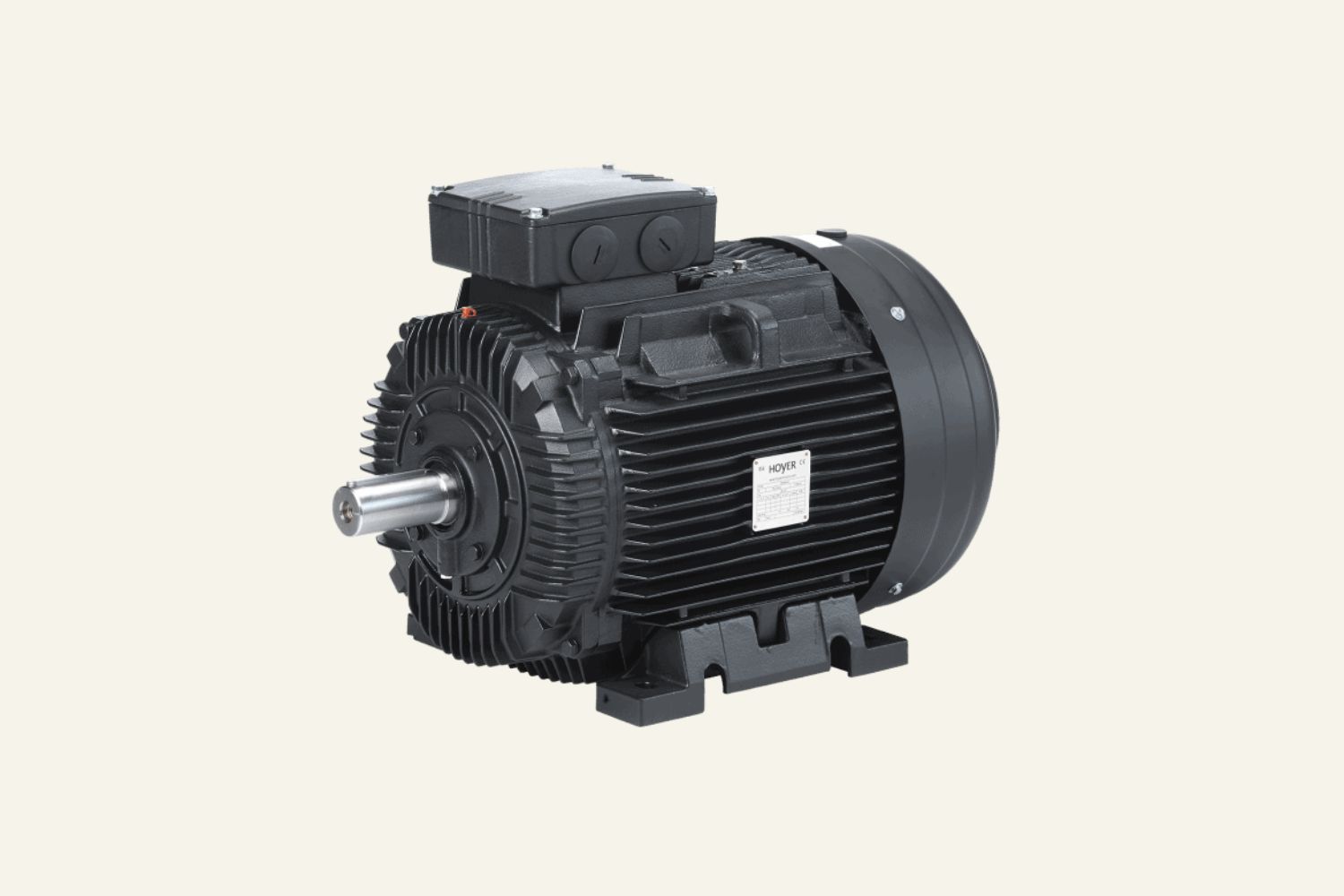
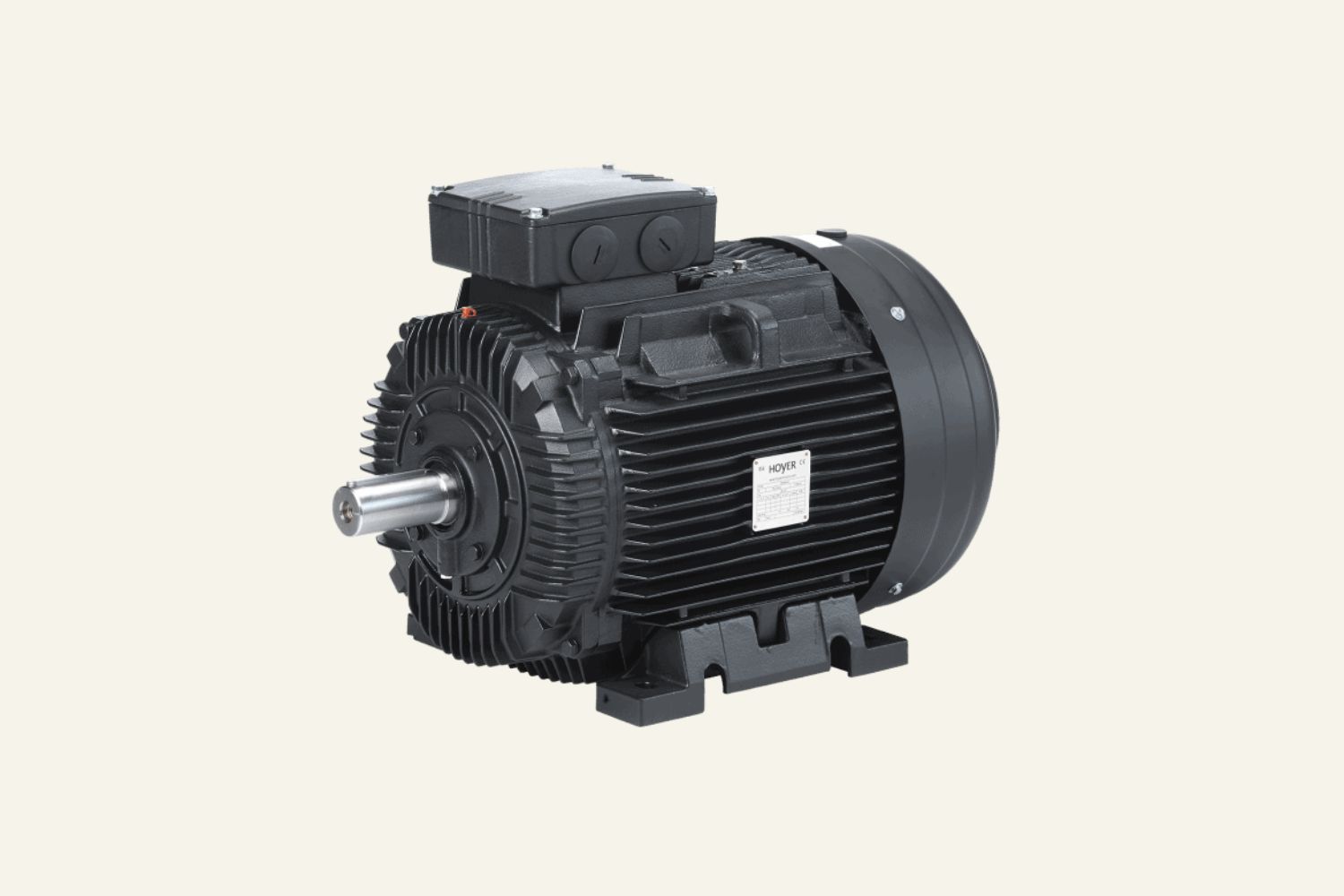
Articles
How To Cool An Electric Motor
Modified: August 27, 2024
Learn effective techniques to cool an electric motor with our informative articles. Find valuable tips and insights to ensure optimal performance and prevent overheating.
(Many of the links in this article redirect to a specific reviewed product. Your purchase of these products through affiliate links helps to generate commission for Storables.com, at no extra cost. Learn more)
Introduction
An electric motor is a crucial component in various industries and applications, powering everything from HVAC systems to industrial machinery. As the demand for higher performance and efficiency in electric motors increases, so does the need for effective cooling methods. Without proper cooling, electric motors can quickly overheat, leading to reduced performance, increased wear and tear, and even premature motor failure.
