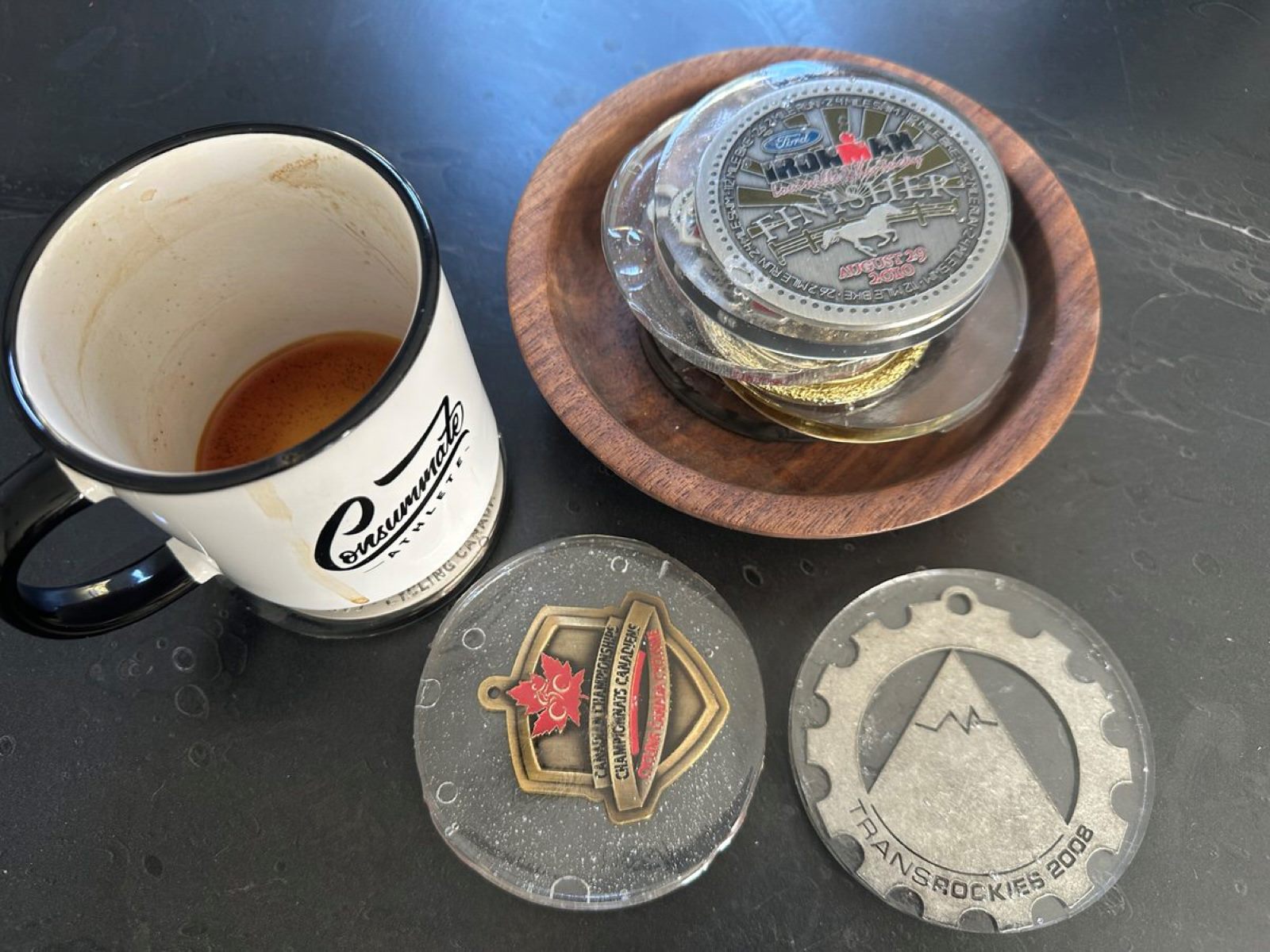
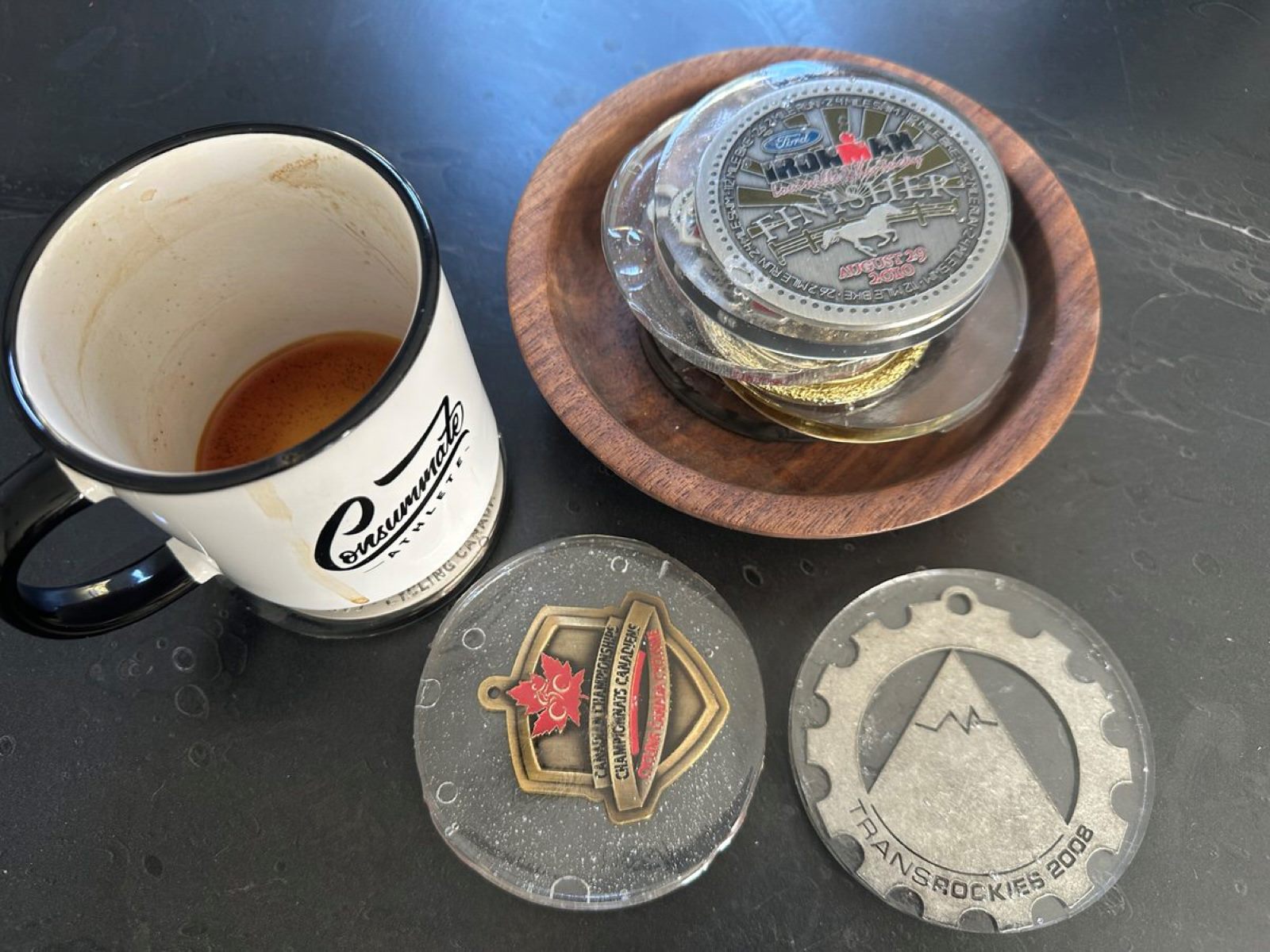
Tableware
How To Seal Resin Coasters
Modified: January 4, 2024
Learn how to properly seal resin coasters for long-lasting durability. Enhance the functionality and beauty of your tableware with this step-by-step tutorial.
(Many of the links in this article redirect to a specific reviewed product. Your purchase of these products through affiliate links helps to generate commission for Storables.com, at no extra cost. Learn more)
Introduction
Resin coasters have become increasingly popular for their beauty, durability, and versatility. These coasters add a touch of elegance to any table setting, making them a perfect addition to your home decor or a thoughtful gift for a loved one. However, to keep your resin coasters looking their best, it’s important to seal them properly. Sealing resin coasters not only enhances their appearance but also protects them from scratches, moisture, and UV damage.
