Home>Furniture & Design>Interior Design Trends>How To Mold Glass
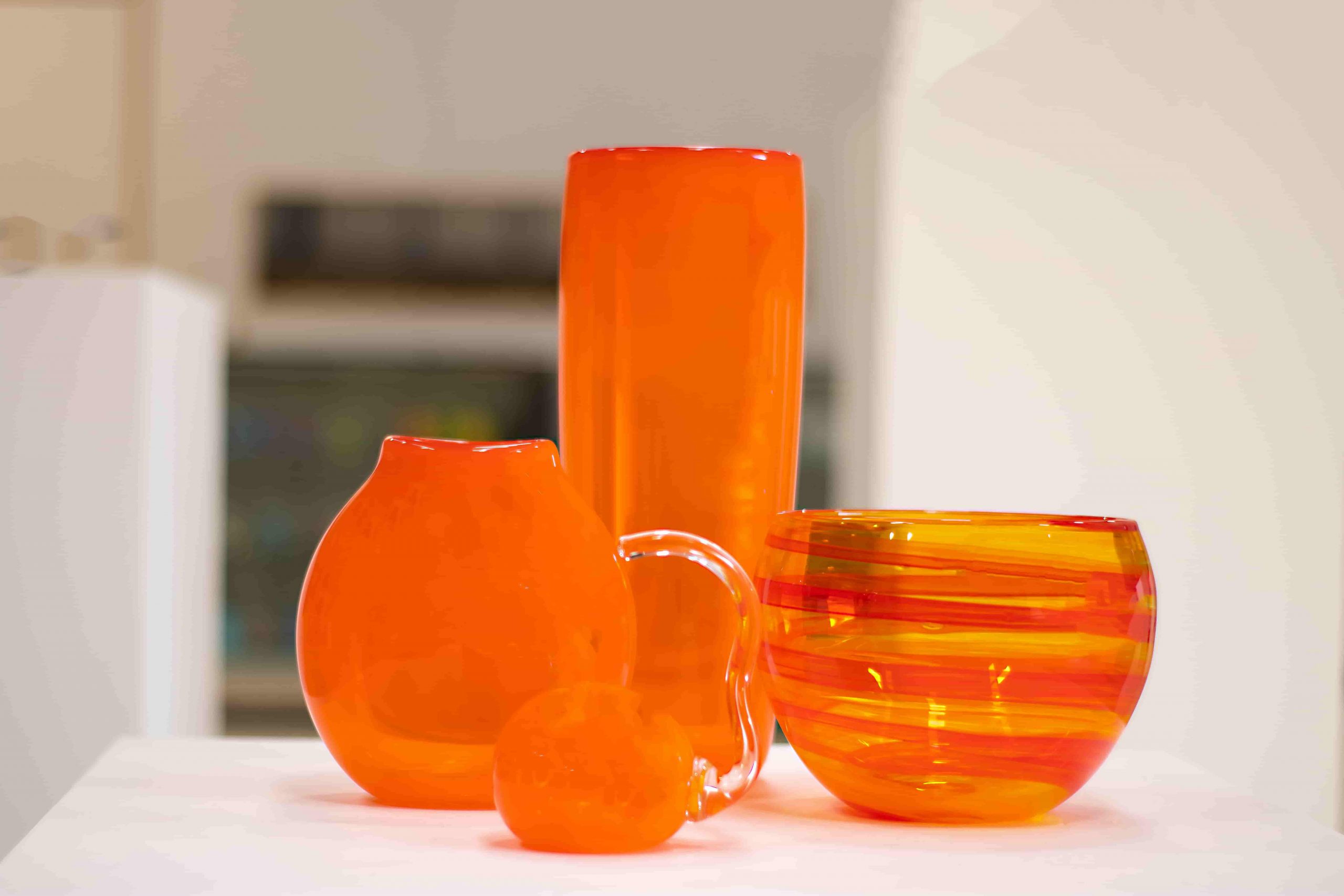
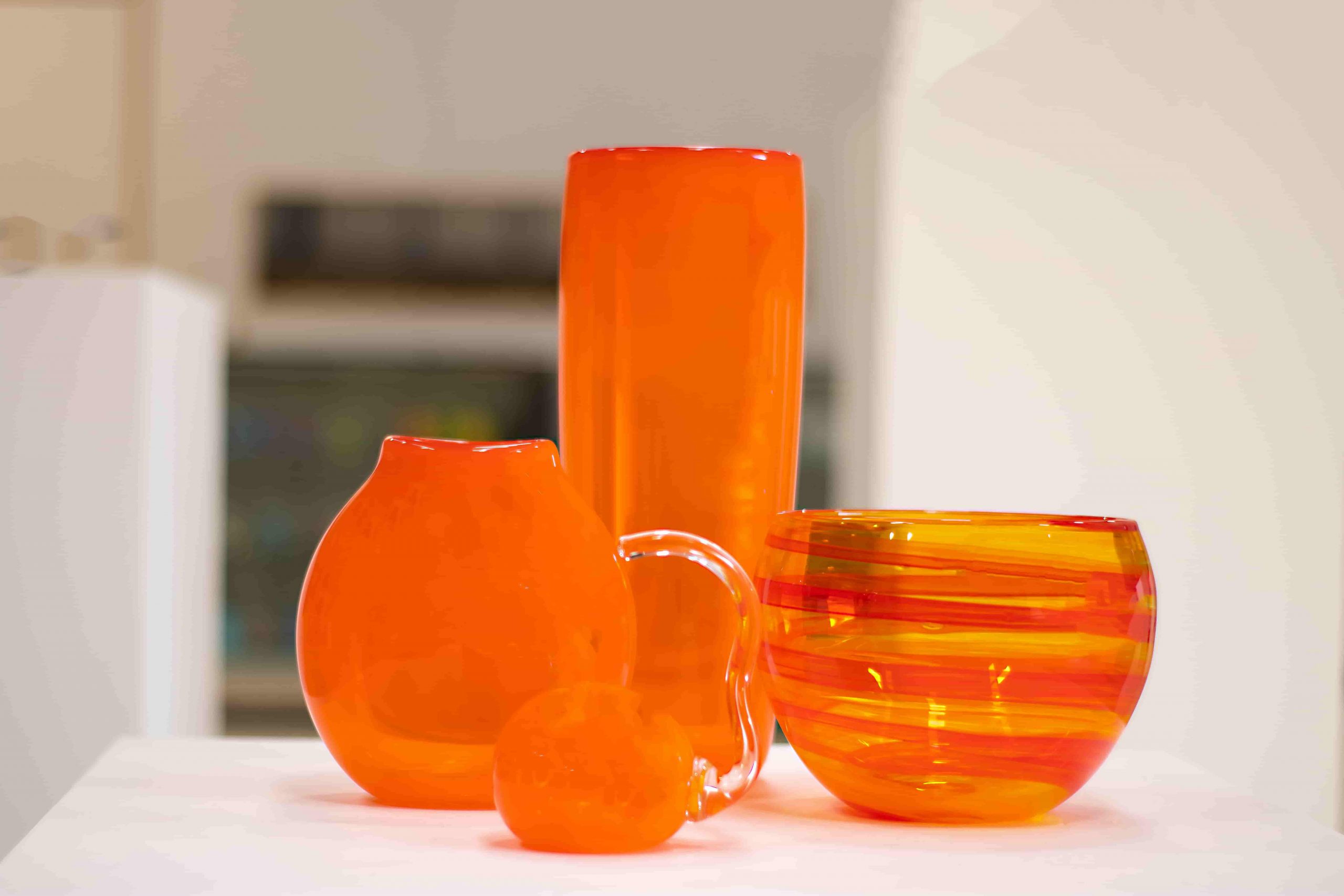
Interior Design Trends
How To Mold Glass
Modified: February 18, 2024
Discover the latest interior design trends with our guide on how to mold glass. Elevate your space with innovative glass molding techniques and create a modern, stylish interior.