In this article, we will explore the importance of cooling an electric motor, the factors that affect motor temperature, and the different cooling methods available. We will also discuss common cooling challenges and provide solutions for optimal motor cooling.
Properly cooling an electric motor is essential for maintaining optimum operating conditions and extending its lifespan. By understanding the different cooling methods and selecting the most suitable one for your motor, you can enhance performance, prevent overheating, and ensure reliable operation.
Key Takeaways:
- Proper cooling of electric motors is crucial for maintaining efficiency, reliability, and longevity. Understanding factors like power rating, operating environment, and cooling requirements is essential for selecting the right cooling method.
- Common cooling challenges, such as insufficient cooling capacity and thermal hotspots, can be addressed through regular maintenance, cleaning, and optimization of the cooling system. Properly addressing these challenges ensures effective heat dissipation and reliable motor operation.
Read more: How To Lubricate Fan Motor
Importance of Cooling an Electric Motor
Cooling an electric motor is of utmost importance as it plays a crucial role in ensuring the motor’s efficiency, reliability, and overall performance. The primary function of cooling is to dissipate the heat generated during motor operation and to maintain the motor’s temperature within a safe operating range.
When an electric motor operates, it generates heat due to electrical and mechanical losses. If this heat is not properly controlled and dissipated, it can lead to various issues:
- Reduced Efficiency: Excessive heat buildup in an electric motor can negatively impact its efficiency and performance. Heat causes increased resistance in the motor windings, leading to higher power losses and decreased efficiency.
- Accelerated Wear and Tear: High temperatures can accelerate the wear and tear of motor components, such as the insulation on the winding wires. This can result in increased maintenance requirements and ultimately, motor failure.
- Shortened Motor Lifespan: Continuous exposure to elevated temperatures can significantly reduce the lifespan of an electric motor. Overheating can cause premature aging and degradation of insulation materials, leading to insulation breakdown and motor failure.
- Potential Safety Hazards: In extreme cases, excessive heat can pose safety risks, including the possibility of fire or electrical hazards. It is essential to prevent the motor from reaching critical temperatures to ensure the safety of personnel and equipment.
To mitigate these issues and ensure optimal motor performance, proper cooling measures are necessary. Effective cooling helps maintain the motor’s temperature within a safe range, enhancing its efficiency, reliability, and longevity.
Furthermore, cooling allows for the operation of electric motors at higher power levels without compromising their performance. By actively dissipating heat, cooling methods enable motors to handle increased loads and operate in demanding environments without the risk of overheating.
In the following sections, we will explore the factors that influence motor temperature and the different cooling methods available to effectively manage the heat generated by electric motors.
Factors Affecting Motor Temperature
Several factors contribute to the temperature of an electric motor during operation. Understanding these factors is crucial in implementing the appropriate cooling measures. Here are the key factors that influence motor temperature:
- Load: The load on the motor, or the amount of work it is required to perform, has a significant impact on motor temperature. Higher loads result in increased electrical and mechanical losses, generating more heat within the motor.
- Ambient Temperature: The temperature of the surrounding environment affects the motor’s ability to dissipate heat. If the ambient temperature is high, it becomes more challenging for the motor’s cooling system to maintain optimal operating temperatures.
- Enclosure Type: The design and construction of the motor’s enclosure also play a role in its ability to dissipate heat. Open enclosures allow for better airflow, while closed enclosures can trap heat and require more effective cooling mechanisms.
- Duty Cycle: The duty cycle refers to the operating pattern of the motor, including the duration and frequency of operation. Motors operating continuously or with a high duty cycle generate more heat and may require more robust cooling solutions.
- Insulation Condition: The condition of the motor’s insulation affects its ability to withstand heat. Deteriorated or damaged insulation can lead to increased heat generation and potential insulation breakdown.
- Motor Speed: Higher motor speeds result in increased friction and electrical losses, leading to elevated temperatures. Motors operating at high speeds may require more efficient cooling methods to manage the generated heat.
- Voltage and Current: Higher voltages and currents can contribute to increased heat generation within the motor. Motors operating at higher power levels may require additional cooling measures to prevent overheating.