In this article, we will guide you through the step-by-step process of sealing resin coasters. We will cover everything from preparing the coasters to applying the sealant, ensuring that you achieve a professional and long-lasting finish. So, let’s dive in and get started!
Key Takeaways:
- Protect and enhance resin coasters by following a thorough sealing process, ensuring longevity and professional-looking results. Use high-quality materials and take care in each step for durable and beautiful tableware.
- Sealing resin coasters involves meticulous preparation, precise application, and attention to detail. Achieve a flawless finish by cleaning, mixing, pouring, removing air bubbles, curing, sanding, cleaning again, and applying the sealant.
Read more: How To Resin Coasters
Materials Needed
Before you begin sealing your resin coasters, it’s essential to gather all the necessary materials. Having everything at hand will make the process smoother and more efficient. Here is a list of the materials you’ll need:
- Resin coasters
- Resin sealant
- Paintbrush or foam brush
- Plastic cups
- Stir sticks
- Disposable gloves
- Disposable mixing containers
- Sandpaper (various grits)
- Lint-free cloth
- Drop cloth or newspaper
- Masking tape
It’s important to choose high-quality resin and sealant products to ensure the best results. Look for ones that are specifically designed for sealing resin or epoxy surfaces. The right products will provide a durable and glossy finish that will protect your coasters for years to come.
Make sure to work in a well-ventilated area and wear protective gloves to avoid direct contact with the resin and sealant. Additionally, lay down a drop cloth or newspaper to protect your work surface from any spills or drips.
Step 1: Preparing the Resin Coasters
Before you can seal your resin coasters, it’s crucial to prepare them properly. This involves removing any dust, dirt, or residue that may be on the surface. Follow these steps to ensure your coasters are clean and ready for sealing:
- Start by gently wiping the surface of each coaster with a lint-free cloth to remove any loose debris.
- Next, fill a bowl with warm water and add a few drops of mild dish soap. Dip the cloth into the soapy water and wring out any excess liquid.
- Gently scrub the surface of each coaster with the damp cloth to remove any stubborn stains or residue. Be careful not to scrub too hard as it may damage the resin.
- Rinse the coasters with clean water to remove the soap residue.
- Finally, pat the coasters dry with a clean lint-free cloth and let them air dry completely.
By properly cleaning the surface of the coasters, you’ll ensure that the sealant adheres well and provides a smooth and flawless finish.
Step 2: Mixing the Resin
Once your resin coasters are clean and dry, it’s time to mix the resin. Follow these steps to ensure a proper mixture:
- Put on your disposable gloves to protect your hands.
- Prepare your mixing container by following the manufacturer’s instructions. It is important to use a container with measurements to ensure the correct resin to hardener ratio.
- Pour the appropriate amounts of resin and hardener into the mixing container. The ratio may vary depending on the brand of resin you are using, so make sure to read the instructions carefully.
- Use a stir stick to thoroughly mix the resin and hardener together. Stir gently but thoroughly in a slow, circular motion, making sure to scrape the sides and bottom of the container.
- Continue to stir for the specified time indicated in the instructions. This process will ensure that the resin and hardener are properly combined, preventing any issues with curing later on.
Remember, it’s essential to follow the manufacturer’s instructions regarding the mixing ratios and curing time. Different resin brands may have slightly different requirements, so it’s important to read and understand the instructions specific to the product you are using.
Once the resin and hardener are fully mixed, move on to the next step: pouring the resin onto the coasters.
Step 3: Pouring the Resin
With your resin mixture ready, it’s time to pour it onto your prepared coasters. Follow these steps to ensure a smooth and even application:
- Place your resin coasters on a level surface, preferably on top of a drop cloth or newspaper to catch any drips.
- If desired, you can use masking tape to create a barrier around the edges of the coasters. This will help contain the resin and prevent it from overflowing.
- Slowly and carefully pour the mixed resin onto the center of each coaster. Start with a small amount and gradually add more if needed.
- Use a paintbrush or foam brush to spread the resin evenly across the surface of each coaster. Make sure to cover all corners and edges for a complete seal.
- If you’re creating layered designs or incorporating other materials, such as dried flowers or glitter, now is the time to do so. Simply place the desired elements on top of the wet resin and gently press them down.
