speed of an electric motor is directly influenced by the voltage applied to it. Typically, electric motors are designed to operate within a specific voltage range. If the voltage supplied to the motor is higher than its rated voltage, it can cause the motor to run faster. Conversely, a lower voltage can result in a decrease in motor speed.
To reduce motor speed by controlling the power supply voltage, there are a few approaches that can be taken:
- Manual Voltage Adjustment: In some cases, it is possible to manually adjust the power supply voltage by using a variable transformer or voltage regulator. By lowering the voltage supplied to the motor, its speed can be reduced. However, this method may not offer precise control over the speed reduction and should be used with caution.
- Using a Voltage Regulator: A voltage regulator is an electronic device that automatically adjusts the voltage supplied to the motor, ensuring a consistent and controlled voltage level. By lowering the output voltage of the regulator, the motor’s speed can be reduced. This method provides more precise control and is commonly used in applications where accurate speed reduction is required.
Controlling power supply voltage to reduce motor speed offers a few benefits:
- Simplicity: Adjusting the power supply voltage is a relatively simple method that does not require complex modifications to the motor or additional equipment.
- Cost-Effective: Implementing voltage control for speed reduction is often cost-effective compared to other methods, as it may not require significant investments in additional equipment or system modifications.
- Suitable for Various Motors: This method can be applied to different types of motors, regardless of their winding configuration or motor design.
However, it’s important to note that there are limitations when using this method. Lowering the voltage can result in a decrease in motor torque, which may impact the motor’s ability to handle certain loads or perform specific tasks. It’s crucial to consider the motor’s torque requirements and ensure that reducing the voltage will not compromise its performance.
It’s also essential to consult the motor manufacturer’s specifications and guidelines regarding safe voltage ranges and operating conditions. Modifying the power supply voltage beyond the recommended limits may lead to motor damage or reduced lifespan.
In summary, controlling the power supply voltage is a simple and cost-effective method for reducing the speed of an electric motor. It offers flexibility and can be applied to various motor types. However, it’s important to assess the motor’s torque requirements and follow manufacturer recommendations to ensure safe and optimal operation.
Method 5: Adjusting Motor Pulley Size
Adjusting the motor pulley size is a practical method for reducing the speed of an electric motor, particularly in applications that utilize a belt-driven system. By changing the size of the motor pulley, the speed of the driven equipment can be effectively adjusted.
In a belt-driven system, the motor is connected to the driven equipment, such as a conveyor or a pump, using a belt and pulleys. The speed ratio between the motor and the driven equipment is determined by the sizes of the pulleys involved.
To reduce the motor speed by adjusting the pulley size, there are two main approaches:
- Decreasing the Size of the Motor Pulley: By using a smaller pulley on the motor shaft, the speed of the driven equipment can be effectively reduced. A smaller motor pulley size increases the speed ratio, resulting in a slower rotational speed in the equipment being driven.
- Increasing the Size of the Driven Equipment Pulley: Alternatively, the speed can be reduced by using a larger pulley on the driven equipment. A larger pulley on the driven equipment decreases the speed ratio, resulting in a slower rotational speed.
Adjusting the motor pulley size offers several advantages:
- Simple Implementation: The method of adjusting pulley size is relatively straightforward, as it involves replacing the pulleys with ones of suitable sizes.
- Cost-Effective: Changing pulley sizes is often a cost-effective solution, requiring minimal investment compared to other methods of speed reduction.
- Flexibility: This method provides flexibility in achieving the desired speed reduction by selecting the appropriate pulley sizes based on the specific requirements of the application.
- No Impact on Torque: Adjusting the pulley size does not have a direct impact on the motor’s torque output, allowing the motor to maintain its torque capabilities.
However, it’s important to consider a few factors when implementing this method. Changing the pulley sizes will affect the belt length and tension, and it’s crucial to ensure that the new belt length is appropriate and properly tensioned. Incorrect belt tension can lead to slippage, decreased efficiency, and premature wear.
Additionally, it’s important to maintain proper alignment between the pulleys to prevent belt misalignment and potential damage to the motor or driven equipment.
Overall, adjusting the motor pulley size is a practical and cost-effective method for reducing motor speed in belt-driven systems. By selecting the appropriate pulley sizes and ensuring proper belt tension and alignment, this method can provide the desired speed reduction without compromising torque capabilities or requiring complex modifications.
Conclusion
Reducing the speed of an electric motor is a common requirement in many applications, and there are several effective methods available to achieve this. Understanding the different factors that affect motor speed is crucial in selecting the appropriate method for speed reduction.
We explored five methods for reducing motor speed: using gear reduction, employing a Variable Frequency Drive (VFD), changing motor windings, controlling power supply voltage, and adjusting motor pulley size. Each method has its own advantages and considerations, and the choice depends on various factors such as the specific application requirements, available resources, and desired level of speed reduction.
Using gear reduction provides precision speed control and increased torque output, making it suitable for applications requiring heavy loads and precise speed adjustments. VFDs offer versatility and energy efficiency, allowing for precise control over motor speed and soft starting capability. Changing motor windings offers customization of speed reduction, but it requires technical expertise and consideration of motor specifications.
Controlling power supply voltage is a straightforward method that offers simplicity and cost-effectiveness, but it should be used with caution to ensure optimal motor performance. Adjusting motor pulley size is a practical solution in belt-driven systems, providing flexibility and ease of implementation.
In conclusion, the choice of method for reducing motor speed depends on the specific requirements of the application, the available resources, and the desired level of speed reduction. It is crucial to assess these factors and consult with experts or follow manufacturer recommendations to ensure safe and optimal operation.
By selecting and implementing the appropriate method, it is possible to effectively reduce the speed of an electric motor, allowing for efficient and precise operation in various industrial and commercial applications.
Excited to take your understanding of electric motors further? Dive into our detailed review of the best options for controlling motor speed, perfect for optimizing performance in 2024. For those looking to slash energy bills, don't miss our guide on using air conditioning more efficiently. Both articles pack practical tips and are just a click away, promising to enhance your knowledge and help achieve more with less!
Frequently Asked Questions about How To Reduce The Speed Of An Electric Motor
Was this page helpful?
At Storables.com, we guarantee accurate and reliable information. Our content, validated by Expert Board Contributors, is crafted following stringent Editorial Policies. We're committed to providing you with well-researched, expert-backed insights for all your informational needs.
0 thoughts on “How To Reduce The Speed Of An Electric Motor”