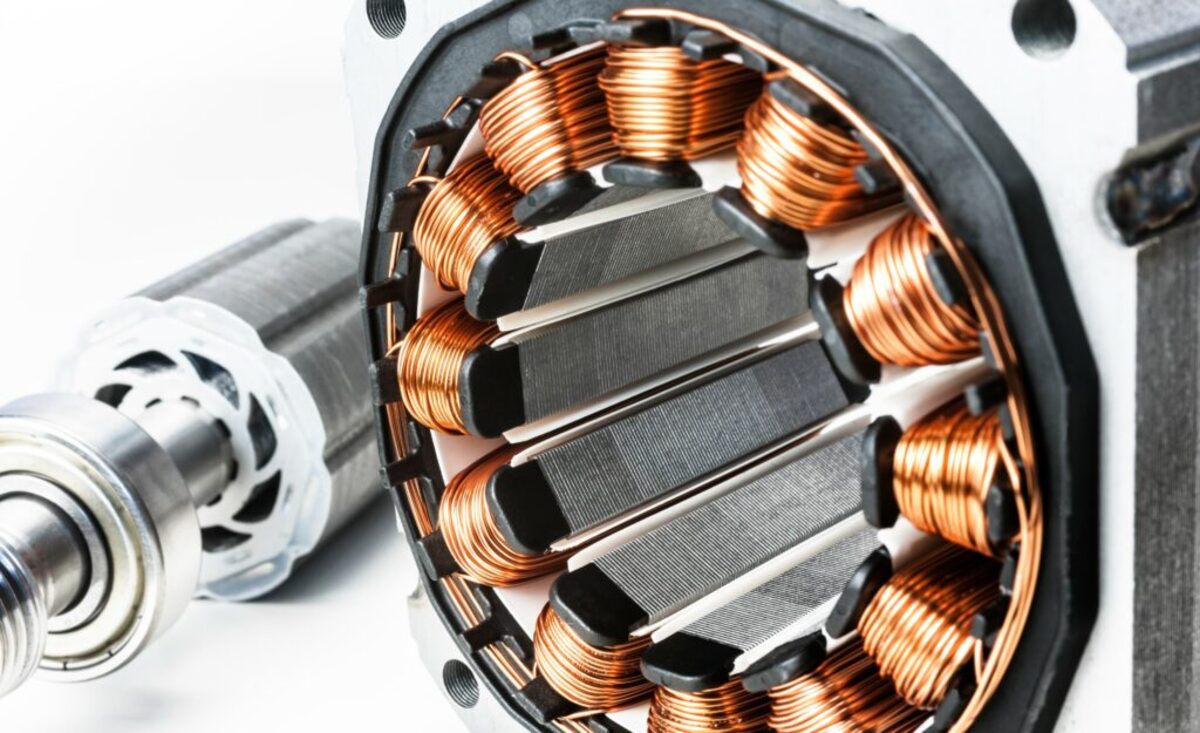
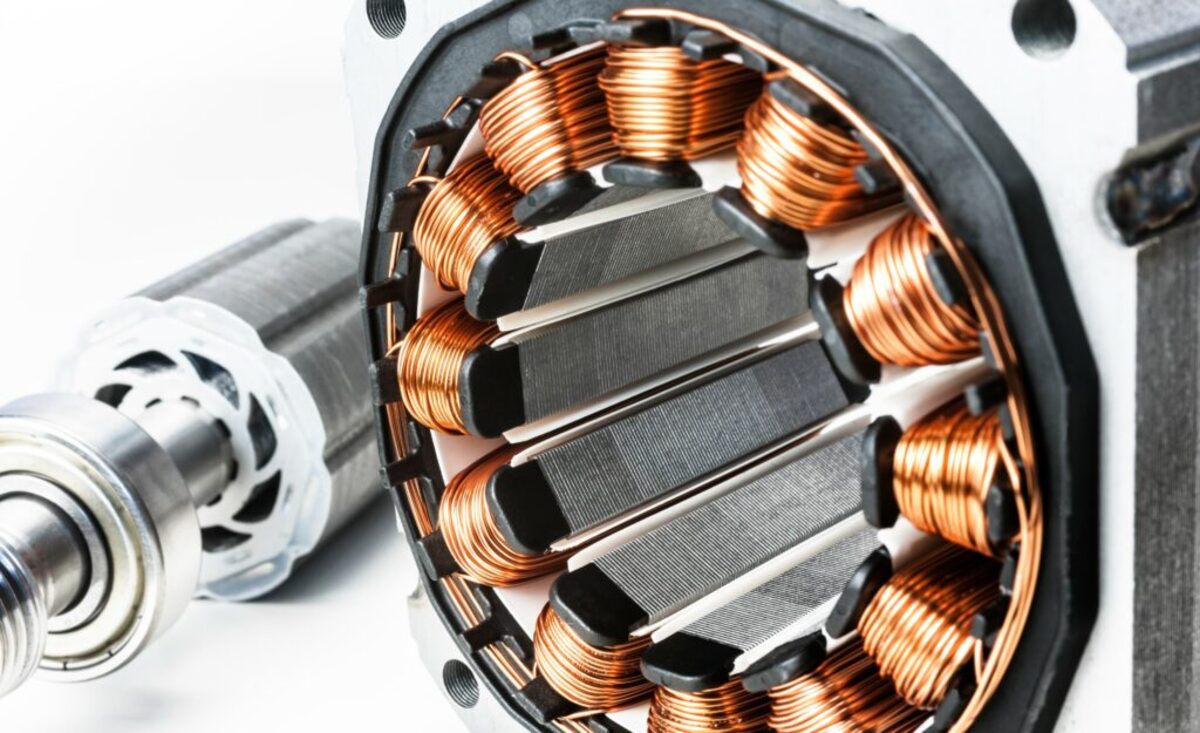
Articles
How To Slow Down An Electric Motor
Modified: January 19, 2024
Discover effective techniques and tips on how to slow down an electric motor in this comprehensive article. Improve your knowledge and skills with our insightful articles on motor control and maintenance.
(Many of the links in this article redirect to a specific reviewed product. Your purchase of these products through affiliate links helps to generate commission for Storables.com, at no extra cost. Learn more)
Introduction
Electric motors have become an indispensable part of our everyday lives. From powering industrial machinery to driving household appliances, these motors play a crucial role in various applications. However, there may be instances when you need to slow down the speed of an electric motor. Whether it’s to reduce wear and tear, improve efficiency, or meet specific operational requirements, knowing how to slow down an electric motor can be a valuable skill.
In this article, we will delve into the world of electric motors and explore the causes of high motor speed. We will also discuss various techniques that can be used to slow down an electric motor effectively. By understanding these methods, you can ensure optimal performance and longevity of your motor-driven equipment.
Key Takeaways:
- Slowing down an electric motor can be achieved through methods such as adjusting voltage, changing gear ratios, using VFDs, or installing motor speed controllers. Each method offers unique benefits and considerations for optimal motor performance.
- Understanding the causes of high motor speed and employing the right technique to slow down the motor is crucial for optimizing performance, extending lifespan, and meeting specific application needs. Safety and professional guidance are essential in implementing these methods.
Read more: How To Slow Down Infill On Active Print
Understanding Electric Motors
Before we dive into the techniques of slowing down electric motors, it’s essential to have a basic understanding of how these motors work. Electric motors are devices that convert electrical energy into mechanical energy, making them ideal for powering various mechanical systems. They operate based on the principles of electromagnetism.
Electric motors consist of several components, including a stator, rotor, and a power source. The stator is a stationary part of the motor and contains coils of wire, known as windings, which are connected to an electrical power supply. The rotor, on the other hand, is the rotating part of the motor and is connected to the mechanical load.
When electric current flows through the windings of the stator, it produces a magnetic field. This magnetic field interacts with the magnetic field produced by the rotor, causing the rotor to move. As a result, mechanical energy is generated, and the motor starts rotating.