Be mindful not to pour too much resin at once, as it could overflow and create a mess. It’s better to add resin in multiple thin layers, allowing each layer to cure properly before applying the next one.
Once you have poured and spread the resin on all of your coasters, you can move on to the next step: removing air bubbles.
Read more: How To Make Resin Car Coasters
Step 4: Removing Air Bubbles
After pouring the resin onto your coasters, it’s common for air bubbles to form. These bubbles can affect the overall appearance of your coasters if left unattended. Follow these steps to effectively remove air bubbles:
- Allow the resin to sit for a few minutes after pouring. This will give the air bubbles a chance to rise to the surface.
- With a heat gun or a kitchen torch, carefully pass the flame over the surface of the resin, holding it a few inches away. The heat will cause the air bubbles to pop and disappear.
- Alternatively, you can use a toothpick or a small wooden stick to gently tap the surface of the resin. This will also help release any trapped air bubbles.
- Continue to pass the heat gun or tap the resin until all visible air bubbles are eliminated.
Be cautious when using a heat gun or kitchen torch, as excessive heat or too close of a flame can damage the resin or create unwanted effects. It’s important to maintain a safe distance and move the heat source continuously to prevent overheating.
Once you’re satisfied with the removal of air bubbles, allow the resin to cure according to the instructions provided by the manufacturer. This usually takes a few hours, but it may vary depending on the type of resin used.
Now that the resin is curing, you can move on to the next step: sanding the coasters to achieve a smooth finish.
Make sure to work in a well-ventilated area and wear gloves to protect your skin. Use a heat gun or torch to remove any air bubbles from the resin before it sets. Allow the coasters to cure in a dust-free environment for at least 24 hours.
Step 5: Curing the Resin
After removing any air bubbles, it’s time to let the resin cure. Curing is the process in which the resin hardens and solidifies, providing a strong and durable finish. Follow these steps to ensure proper resin curing:
- Place the resin coasters in a dust-free and well-ventilated area. It’s important to protect them from any dust or particles that may settle on the surface.
- Allow the resin to cure for the recommended time specified by the manufacturer. This can typically range from 24 to 48 hours, depending on the brand and type of resin used.
- Avoid touching or moving the coasters during the curing process, as this can leave unwanted marks or disrupt the resin’s smooth finish.
- Keep the room temperature consistent and moderate to ensure proper curing. Extreme temperatures can hinder the curing process and affect the final outcome.
During the curing process, the resin will go through stages of becoming tacky and ultimately hardening. It’s essential to follow the recommended curing time to allow the resin to fully set and achieve optimal strength and clarity.
Once the resin has completely cured, you can proceed to the next step: sanding the coasters to refine the surface and remove any imperfections.
Step 6: Sanding the Coasters
After the resin has cured and hardened, it’s time to sand the coasters to achieve a smooth and flawless finish. Sanding helps to remove any imperfections, rough edges, or uneven surfaces. Follow these steps to properly sand your resin coasters:
- Prepare your workspace by laying down a drop cloth or newspaper to catch any dust or debris.
- Start with a low grit sandpaper, such as 120 or 150, to gently sand the surface of the coasters. Use a circular motion and apply light pressure to even out any bumps or rough areas.
- Continue sanding with progressively higher grit sandpaper, such as 220, 320, and 400. Each higher grit will help to refine the surface and remove scratches left by the previous grit.
- Pay extra attention to the edges of the coasters, as they may require more sanding to ensure smoothness.
- Periodically wipe the coasters with a clean, damp cloth to remove the sanding dust and assess the progress. This will also help you identify any areas that still require sanding.
- Once you are satisfied with the smoothness of the coasters, finish off the sanding process with a fine grit sandpaper, such as 600 or 800, for a final polish.
Remember to sand gently and evenly to avoid removing too much resin or creating uneven surfaces. Take your time and periodically check the coasters to ensure you’re achieving the desired smoothness.
After sanding, use a clean, lint-free cloth to remove any remaining dust from the surface of the coasters. Now, your coasters are ready for the next step: cleaning before sealing.