- Mechanical Design: The mechanical design of the motor, including factors such as the size, shape, and materials used, can influence its ability to dissipate heat. Motors with better heat transfer properties and efficient cooling mechanisms generally operate at lower temperatures.
It is important to consider these factors when selecting a cooling method for your electric motor. By understanding the specific conditions and requirements of your motor, you can implement the most effective cooling solution to maintain optimal operating temperatures and enhance motor performance.
Types of Electric Motor Cooling Methods
There are several cooling methods available to effectively manage the heat generated by electric motors. The choice of cooling method depends on various factors, including the motor’s design, application, and operating conditions. Here are the most common types of electric motor cooling methods:
- Air Cooling: Air cooling is the most basic and widely used method for cooling electric motors. It relies on the circulation of ambient air around the motor to dissipate heat. Air cooling can be achieved through natural convection, where the heat rises and is replaced by cooler air, or forced convection, where fans or blowers are used to enhance airflow and improve cooling efficiency. Air cooling methods are relatively simple and cost-effective but may have limitations in high-temperature or confined environments.
- Liquid Cooling: Liquid cooling involves circulating a coolant, such as water or a specialized cooling fluid, through the motor to absorb and remove heat. This method provides better heat transfer capabilities compared to air cooling and is often used in high-performance motors or applications that require precise temperature control. Liquid cooling can be implemented through various techniques, including direct liquid cooling, where coolant flows directly through internal channels, or indirect liquid cooling, where the coolant transfers heat to an external cooling system.
- Forced Cooling: Forced cooling methods involve the use of external mechanisms, such as fans, blowers, or pumps, to actively introduce airflow or circulate coolant through the motor. These methods enhance heat transfer and cooling efficiency, making them ideal for motors operating in demanding conditions or enclosed environments with limited natural airflow. Forced cooling can be combined with air or liquid cooling techniques to achieve optimal results.
- Passive Cooling: Passive cooling methods rely on the natural flow of heat through conduction, convection, and radiation without the use of external cooling mechanisms. Examples of passive cooling techniques include heat sinks, which provide increased surface area for heat dissipation, and thermal insulation, which helps prevent heat transfer to sensitive components. Passive cooling methods can be effective in smaller motors or applications where power levels and operating temperatures are relatively low.
Each cooling method has its advantages and considerations, and the choice depends on factors such as the motor’s power rating, operating environment, reliability requirements, and cost. It is essential to carefully evaluate these factors and consult with experts to select the most suitable cooling method for your specific motor and application.
Air Cooling
Air cooling is one of the most common and straightforward methods used to cool electric motors. It relies on the natural circulation of ambient air to dissipate heat generated during motor operation. This method is cost-effective and relatively easy to implement, making it a popular choice for a wide range of applications.
In air-cooled electric motors, heat is primarily dissipated through convection. As the motor operates, heat is generated within the windings, core, and other components. The heated air rises, creating a natural flow that allows cooler air to replace it, resulting in heat transfer and cooling.
There are two main types of air cooling methods:
- Natural Convection: Also known as free convection, this method relies on the principle that hot air rises and cooler air sinks. The natural convection process allows heat to dissipate as the hot air moves away from the motor’s critical components. This method is commonly used in open-frame motors or applications where the airflow is not restricted.
- Forced Convection: Forced convection involves the use of external fans or blowers to enhance the airflow around the motor. These fans or blowers create a forced draft, increasing the rate of heat transfer and improving cooling efficiency. Forced convection is beneficial for enclosed or restricted environments where natural convection may not be sufficient to dissipate heat effectively.
When implementing air-cooling methods, there are a few factors to consider:
- Ambient Temperature: The ambient temperature affects the cooling capacity of air cooling methods. Higher ambient temperatures can reduce the ability of air cooling to dissipate heat effectively.
- Enclosure Design: The design of the motor’s enclosure can impact the airflow and heat dissipation. Open-frame designs provide better airflow, while closed enclosures may restrict natural convection and require forced convection methods.
- Motor Placement: The installation location of the motor can also affect its cooling efficiency. Ensuring sufficient clearance around the motor and avoiding areas with restricted airflow can optimize air cooling performance.
- Circulation and Ventilation: Proper circulation of air within the operating environment and good ventilation can help enhance air cooling effectiveness. This can be achieved through strategic placement of fans or creating airflow paths to maximize heat dissipation.
