Home>diy>Building & Construction>How To Build A House Out Of A Metal Building
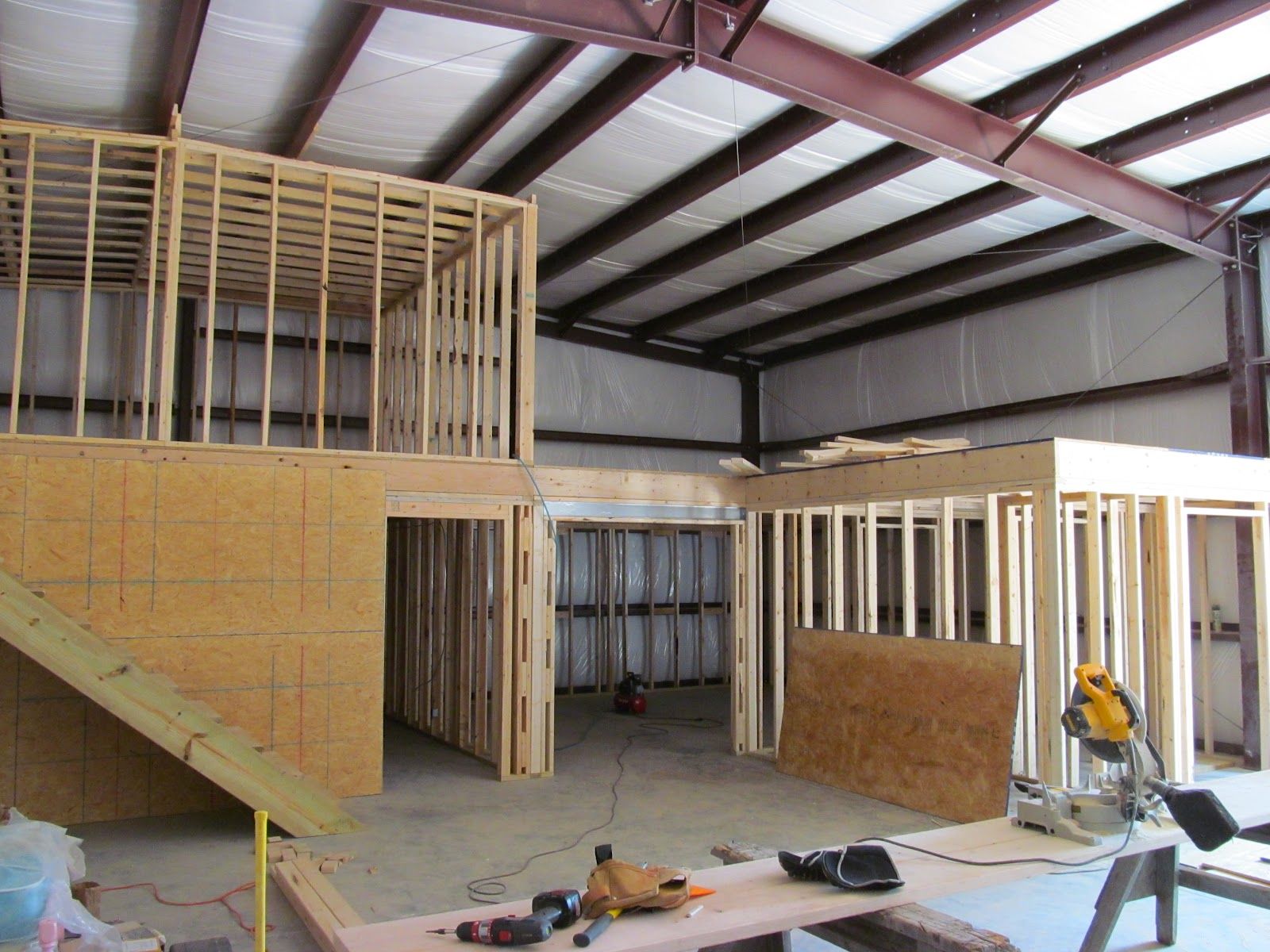
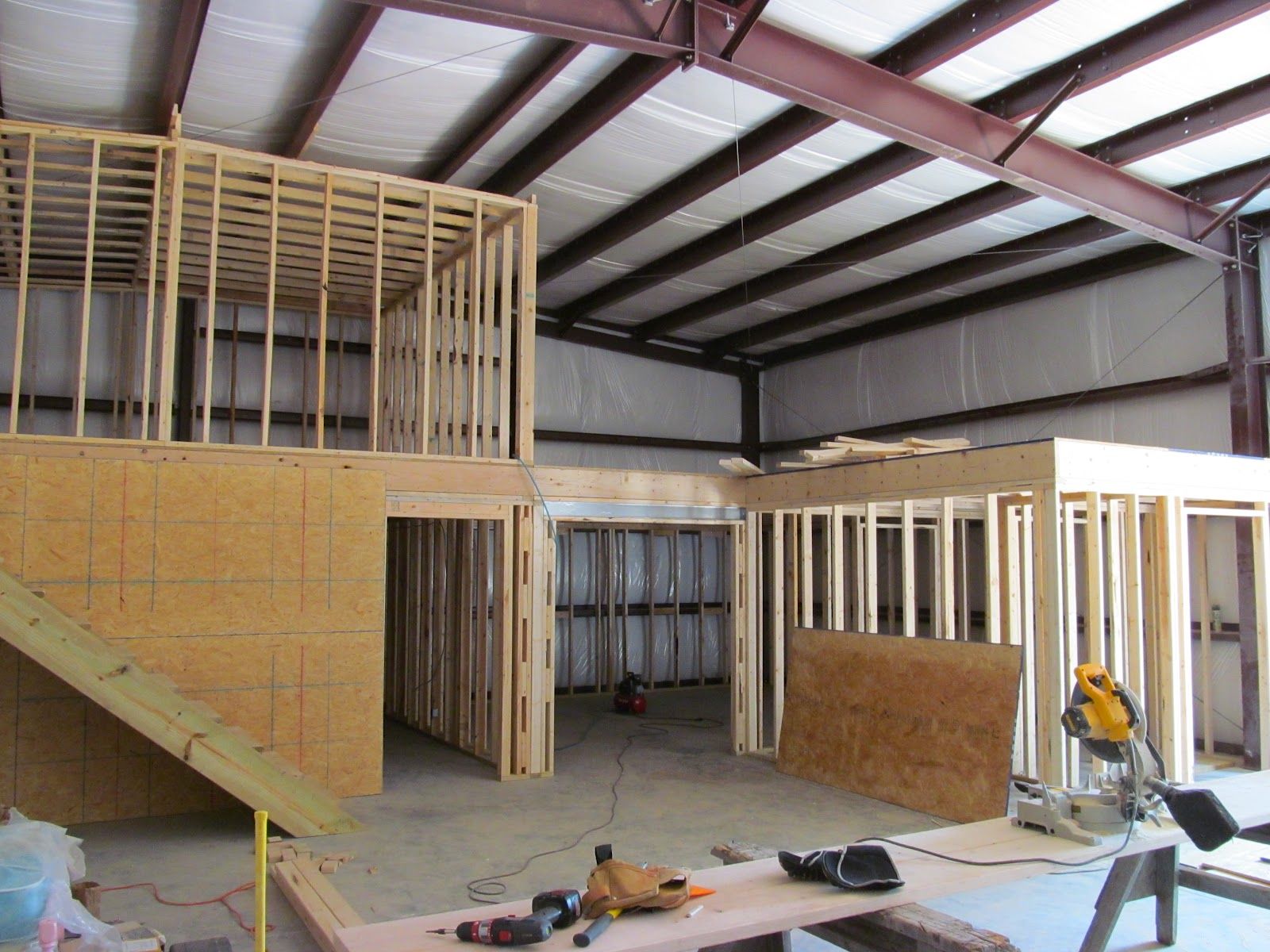
Building & Construction
How To Build A House Out Of A Metal Building
Modified: September 2, 2024
Learn how to construct a durable and cost-effective house by repurposing a metal building. Expert tips and step-by-step guidance for building-construction enthusiasts.