(Many of the links in this article redirect to a specific reviewed product. Your purchase of these products through affiliate links helps to generate commission for Storables.com, at no extra cost. Learn more)
Introduction
Glass molding is a fascinating and intricate process that has been practiced for centuries, evolving from traditional hand-crafting methods to advanced industrial techniques. This art form combines the delicate nature of glass with the precision of molding, resulting in exquisite and functional glassware, decorative items, and architectural elements. Whether you are a novice enthusiast or a seasoned professional, understanding the fundamentals of glass molding is essential for achieving exceptional results.
The art of glass molding encompasses a wide range of techniques, each with its own unique characteristics and applications. From the ancient art of glassblowing to modern precision molding, the process involves shaping molten glass into desired forms, allowing for endless creative possibilities. Whether it's creating intricate glass sculptures, designing custom glassware, or producing architectural glass components, the molding process offers a versatile platform for artistic expression and functional design.
In this comprehensive guide, we will delve into the intricate world of glass molding, exploring the various techniques, materials, and considerations involved in the process. From understanding the properties of different types of glass to mastering the art of shaping and finishing, this guide will provide valuable insights for both beginners and experienced artisans. Whether you are passionate about creating unique glass art or seeking to expand your knowledge of glass molding, this guide will serve as a valuable resource for unlocking the potential of this captivating craft.
As we embark on this journey through the art of glass molding, we will unravel the mysteries of this ancient craft, uncovering the secrets of transforming molten glass into exquisite works of art. By gaining a deeper understanding of the intricate processes and techniques involved, you will be empowered to unleash your creativity and bring your glass molding aspirations to life. Join us as we explore the art, science, and magic of glass molding, and discover the endless possibilities that await within this captivating realm.
Key Takeaways:
- Glass molding involves techniques like glassblowing, pressing, and casting to create stunning glassware, decorative items, and architectural elements, showcasing the versatility of molten glass.
- Choosing the right type of glass, meticulous preparation, and precise cooling and finishing are crucial for creating exquisite glass products that embody artistry, vision, and unwavering commitment to excellence.
Read more: How To Make Glass Molds
Understanding the Glass Molding Process
The glass molding process is a complex and intricate art form that involves transforming raw materials into exquisite glass products through a series of carefully orchestrated steps. From the initial preparation of the glass to the final finishing touches, each stage of the molding process requires precision, skill, and a deep understanding of the unique properties of glass.
At its core, the glass molding process revolves around the manipulation of molten glass to achieve specific shapes, textures, and forms. This can be achieved through various techniques, including glassblowing, pressing, and casting, each offering distinct advantages and applications.
Glassblowing, one of the oldest and most revered techniques, involves shaping molten glass by blowing air into a tube, creating intricate and organic forms with remarkable precision. This method allows artisans to craft delicate glass sculptures, ornate vases, and decorative ornaments, showcasing the fluidity and versatility of molten glass.
Pressing, on the other hand, involves molding molten glass between two or more molds to create uniform and precise shapes. This technique is commonly used in the production of glassware, such as drinking glasses, bowls, and plates, where consistency and accuracy are paramount.
Casting, another popular method, entails pouring molten glass into a mold to create three-dimensional objects with intricate details and textures. This technique is often employed in the production of architectural glass components, decorative panels, and sculptural elements, offering unparalleled flexibility in design and form.
Regardless of the specific technique employed, the glass molding process requires a deep understanding of the unique properties of glass, including its viscosity, thermal behavior, and structural integrity. By mastering these fundamental principles, artisans can harness the transformative power of molten glass, bringing their creative visions to life with unparalleled precision and artistry.