Air cooling is a cost-effective cooling method suitable for various applications where moderate operating temperatures can be maintained. However, it may have limitations in high-temperature environments or applications that demand precise temperature control. In such cases, alternative cooling methods such as liquid or forced cooling may be more appropriate.
When selecting the cooling method for your electric motor, it is essential to consider factors such as the motor’s power rating, operating environment, and cooling requirements to ensure optimal cooling performance and prolonged motor lifespan.
Read more: How To Test Condenser Fan Motor
Liquid Cooling
Liquid cooling is a highly effective method used to cool electric motors, particularly in applications where precise temperature control and higher cooling capabilities are required. This method involves circulating a liquid coolant, such as water or a specialized cooling fluid, through the motor to absorb and dissipate heat.
There are two main types of liquid cooling methods used for electric motors:
- Direct Liquid Cooling: In direct liquid cooling, the coolant flows directly through internal channels or passages within the motor. The coolant absorbs heat as it passes through these channels, effectively removing heat from critical components. Direct liquid cooling provides excellent cooling efficiency and enables precise temperature control. This method is commonly used in high-performance motors or applications that require stable and low operating temperatures.
- Indirect Liquid Cooling: Indirect liquid cooling involves the use of a cooling system external to the motor to remove heat. The coolant does not directly contact the motor’s internal components but transfers heat to the external cooling system through heat exchangers. This method is often used when direct contact between the coolant and motor is not desired, such as in applications with strict environmental or safety requirements.
Liquid cooling offers several advantages over air cooling methods:
- Higher Cooling Capacity: Liquid cooling has superior heat transfer capabilities compared to air cooling, enabling more efficient heat dissipation. This allows for better temperature control and the ability to handle higher power densities.
- Precise Temperature Control: Liquid cooling allows for precise temperature control, crucial in applications where maintaining consistent and stable operating temperatures is essential for optimal performance and reliability.
- Reduced Acoustic Noise: Liquid cooling can help reduce the acoustic noise generated by the motor, making it suitable for noise-sensitive applications.
- Compact Design: Liquid cooling methods can be designed to be more compact and space-efficient compared to air cooling, making it advantageous in applications with limited available space.
- Flexibility: Liquid cooling systems can be customized and tailored to specific motor designs and application requirements, allowing for a high degree of flexibility.
However, liquid cooling also has some considerations:
- Complexity: Liquid cooling systems can be more complex to design, implement, and maintain compared to air cooling. They require appropriate plumbing, pumps, and control systems to ensure proper circulation and cooling efficiency.
- Coolant Compatibility: The selection of the appropriate coolant and its compatibility with motor components is crucial to prevent corrosion, contamination, or damage to the system.
- Maintenance: Regular maintenance and inspection of the cooling system are necessary to prevent issues such as leaks or blockages. Proper filtration and treatment of the coolant may also be required.
Liquid cooling is particularly beneficial in high-power electric motors or applications where maintaining stable and low operating temperatures is critical. By efficiently dissipating heat, liquid cooling ensures optimal motor performance, longevity, and reliability.
Regularly clean the motor’s cooling fan and ensure that the ventilation openings are not blocked. This will help to maintain proper airflow and prevent the motor from overheating.
Forced Cooling
Forced cooling is a cooling method used to enhance the airflow or circulation of a cooling medium around the motor. It involves the use of external mechanisms, such as fans, blowers, or pumps, to actively introduce airflow or circulate a coolant through the motor, improving heat transfer and cooling efficiency.
Forced cooling methods are particularly beneficial in situations where natural convection or passive cooling may be insufficient, such as in enclosed environments or applications with high heat generation. These methods provide a controlled and directed flow of air or coolant, ensuring effective heat dissipation from critical motor components.
There are two common types of forced cooling:
- Forced Air Cooling: Forced air cooling involves the use of fans or blowers to introduce airflow and increase the convective heat transfer around the motor. The fans or blowers are strategically placed to direct the airflow towards the hotspots or areas where heat generation is high. The forced airflow helps remove heat more efficiently, preventing the motor from overheating. Forced air cooling is often utilized in enclosed environments or applications where natural convection may be limited.