(Many of the links in this article redirect to a specific reviewed product. Your purchase of these products through affiliate links helps to generate commission for Storables.com, at no extra cost. Learn more)
Introduction
Building a house is an exciting venture, but the traditional methods of using wood or bricks may not always be the most practical or cost-effective option. Metal buildings have gained popularity in recent years as a viable alternative for constructing residential properties. Not only are they durable and versatile, but they also offer excellent energy efficiency and design options.
In this article, we will explore the process of building a house out of a metal building. From choosing the right metal building to adding the finishing touches, we will cover all the essential steps to ensure a successful and well-built home.
Before diving into the details, it’s important to understand that building a house out of a metal building requires careful planning, adherence to local building codes, and the assistance of professionals, such as architects and contractors. With the right team and knowledge, you can create a beautiful and structurally sound home that will stand the test of time.
Key Takeaways:
- Building a house out of a metal building requires careful planning, from choosing the right metal building to installing electrical and plumbing systems. Professional expertise is crucial for a successful and structurally sound home.
- The finishing touches, such as interior design, lighting, and landscaping, add personality and functionality to a house made from a metal building. Attention to detail and personal style transform it into a comfortable and inviting home.
Choosing the Right Metal Building
When it comes to choosing the right metal building for your house, there are several factors to consider. This includes the size, style, and design options available. Additionally, the building material, such as steel or aluminum, should be carefully selected to suit your specific needs.
First and foremost, determine the size of the metal building based on your desired living space. Consider the number of bedrooms, bathrooms, and common areas you require. It’s essential to account for future expansion or modifications as well.
Next, consider the style and design of the metal building. Metal buildings come in various styles, such as gable, gambrel, and monitor. Each style offers distinct aesthetic qualities and may affect the interior layout and overall appearance of your home. Consider your personal preferences and architectural compatibility with your surroundings.
In addition to size and style, the choice of material is crucial. Steel and aluminum are the most commonly used metals for building construction. Steel is known for its strength and durability and is ideal for areas prone to extreme weather conditions. Aluminum, on the other hand, is lightweight and resistant to rust, making it a popular choice for coastal regions.
It’s also important to consider the insulation options available for the metal building. Insulation is crucial for maintaining comfortable indoor temperatures and reducing energy consumption. Choose a metal building that offers insulation options suitable for your climate and energy efficiency requirements.
Lastly, consider the cost and warranty of the metal building. Compare prices from different manufacturers and suppliers to ensure you are getting the best value for your investment. Additionally, check the warranty terms and conditions to protect yourself against any potential issues or defects in the building.
Taking these factors into account will help you choose the right metal building that meets your specific requirements and ensures a stable and comfortable home.
Preparing the Foundation
The foundation is a critical component of any house, and when building a house out of a metal building, the foundation plays an equally important role. It provides stability and supports the weight of the structure, ensuring its long-term durability.
The first step in preparing the foundation is to obtain the necessary permits and consult with local building authorities. They will provide guidance on the specific requirements and regulations for your area.
Once you have the necessary permits, the next step is site preparation. Clear the construction area of any vegetation, debris, or obstructions. Ensure the site is level and compacted for a solid foundation.
Depending on the type of foundation you choose, you may need to excavate the site. Common types of foundations for metal buildings include slab-on-grade and pier foundations. A slab-on-grade foundation involves pouring a concrete pad directly on the ground, while a pier foundation involves concrete piers that support the structure. Consult with a structural engineer or contractor to determine the best foundation type for your specific needs.