As we delve deeper into the art of glass molding, we will explore the nuances of each technique, unraveling the secrets of manipulating molten glass to achieve stunning results. By gaining a comprehensive understanding of the glass molding process, you will be equipped with the knowledge and insight to embark on your own creative journey, unlocking the boundless potential of this captivating art form.
Choosing the Right Type of Glass
Selecting the appropriate type of glass is a critical aspect of the glass molding process, as it directly influences the visual, functional, and structural characteristics of the final product. The diverse range of glass types available offers artisans a wealth of options, each with unique properties and applications. Understanding the distinct qualities of different types of glass is essential for achieving desired aesthetic effects, ensuring structural integrity, and meeting specific functional requirements.
One of the most common types of glass used in molding is soda-lime glass, renowned for its versatility, affordability, and ease of molding. This type of glass is ideal for creating everyday glassware, decorative items, and architectural components, offering a balance of clarity, durability, and workability. Its composition, which includes sodium carbonate and lime, provides excellent melting properties, making it well-suited for various molding techniques, including blowing, pressing, and casting.
For applications that demand exceptional clarity and optical purity, borosilicate glass emerges as a preferred choice. Renowned for its high resistance to thermal shock and chemical corrosion, borosilicate glass is often used in the production of laboratory glassware, scientific instruments, and specialized lighting components. Its superior thermal properties make it well-suited for precision molding processes, allowing artisans to create intricate and heat-resistant glass products with exceptional clarity and durability.
In the realm of artistic glass molding, lead crystal glass stands out for its unparalleled brilliance, refractive qualities, and luxurious aesthetic appeal. Comprising a blend of silica, lead oxide, and other minerals, lead crystal glass exudes a timeless elegance and sophistication, making it a coveted material for crafting exquisite glass sculptures, decorative ornaments, and fine tableware. Its exceptional refractive index and lustrous finish elevate the visual impact of molded glass products, adding a touch of opulence and allure to any artistic creation.
In addition to these prominent glass types, specialty glasses such as tempered glass, laminated glass, and colored glass offer artisans a diverse palette of options for creating custom-tailored glass products. Tempered glass, known for its exceptional strength and safety features, is often used in architectural applications, while laminated glass, composed of multiple layers for enhanced security and sound insulation, finds its niche in structural and decorative elements. Colored glass, infused with metal oxides or other pigments, allows artisans to imbue their creations with vibrant hues and captivating visual effects, adding a layer of artistic expression to the molding process.
By carefully considering the unique properties and applications of different types of glass, artisans can make informed decisions when selecting the most suitable material for their molding projects. Whether aiming for durability, optical clarity, artistic expression, or functional performance, the right type of glass serves as the foundation for bringing creative visions to life, shaping the identity and character of each molded glass creation.
Preparing the Glass for Molding
Before embarking on the intricate process of molding glass, meticulous preparation of the raw material is essential to ensure optimal results and the realization of the artisan's creative vision. The preparation phase encompasses a series of crucial steps aimed at refining the glass composition, enhancing workability, and minimizing potential imperfections in the final product.
The first step in preparing glass for molding involves the careful selection of raw materials, taking into account the desired characteristics of the final glass product. The quality and purity of the raw materials, including silica sand, soda ash, limestone, and other additives, play a pivotal role in determining the optical clarity, thermal properties, and chemical resistance of the glass. By meticulously sourcing and blending these raw materials, artisans can tailor the glass composition to meet specific aesthetic, functional, and performance requirements.
Once the raw materials are selected and blended, they undergo a rigorous melting process in a high-temperature furnace, where they are transformed into molten glass. This molten glass is then carefully monitored and refined to achieve the desired viscosity, homogeneity, and thermal stability, ensuring optimal workability during the molding process. The precise control of temperature and chemical composition is paramount in achieving consistent and predictable glass behavior, laying the foundation for successful molding outcomes.