- Forced Liquid Cooling: Forced liquid cooling utilizes pumps or other mechanisms to actively circulate a liquid coolant through the motor. The coolant absorbs heat from the motor’s internal components and transfers it to an external cooling system or heat exchanger. The forced circulation ensures a constant supply of cooler coolant to remove heat more effectively. Forced liquid cooling offers higher cooling capacity and precision temperature control compared to forced air cooling and is commonly used in high-power motors or applications with stringent cooling requirements.
Forced cooling methods offer several advantages:
- Improved Heat Dissipation: Forced cooling enhances heat transfer and dissipates heat more efficiently, allowing the motor to operate at lower temperatures and prevent overheating.
- Enhanced Thermal Management: By actively introducing airflow or circulating coolant, forced cooling allows for better thermal management, ensuring consistent and stable operating temperatures.
- Flexibility and Adaptability: Forced cooling methods can be customized and adjusted to suit specific cooling requirements and operating conditions. The airflow or circulation can be directed to specific areas or components, optimizing cooling efficiency.
- Compensation for Enclosed Environments: Forced cooling is particularly advantageous in enclosed environments or applications where natural convection is limited, providing the necessary airflow or coolant circulation to maintain efficient heat dissipation.
However, there are a few considerations when implementing forced cooling methods:
- Power Consumption: Forced cooling methods, especially those using fans or blowers, require electrical energy to operate. This extra power consumption should be considered in the overall energy efficiency of the system.
- Noise Generation: Fans, blowers, or pumps used in forced cooling can generate noise. It is important to consider noise levels, especially in applications where noise reduction is a requirement.
- Maintenance: Forced cooling systems require regular maintenance to ensure proper function and performance. This includes inspecting and cleaning fans or blowers, checking for blockages in cooling channels, and monitoring coolant levels and quality in forced liquid cooling systems.
Forced cooling methods play an essential role in applications that demand efficient heat dissipation and temperature control. By actively introducing airflow or circulating coolant, forced cooling ensures optimal motor performance, prolongs motor life, and prevents overheating-related issues.
Passive Cooling
Passive cooling is a method of cooling electric motors that relies on natural heat transfer processes without the use of external mechanisms. It involves the design and implementation of heat dissipation techniques to effectively manage the heat generated during motor operation.
Passive cooling methods aim to promote heat dissipation through conduction, convection, and radiation. These methods are typically used in smaller motors or applications where power levels and operating temperatures are relatively low.
Here are some common passive cooling techniques:
- Heat Sinks: Heat sinks are widely used in passive cooling to increase the surface area available for heat dissipation. These metal structures are designed to absorb heat from the motor and transfer it to the surrounding air through convection. Heat sinks are often finned to enhance the heat transfer process and maximize cooling efficiency.
- Thermal Insulation: Thermal insulation is utilized to prevent heat transfer from the motor to sensitive components or the surrounding environment. By using materials with low thermal conductivity, such as insulation pads or coatings, the transmission of heat is minimized, keeping the motor and nearby components at lower temperatures.
- Natural Convection: Natural convection, as mentioned earlier, relies on the principle that hot air rises and cooler air sinks. By allowing heated air to escape and drawing in cooler air, natural convection promotes heat dissipation without the need for external fans or blowers. It is commonly used in open-frame motors or applications where the airflow is not restricted.
- Enclosure Ventilation: Proper ventilation of the motor’s enclosure is crucial for passive cooling. Ventilation openings or vents allow for the natural exchange of air, promoting heat dissipation. These openings should be strategically located to facilitate the flow of cooler air into the enclosure and the expulsion of hot air.
Passive cooling has several advantages:
- Simplicity and Reliability: Passive cooling methods are typically simple in design, requiring minimal or no additional components. They are reliable and have fewer points of failure compared to active cooling methods.
- Low Energy Consumption: Passive cooling does not require the use of external fans, blowers, or pumps, resulting in lower energy consumption and operating costs.
- Noise Reduction: Since passive cooling does not involve mechanical components, it generally produces less noise compared to active cooling methods, making it suitable for noise-sensitive applications.
- Cost-Effectiveness: Passive cooling techniques are often more cost-effective to implement and maintain, as they do not require complex systems or regular electrical power.