If you opt for a slab-on-grade foundation, the next step is to lay a durable and moisture-resistant barrier. This barrier prevents moisture from seeping into the concrete, avoiding potential issues like mold or cracking. A layer of gravel is then added for proper drainage.
Once the barrier and gravel are in place, it’s time to pour the concrete. Work with a professional concrete contractor to ensure the proper thickness and reinforcement of the concrete slab. The contractor will take into consideration factors like soil conditions, climate, and the weight of the metal building to ensure a strong foundation.
If you choose a pier foundation, the piers are typically made of concrete or steel and should be spaced according to the recommendations of the structural engineer or building code. The piers should be set in place and leveled before proceeding with the construction.
Regardless of the foundation type, it is important to allow sufficient curing time for the concrete to achieve its maximum strength before continuing with the construction process.
Preparing the foundation properly is essential to ensure a stable and secure structure. Take the time and effort to follow the proper steps and consult with professionals as needed for a successful foundation installation.
Assembling the Metal Building
Once the foundation is prepared, it’s time to start assembling the metal building. This step involves erecting the metal panels, framing the structure, and securing it in place.
Start by laying out the metal building components according to the manufacturer’s instructions. Be sure to organize the panels, beams, and other parts in a systematic manner for easy access during the assembly process.
Begin by attaching the metal panels to the foundation. This typically involves using anchor bolts or screws to secure the panels to the foundation or through the bottom base rails. Follow the manufacturer’s guidelines for proper installation, ensuring that the panels are properly aligned and securely fastened.
As you go along, connect the metal panels to create the walls of the structure. This may involve sliding panels together, interlocking them, or using fasteners to join them securely. Pay attention to any specific recommendations or techniques provided by the manufacturer to ensure a strong and watertight seal.
Once the walls are in place, it’s time to install the roof of the metal building. This step typically involves attaching roof beams, purlins, and roofing panels. Follow the manufacturer’s instructions for proper alignment and spacing of the roof components, ensuring stability and durability.
During the assembly process, it’s important to have proper safety measures in place. This includes using appropriate safety equipment, such as harnesses and helmets, as well as following proper lifting and handling techniques to prevent accidents or injuries.
As you assemble the metal building, periodically check for any adjustments or modifications that may be required. Sometimes, minor alterations may be needed to ensure a precise fit or address any unforeseen issues that arise during the construction process.
Once the metal building is fully assembled, take the time to inspect the structure thoroughly. Check for any loose or improperly secured panels, beams, or connections. Ensure that all components are aligned correctly, and there are no visible defects that may compromise the integrity of the structure.
Assembling a metal building requires precision, attention to detail, and adherence to safety protocols. If you are not confident in your abilities, it’s highly recommended to seek professional assistance to ensure a successful and safe assembly process.
Roof Installation
The roof is a critical component of any house, and when it comes to a metal building, proper roof installation is crucial for maintaining structural integrity and protecting the interior from the elements. Here are the steps to follow when installing the roof for your metal building.
Before starting the roof installation, ensure that the metal building’s walls are fully assembled and secure. This will provide a stable and supportive structure for the roof installation process.
First, determine the roofing material you will use. Metal buildings offer a variety of options, including metal panels, shingles, or even a combination of materials. Consider factors such as durability, weather resistance, and aesthetic appeal when selecting the roofing material.
Next, prepare the roof surface by ensuring it is clean, free of debris, and properly aligned. This may involve sweeping or pressure washing the surface, removing any obstacles that may obstruct the roof installation process.
If you are using metal panels as the roofing material, start by laying the panels across the roof framework. Begin at one end of the roof and work your way across, overlapping each panel according to the manufacturer’s instructions. Use screws or fasteners to secure the panels to the framework, maintaining a consistent spacing between each panel.