In addition to refining the chemical composition and thermal properties of the molten glass, artisans may also introduce colorants, opacifiers, or other additives to imbue the glass with specific visual effects and aesthetic qualities. This customization allows for the creation of colored, textured, or translucent glass products, adding a layer of artistic expression and visual intrigue to the molding process.
Furthermore, the molten glass is carefully conditioned to eliminate bubbles, seeds, or other imperfections that could compromise the integrity and visual appeal of the final product. This meticulous refining process involves controlled cooling and reheating of the molten glass, allowing any trapped gases or impurities to dissipate, resulting in a pristine and flawless glass composition ready for molding.
By meticulously preparing the glass for molding, artisans lay the groundwork for achieving exceptional results, ensuring that the raw material is refined, homogenized, and optimized for the intricate shaping and manipulation that lies ahead. This meticulous attention to detail and craftsmanship sets the stage for the seamless transition from molten glass to exquisite molded creations, embodying the artisan's skill, vision, and dedication to the art of glass molding.
When molding glass, always wear protective gear like gloves and goggles to prevent burns and injuries. Glass can reach high temperatures and can be dangerous if mishandled.
Molding Techniques
Molding techniques encompass a diverse array of methods for shaping and manipulating molten glass into a myriad of forms, each offering unique possibilities for artistic expression and functional design. From the ancient art of glassblowing to the precision of modern casting processes, artisans have at their disposal a rich tapestry of techniques, each with its own distinct characteristics and applications.
Glassblowing, often regarded as one of the most iconic and revered molding techniques, involves the skilled manipulation of molten glass through the use of a blowpipe and various hand tools. Artisans deftly shape the molten glass by blowing air into the pipe, creating intricate and organic forms with remarkable precision. This centuries-old technique allows for the creation of delicate glass sculptures, ornate vases, and decorative ornaments, showcasing the fluidity and versatility of molten glass.
Pressing, another prominent molding technique, entails the use of molds to shape molten glass into precise and uniform forms. By carefully pressing the molten glass between molds, artisans can create a wide range of glassware, including drinking glasses, bowls, and plates, with consistent shapes and dimensions. This method is favored for its ability to produce large quantities of identical glass products with exceptional accuracy and efficiency.
Casting, a versatile and sophisticated technique, involves pouring molten glass into molds to create three-dimensional objects with intricate details and textures. This method allows artisans to produce architectural glass components, decorative panels, and sculptural elements with unparalleled flexibility in design and form. By utilizing molds of varying complexity, artisans can achieve stunning visual effects and intricate patterns, adding depth and dimension to their glass creations.
Lampworking, a specialized form of glass molding, involves the use of a stationary torch to melt and shape glass rods and tubes into intricate designs and miniature sculptures. This technique is favored for its precision and control, allowing artisans to create intricate glass beads, figurines, and small-scale decorative elements with remarkable detail and artistry.
By mastering these diverse molding techniques, artisans can unleash their creativity and bring their artistic visions to life with unparalleled precision and craftsmanship. Each technique offers a unique set of possibilities, allowing artisans to explore the boundless potential of molten glass and create stunning works of art that captivate the imagination and inspire awe.
Cooling and Finishing the Molded Glass
Once the intricate process of shaping and molding the glass is complete, the crucial stage of cooling and finishing the molded glass commences. This phase is essential for ensuring the structural integrity, visual clarity, and surface quality of the glass products, marking the transition from molten fluidity to solidified elegance.
The cooling process is a delicate balance of controlled temperature reduction, allowing the molten glass to gradually solidify without introducing internal stresses or imperfections. This gradual cooling, often facilitated in temperature-controlled annealing ovens, is critical for relieving internal strains and preventing the formation of cracks or fractures in the glass. By carefully regulating the cooling rate and duration, artisans can achieve optimal stress relief and dimensional stability, ensuring that the molded glass retains its intended shape and integrity.