However, passive cooling does have its limitations:
- Lower Cooling Capacity: Passive cooling methods may not provide the same cooling capacity as active cooling methods. They are more suitable for applications with lower heat generation or where precise temperature control is not critical.
- Constraints in High-Temperature Environments: Passive cooling may be limited in high-temperature environments, as it relies on natural heat transfer mechanisms. In such cases, active cooling methods may be required to manage the increased heat generation.
- Size and Space Considerations: Passive cooling methods can occupy more space due to the use of heat sinks or other cooling elements. It is essential to consider space constraints when incorporating passive cooling techniques into motor designs.
Passive cooling methods, when appropriately designed and implemented, can provide effective heat dissipation for smaller motors or applications with lower heat generation. By leveraging natural heat transfer processes, passive cooling contributes to maintaining optimal motor temperature and ensuring reliable motor operation.
Selecting the Right Cooling Method for Your Motor
Choosing the right cooling method for your electric motor is crucial to ensure optimal performance, reliability, and longevity. Each cooling method has its advantages and considerations, and the selection should be based on various factors specific to your motor and application. Here are some key considerations when choosing a cooling method:
- Motor Power Rating: The power rating of your motor is an essential factor to consider. Higher power motors typically generate more heat and may require more robust cooling methods, such as liquid cooling or forced cooling, to effectively dissipate the heat.
- Operating Environment: The operating environment plays a significant role in determining the appropriate cooling method. Consider factors such as ambient temperature, humidity, dust or debris levels, and the presence of any corrosive or hazardous substances. High-temperature environments or environments with restricted airflow may necessitate the use of active cooling methods, such as forced cooling.
- Cooling Requirement: Assess the specific cooling requirements of your motor. Consider the desired operating temperature range, the level of heat generation, and the acceptable temperature rise during operation. This will help determine the cooling capacity needed and the suitability of various cooling methods.
- Reliability Requirements: Evaluate the level of reliability required for your application. Critical or high-reliability applications may necessitate more sophisticated cooling methods, such as liquid cooling. On the other hand, applications with lower reliability requirements may be adequately served by simpler passive cooling techniques.
- Space Constraints: Consider the available space for the motor and cooling system. Some cooling methods, such as liquid cooling, may require additional components and infrastructure, which may not be feasible in applications with limited space. In such cases, compact cooling methods like air cooling or passive cooling techniques may be more suitable.
- Budget Considerations: Take into account your budget and cost constraints when selecting a cooling method. Active cooling methods, such as forced air or liquid cooling, may involve higher initial costs due to equipment, installation, and maintenance requirements, while passive cooling methods are generally more cost-effective.
- Maintenance and Serviceability: Evaluate the maintenance and serviceability aspect of the cooling system. Some cooling methods may require regular maintenance, such as cleaning of fans or blowers, replacing coolant, or inspecting heat exchangers. Consider the availability of resources and expertise for maintenance when selecting a cooling method.
It is also crucial to consult with experts or engineers specialized in motor cooling to help you evaluate your specific requirements and recommend the most suitable cooling method. They can provide valuable insights and assist in the design and implementation of the cooling solution to ensure optimal performance and longevity for your motor.
Remember that selecting the right cooling method for your motor is not a one-size-fits-all approach. Careful evaluation of the motor’s characteristics, operating conditions, and application requirements will guide you towards an effective cooling solution that promotes efficient heat dissipation and helps maintain optimal motor performance.
Read more: How Much Is a Fan Motor for an AC Unit
Common Cooling Challenges and Solutions
While implementing a cooling method for an electric motor, various challenges can arise that impact the effectiveness of cooling and may compromise motor performance. Understanding and addressing these common cooling challenges is essential to ensure proper cooling and reliable motor operation. Here are some of the most common cooling challenges and their solutions:
- Insufficient Cooling Capacity: In some cases, the cooling method in use may not provide sufficient cooling capacity to dissipate the heat generated by the motor. To address this challenge, you can consider upgrading to a more efficient cooling method, such as moving from air cooling to liquid cooling or implementing forced cooling techniques to enhance heat dissipation. Additionally, optimizing the design and placement of cooling elements, such as fans or heat sinks, can also improve cooling capacity.