If your roof requires flashing or trim, ensure that it is properly installed around openings such as vents, chimneys, or skylights. This helps to prevent water or debris from infiltrating the interior and ensures proper waterproofing.
For shingle or tile roofs, follow the specific manufacturer’s instructions for installation. Typically, this involves starting at the bottom edge of the roof and working your way up, nailing or fastening the shingles or tiles in place. Take care to align them properly and use appropriate flashing or underlayment to ensure a watertight seal.
During the roof installation process, it is important to pay attention to proper sealing and weatherproofing. This may involve applying sealant or caulking around edges, joints, and seams to prevent water infiltration. Consult with the manufacturer or a roofing professional for recommendations on the best sealant to use for your specific roofing material.
Once the roof is fully installed, take the time to inspect it for any loose or improperly secured components. Check for any visible gaps, leaks, or potential areas of concern. Address any issues promptly to ensure the roof’s longevity and functionality.
Proper roof installation is crucial for a well-built and resilient metal building. If you are unsure about the process or lack experience, it is recommended to consult with a roofing professional to ensure the job is done correctly and to maintain the structural integrity of your home.
When building a house out of a metal building, make sure to properly insulate the structure to regulate temperature and reduce noise. This will make the house more comfortable and energy-efficient.
Read more: How To Build Metal Stairs
Insulating the Metal Building
Insulating a metal building is essential for creating a comfortable and energy-efficient living space. Metal buildings have excellent structural properties but can be prone to extreme temperature fluctuations if not properly insulated. Here are the steps to follow when insulating your metal building.
The first step in insulating a metal building is to determine the insulation material that best suits your needs. Common options include fiberglass batts, rigid foam boards, or spray foam insulation. Consider factors such as R-value (insulation effectiveness), moisture resistance, and cost when selecting the insulation material.
Before installing the insulation, it is important to ensure that the metal building is properly sealed. Inspect the walls and roof for any gaps, cracks, or openings that may allow air or moisture infiltration. Seal these areas with caulking or weatherstripping to create a tight and secure envelope.
If you are using fiberglass batts for insulation, start by measuring and cutting the batts to fit the wall cavities. Carefully insert the batts between the metal framing, ensuring a snug fit. Use staples or insulation hangers to secure the batts in place, taking care not to compress them too tightly, as it may reduce their insulation effectiveness.
If you have opted for rigid foam board insulation, measure and cut the boards to fit the wall cavities. Attach them to the metal framing using adhesive or mechanical fasteners, ensuring a secure and tight fit. Pay attention to any joints or seams, sealing them with tape or sealant to prevent air leakage.
Spray foam insulation is another option that provides excellent coverage and insulation performance. This insulation is applied as a liquid foam that expands to fill the wall cavities. It is typically installed by professionals using specialized equipment, ensuring proper application and coverage.
When insulating the roof of the metal building, the process is similar to insulating the walls. Install the chosen insulation material on the ceiling or between the roof framing, following the manufacturer’s instructions and guidelines for proper installation.
During the insulation installation, pay attention to safety precautions. Wear appropriate protective gear, such as gloves, goggles, and a mask, to prevent exposure to insulation materials. Follow the manufacturer’s guidelines for handling and installing the insulation safely.
Proper insulation not only provides comfort but also contributes to energy efficiency and lower utility costs. Insulating a metal building helps regulate indoor temperatures, reducing the need for excessive heating or cooling. This is especially important in areas with extreme weather conditions.
By following these steps and choosing the right insulation material, you can create a well-insulated metal building that offers year-round comfort and energy savings.
Framing Interior Walls
After the insulation is installed, the next step in building a house out of a metal building is framing the interior walls. Framing the interior walls provides structure and defines the layout of the rooms and spaces within your home. Here are the steps to follow when framing the interior walls of a metal building.
Start by drawing out a detailed floor plan for your house, indicating the locations and dimensions of each room. This will serve as a guide during the framing process.