Step 7: Cleaning the Coasters
Before applying the sealant to your resin coasters, it’s crucial to clean them thoroughly. Cleaning helps remove any sanding dust, fingerprints, or other debris that may have accumulated on the surface. Follow these steps to ensure your coasters are clean and ready for the final sealing:
- Fill a bowl with warm water and add a few drops of mild dish soap. Stir the water gently to create a soapy solution.
- Take a clean, lint-free cloth and dip it into the soapy water. Wring out any excess liquid.
- Gently wipe down the surface of each coaster, making sure to remove any dust, fingerprints, or residue. Pay extra attention to the edges and corners.
- Rinse the coasters with clean water to remove any soap residue.
- Pat the coasters dry with a clean, lint-free cloth or allow them to air dry completely.
By properly cleaning the coasters, you ensure that the sealant will adhere well to the surface and provide a smooth and flawless finish. Additionally, cleaning the coasters helps to remove any oils or contaminants that could interfere with the sealing process.
Once the coasters are clean and dry, they are ready for the final step: applying the sealant to protect and enhance the appearance.
Read more: How To Make Flower Resin Coasters
Step 8: Applying the Sealant
The final step in sealing your resin coasters is to apply a sealant to provide protection and enhance their appearance. Follow these steps to properly apply the sealant:
- Choose a high-quality resin sealant specifically designed for sealing resin or epoxy surfaces. Make sure to read and follow the manufacturer’s instructions.
- Ensure that your workspace is well-ventilated and free of any dust or debris that could settle on the coasters.
- Put on your disposable gloves to protect your hands and prepare the sealant according to the instructions provided.
- Using a clean paintbrush or foam brush, apply a thin and even layer of sealant onto the entire surface of each coaster. Make sure to cover all sides, edges, and corners.
- Avoid over-applying the sealant to prevent drips or pooling. A thin and even layer is sufficient for effective sealing and protection.
- If desired, you can apply multiple coats of sealant, allowing each coat to dry between applications. This will provide additional protection and a more robust finish.
- Once the sealant is applied, allow the coasters to dry and cure completely according to the manufacturer’s instructions.
- Once dry, inspect the coasters for any imperfections or areas that may require touch-ups. You can lightly sand those areas and reapply the sealant if necessary.
Applying a sealant not only protects your resin coasters from scratches, moisture, and UV damage, but it also enhances their shine and color. It provides a durable and long-lasting finish that will keep your coasters looking their best for years to come.
Congratulations! You have now successfully sealed your resin coasters. Allow them to fully cure before using or gifting them, and enjoy the beauty and functionality they bring to your table settings.
Conclusion
Sealing resin coasters is an essential step in ensuring their longevity and maintaining their beauty. By following the step-by-step guide provided in this article, you can achieve professional-looking results and protect your coasters from everyday wear and tear. Here are the key takeaways:
- Prepare the resin coasters by cleaning them thoroughly, removing any dust, dirt, or residue.
- Mix the resin and hardener together according to the manufacturer’s instructions.
- Pour the resin onto the coasters, spreading it evenly and incorporating any additional design elements.
- Remove air bubbles using a heat gun, tapping method, or other techniques.
- Allow the resin to cure for the recommended time to ensure it hardens completely.
- Sand the coasters to achieve a smooth surface, gradually increasing the grit size for a polished finish.
- Clean the coasters to remove any sanding dust or debris before applying the sealant.
- Apply the sealant in thin and even coats, allowing each coat to dry before adding additional layers.
- Once the sealant is dry and cured, your resin coasters are ready to be used or gifted.
Remember to use high-quality resin and sealant products for the best results. Additionally, work in a well-ventilated area, wear disposable gloves, and protect your workspace from spills and drips.
Sealed resin coasters not only protect the underlying design but also add elegance and functionality to your table settings. Whether you’re using them at home or giving them as thoughtful gifts, these coasters are sure to impress.
Now that you have learned how to properly seal resin coasters, you can enjoy the satisfaction of creating beautiful, durable, and long-lasting pieces of tableware. So, go ahead and showcase your creativity with confidence!
Frequently Asked Questions about How To Seal Resin Coasters
Was this page helpful?
At Storables.com, we guarantee accurate and reliable information. Our content, validated by Expert Board Contributors, is crafted following stringent Editorial Policies. We're committed to providing you with well-researched, expert-backed insights for all your informational needs.
0 thoughts on “How To Seal Resin Coasters”