- Thermal Hotspots: Thermal hotspots occur when certain areas of the motor experience higher temperatures than others. This can lead to localized heat buildup and potential damage to motor components. To mitigate thermal hotspots, thermal management techniques such as using heat sinks, redistributing airflow, or implementing targeted cooling methods can be employed. Thermal imaging or temperature monitoring can help identify hotspots and guide the implementation of appropriate cooling measures.
- Inadequate Heat Dissipation: Heat dissipation may be inadequate if the motor’s cooling system is not designed or maintained properly. Regular maintenance and cleaning of cooling components, such as fans or heat sinks, can ensure proper airflow and heat transfer. Additionally, optimizing the motor’s enclosure design by providing ventilation openings or improving internal airflow can enhance heat dissipation. Proper cooling system design and sizing based on the motor’s heat generation characteristics are essential to ensure effective heat dissipation.
- Contamination and Blockages: Contaminants or blockages in the cooling system can hinder proper cooling. Dust, debris, or mineral buildup on cooling surfaces or within channels can impede heat transfer and airflow. Regular cleaning and inspection of cooling components, especially in forced cooling systems, are necessary to prevent blockages and maintain optimal cooling efficiency. Using filters or implementing suitable preventive measures can help minimize the risk of contamination.
- Coolant Leakage: Leakage of coolant in liquid cooling systems can occur, causing inefficient cooling and potentially damaging the motor. Check for any leaks or signs of coolant loss regularly to address and repair them promptly. Ensuring proper sealing, using quality coolant, and conducting routine maintenance and inspections can help prevent coolant leakage.
- Excessive Noise: Some cooling methods, particularly those involving fans or blowers, can generate significant noise levels. This can be a concern in noise-sensitive environments. Implementing noise reduction measures such as using quieter fans, incorporating sound insulation, or optimizing fan placement can help mitigate excessive noise without compromising cooling efficiency.
It is important to tailor the solutions to address the specific cooling challenges faced in your motor and application. Consulting with experts or engineers specializing in motor cooling can provide valuable insights and recommendations to efficiently overcome cooling challenges and ensure reliable motor operation.
Regular monitoring, maintenance, and optimization of the cooling system are essential to address cooling challenges effectively and maximize the lifespan and performance of the electric motor.
Conclusion
Proper cooling of an electric motor is crucial for maintaining optimal performance, reliability, and longevity. Without effective cooling methods in place, motors can experience reduced efficiency, accelerated wear and tear, and even premature failure. Selecting the right cooling method depends on various factors such as motor power rating, operating environment, cooling requirements, and budget constraints.
Air cooling, the most common cooling method, relies on natural convection or forced airflow to dissipate heat. It is cost-effective and suitable for many applications. Liquid cooling, on the other hand, provides higher cooling capacity and precise temperature control. It is often used in high-performance motors or applications with stringent cooling requirements. Forced cooling methods, including forced air cooling and forced liquid cooling, enhance heat transfer and are ideal for enclosed environments or situations with limited natural airflow.
Passive cooling techniques, such as the use of heat sinks, thermal insulation, and natural convection, are effective for smaller motors or applications with lower heat generation. They offer simplicity, reliability, and cost-effectiveness. However, they may have limitations in high-temperature environments or applications with higher cooling requirements.
When selecting a cooling method, it is important to address common cooling challenges such as insufficient cooling capacity, thermal hotspots, inadequate heat dissipation, contamination or blockages, coolant leakage, and excessive noise. Regular maintenance, cleaning, and optimization of the cooling system help overcome these challenges and ensure effective heat dissipation.
In conclusion, proper cooling is essential in maximizing the performance, reliability, and lifespan of electric motors. Understanding the various cooling methods available, considering application requirements, and addressing common cooling challenges will help select and implement the most suitable cooling method for your motor, ensuring optimal motor operation and minimizing the risks associated with overheating.
Frequently Asked Questions about How To Cool An Electric Motor
Was this page helpful?
At Storables.com, we guarantee accurate and reliable information. Our content, validated by Expert Board Contributors, is crafted following stringent Editorial Policies. We're committed to providing you with well-researched, expert-backed insights for all your informational needs.
0 thoughts on “How To Cool An Electric Motor”