As the glass undergoes the gradual cooling process, meticulous attention is also directed towards the finishing touches that elevate the visual appeal and tactile quality of the molded products. This may involve techniques such as polishing, grinding, or etching, aimed at refining the surface texture, removing imperfections, and enhancing the overall aesthetic presentation of the glass. Polishing, in particular, imparts a lustrous sheen to the glass surface, accentuating its clarity and brilliance, while grinding allows for precise shaping and smoothing of edges, ensuring a flawless and refined finish. Additionally, etching techniques can be employed to create intricate patterns, textures, or decorative motifs, adding a layer of artistic expression and visual intrigue to the finished glass products.
Furthermore, the process of finishing the molded glass may also encompass the application of protective coatings or treatments to enhance durability, resistance to environmental factors, and longevity. This may include the application of specialized coatings for UV protection, scratch resistance, or enhanced chemical durability, depending on the intended application and functional requirements of the glass products. These finishing treatments not only safeguard the integrity of the glass but also contribute to its longevity and performance in diverse environments.
By meticulously orchestrating the cooling and finishing processes, artisans ensure that the molded glass products emerge with impeccable clarity, structural resilience, and captivating visual allure. This meticulous attention to detail and craftsmanship underscores the dedication and artistry inherent in the glass molding process, culminating in the creation of exquisite glass products that embody the artisan's skill, vision, and unwavering commitment to excellence.
Conclusion
In conclusion, the art of glass molding stands as a testament to the timeless marriage of craftsmanship, creativity, and scientific precision. From the ancient traditions of glassblowing to the cutting-edge innovations in precision molding, this captivating art form continues to captivate and inspire artisans and enthusiasts alike. The journey through the intricate world of glass molding has unveiled the profound complexities and boundless possibilities inherent in this age-old craft.
Throughout this comprehensive guide, we have delved into the fundamental principles, techniques, and considerations that define the art of glass molding. We have explored the diverse range of molding techniques, each offering unique avenues for artistic expression and functional design. From the delicate art of glassblowing to the precision of pressing and casting, artisans have at their disposal a rich tapestry of methods for shaping and manipulating molten glass into exquisite forms.
Furthermore, the critical role of selecting the right type of glass has been underscored, emphasizing the profound impact of glass composition on the visual, functional, and structural qualities of the final products. Whether it is the versatility of soda-lime glass, the optical purity of borosilicate glass, or the luxurious allure of lead crystal, the choice of glass type serves as a cornerstone for realizing creative visions and achieving desired aesthetic effects.
The meticulous preparation of glass for molding has been highlighted as a pivotal phase, laying the groundwork for successful outcomes by refining the glass composition, enhancing workability, and minimizing potential imperfections. This preparatory phase sets the stage for the seamless transition from raw materials to molten glass, ensuring that the material is optimized for the intricate shaping and manipulation that lies ahead.
As the molten glass is carefully shaped and molded, the cooling and finishing processes play a crucial role in solidifying the structural integrity, visual clarity, and surface quality of the glass products. The delicate orchestration of controlled cooling, surface refinement, and protective treatments culminates in the emergence of exquisite glass creations that embody the artisan's skill, vision, and unwavering commitment to excellence.
In essence, the art of glass molding transcends mere craftsmanship, evolving into a harmonious fusion of artistry, science, and innovation. It is a testament to the enduring allure of glass as a medium for creative expression, offering a canvas for boundless imagination and technical mastery. As we conclude this exploration of glass molding, we are reminded of the profound legacy and enduring relevance of this captivating art form, inspiring generations of artisans to push the boundaries of creativity and craftsmanship in the timeless pursuit of molding molten glass into works of enduring beauty and significance.
Frequently Asked Questions about How To Mold Glass
Was this page helpful?
At Storables.com, we guarantee accurate and reliable information. Our content, validated by Expert Board Contributors, is crafted following stringent Editorial Policies. We're committed to providing you with well-researched, expert-backed insights for all your informational needs.
0 thoughts on “How To Mold Glass”