Measure and mark the locations where the interior walls will be installed on the metal building’s floor and ceiling. Use a chalk line or laser level to ensure accurate placement.
Next, determine the stud spacing for the interior walls. Standard practice is to space the studs 16 inches apart, but this may vary depending on building codes and specifications.
Cut the metal or wood studs to the appropriate length, considering the height of the walls and any openings for doors or windows.
Start framing the interior walls by installing the sole plates, which are horizontal boards that run along the base of the walls. Secure the sole plates to the floor using concrete anchors or screws, ensuring they are level and aligned.
Using a level, plumb the first stud into position, attaching it to the sole plate and the ceiling or roof beams with screws or fasteners. Continue installing the remaining studs, making sure they are plumb and properly aligned.
For openings such as doorways or windows, install additional framing components to support and stabilize them. Follow the manufacturer’s instructions or consult with a professional to ensure proper installation and structural integrity.
Once all the studs are in place, install the top plates by attaching them to the ceiling or roof beams. This provides additional stability and rigidity to the walls.
When framing interior walls, it is important to consider electrical and plumbing requirements. Consult with an electrician and plumber to determine the appropriate locations for outlets, switches, plumbing lines, and ventilation.
Ensure that all electrical and plumbing components are installed according to local building codes and regulations. This may involve running wires, pipes, and ducts through the wall cavities before installing drywall or other wall finishes.
Once the interior walls are framed and all necessary electrical and plumbing work is completed, the next step is to install the wall finishes, such as drywall or paneling. This will create a finished and seamless appearance for your interior walls.
Framing interior walls is an important step in the construction of a house made from a metal building. Proper framing ensures stability, defines room layouts, and allows for the installation of electrical and plumbing components. Take the time to carefully plan and execute the framing process to create a solid and well-designed home.
Installing Doors and Windows
Installing doors and windows in a metal building is a crucial step in turning it into a functional and livable home. Proper installation of doors and windows ensures functionality, security, and proper ventilation. Here are the steps to follow when installing doors and windows in your metal building.
Start by measuring and marking the locations where the doors and windows will be installed. Consider factors such as room layout, natural light, and airflow when determining the placement.
Next, prepare the openings for the doors and windows. If the metal building does not already have pre-cut openings, you will need to measure and carefully cut the openings following the manufacturer’s guidelines. Take proper safety precautions, such as wearing protective eyewear and gloves, and using appropriate tools for cutting metal.
After the openings are prepared, install the door or window frame. This involves attaching the frame to the metal building using screws or fasteners. Ensure the frame is level and plumb, using a level or plumb line to make accurate adjustments as needed.
Once the frame is securely in place, install the door or window unit into the frame. This may involve inserting the door or window into the frame and attaching it using hinges, screws, or other specified hardware. Follow the manufacturer’s instructions for proper installation, ensuring a snug fit and smooth operation.
Properly seal the gaps around the door or window frame to prevent air or water infiltration. Use weatherstripping or sealant to create a tight seal, ensuring energy efficiency and protection from the elements.
Depending on the design and functionality of the doors and windows, additional components such as handles, locks, and hardware may need to be installed. Follow the manufacturer’s instructions and guidelines for installing these components correctly.
During the installation process, it is important to pay attention to safety measures. Work with caution to prevent injury and damage to the doors, windows, or the metal building itself. If you are not confident in your abilities, it is recommended to seek professional assistance for the installation of doors and windows.
Once the doors and windows are installed, take the time to inspect them for proper operation and functionality. Ensure that they open and close smoothly, latch securely, and provide adequate sealing against drafts and water infiltration.
Installing doors and windows in a metal building is an important step in creating a comfortable and functional living space. By following these steps and taking proper precautions, you can ensure a proper installation and enjoy the benefits of natural light, ventilation, and secure access to your home.
Electrical and Plumbing
The installation of electrical and plumbing systems is a critical part of building a house out of a metal building. Proper electrical and plumbing setup ensures functionality, safety, and convenience within your home. Here are the steps to follow when installing electrical and plumbing systems in your metal building.
Electrical Installation:
- Hire a licensed electrician to handle the electrical installation. Electrical work should always be done by a professional to ensure compliance with local building codes and to guarantee safety.
- Create an electrical plan that outlines the placement of switches, outlets, light fixtures, and other electrical components. Consider factors such as room layouts, functional needs, and lighting requirements.
Plumbing Installation:
- Hire a licensed plumber to handle the plumbing installation. Plumbing work requires expertise to ensure proper pipe sizing, connections, and adherence to building codes.
When it comes to electrical and plumbing installations, it is crucial to consult with professionals who are knowledgeable in their respective fields. Their expertise will guarantee that the work is done safely, accurately, and in compliance with all regulations. Undertaking these installations without the appropriate expertise can lead to safety hazards and may not meet the necessary standards.
By following these steps and enlisting the help of licensed professionals, you can ensure that your electrical and plumbing systems are properly installed, providing a safe and functional living environment within your metal building.
Read more: How To Build A Metal Carport
Finishing Touches
Once the major construction and installations are complete, it’s time to focus on the finishing touches of your house made from a metal building. These final touches add personality, style, and functionality to your home. Here are some key aspects to consider during this stage:
Interior Design: Transform the interior space with the power of design. Choose paint colors, wallpapers, or other wall finishes that align with your personal style and aesthetic preferences. Select flooring options such as hardwood, laminate, or ceramic tiles to enhance the visual appeal of each room. Consider adding crown molding or trim for a polished and sophisticated look.
Lighting: Illuminate your living space with carefully chosen lighting fixtures. Opt for a combination of ambient, task, and accent lighting to create the desired ambiance and functionality for each room. Consider installing energy-efficient LED lights to reduce energy consumption and save on utility bills.
Cabinetry and Storage: Install cabinets, shelves, and storage units to maximize space and keep your home organized. Custom-built cabinetry or modular storage systems can provide both functionality and aesthetic appeal, catering to your specific needs and design preferences.
Plumbing Fixtures: Choose stylish and functional plumbing fixtures such as faucets, showerheads, and sinks that reflect your personal style and complement the overall design of your home. Opt for water-saving fixtures to promote sustainability and reduce water consumption.
Electrical Fixtures: Select lighting fixtures, switches, and outlets that enhance the style and functionality of each room. Consider installing smart home automation systems that allow you to control lighting, temperature, and other electrical devices with ease.
Landscaping: Pay attention to the exterior of your home by creating an inviting and well-maintained landscape. Plant trees, shrubs, and flowers to enhance curb appeal and create a welcoming environment. Install pathways, patios, or outdoor seating areas to maximize the use of outdoor spaces.
Finishing Materials: Choose the appropriate finishes for the exterior of your metal building to protect it from weather elements and enhance its appearance. Consider options such as stucco, siding, or brick veneer to create a blended and aesthetically pleasing exterior.
Personal Touches: Add your personal touch to your home by displaying artwork, photographs, and other decorative elements that hold sentimental value. Use accessories such as rugs, curtains, and throw pillows to add texture and color to your living spaces.
Remember that the finishing touches of your home should align with your personal style and preferences. Take your time in choosing the right materials, fixtures, and design elements to ensure a cohesive and visually appealing final result.
By focusing on these finishing touches, your house made from a metal building will be transformed into a comfortable and inviting home, reflecting your unique taste and lifestyle.
Frequently Asked Questions about How To Build A House Out Of A Metal Building
Was this page helpful?
At Storables.com, we guarantee accurate and reliable information. Our content, validated by Expert Board Contributors, is crafted following stringent Editorial Policies. We're committed to providing you with well-researched, expert-backed insights for all your informational needs.
0 thoughts on “How To Build A House Out Of A Metal Building”