Electric motors come in various types, such as AC (alternating current) motors and DC (direct current) motors. AC motors are widely used due to their simplicity, reliability, and wide availability. They are commonly found in household appliances, HVAC systems, and industrial machinery. DC motors, on the other hand, are often used in applications that require precise speed control, such as robotics and electric vehicles.
Now that we have a basic understanding of electric motors, let’s explore the common causes of high motor speed and why it may be necessary to slow them down.
Causes of High Motor Speed
High motor speed can occur due to several factors. Understanding these causes is crucial in determining the appropriate method to slow down an electric motor. Here are some common reasons why a motor may be operating at an undesirably high speed:
- Incorrect voltage: The motor may be receiving a higher voltage than what it is designed for. This can lead to an increase in motor speed beyond the desired range.
- Improper gear ratio: In some cases, the motor may be connected to a mechanical system with an inappropriate gear ratio. This can result in the motor rotating at a higher speed than desired.
- Malfunctioning motor controller: Faulty motor controllers can cause the motor to operate at higher speeds due to incorrect signal processing or control settings.
- External load changes: Sometimes, changes in the load being driven by the motor can cause an increase in speed. This can occur when the load decreases suddenly, causing the motor to spin faster.
It is important to identify the precise cause of the high motor speed before taking any corrective actions. This can be done through careful observation, inspection of the motor and associated components, and consultation with experts if needed.
Now that we have a clear understanding of the causes of high motor speed, let’s explore various techniques that can be employed to slow down an electric motor effectively.
Techniques to Slow Down an Electric Motor
Slowing down an electric motor requires employing the right technique based on the specific situation and motor characteristics. Here are four commonly used methods for slowing down an electric motor:
- Method 1: Adjusting Voltage: One of the simplest and most effective ways to control motor speed is by adjusting the voltage. By reducing the voltage, the motor’s speed can be decreased. This can be achieved by using a transformer or a voltage regulator. However, it is essential to ensure that the voltage is adjusted within the motor’s specified operating range to prevent damage.
- Method 2: Changing Gear Ratio: If the motor is connected to a mechanical system with gears, changing the gear ratio can alter the speed. By increasing the gear ratio, the motor’s rotational speed can be decreased. Conversely, decreasing the gear ratio will increase the speed. This method requires careful calculation and selection of the appropriate gears to achieve the desired speed reduction.
- Method 3: Using Variable Frequency Drives (VFD): A variable frequency drive, also known as a VFD or an adjustable speed drive, allows precise control of motor speed. VFDs can adjust the frequency and voltage supplied to the motor, enabling smooth and continuous speed regulation. This method is particularly useful in applications that require frequent or precise speed changes, such as in industrial processes.
- Method 4: Installing Motor Speed Controllers: Motor speed controllers, such as rheostats or electronic speed controllers, provide a means to adjust and regulate motor speed. These controllers work by varying the amount of current supplied to the motor, thus controlling its speed. They are commonly used in applications where constant speed adjustments are necessary, like in power tools and small appliances.
Each of these techniques has its advantages and considerations. It is important to assess the specific requirements of the motor and the application to determine the most suitable method for slowing down the motor’s speed.
Now that we have explored various techniques to slow down an electric motor, let’s conclude our discussion.
Method 1: Adjusting Voltage
Adjusting the voltage is a straightforward and effective method to slow down an electric motor. By reducing the voltage supplied to the motor, its speed can be decreased. However, it’s important to note that this method should be implemented within the motor’s specified operating range to prevent damage.
To adjust the voltage, you can use a transformer or a voltage regulator. These devices allow you to decrease the incoming voltage, thereby reducing the motor’s speed. It’s important to ensure that the voltage is adjusted gradually and in increments to avoid sudden changes that could harm the motor or the connected equipment.
When adjusting the voltage, it’s essential to consider the characteristics of the motor. Some motors are designed to operate within a specific voltage range, and straying too far from this range can cause inefficiency or even motor failure. It’s advisable to consult the motor’s documentation or seek professional advice to ensure that the voltage adjustment falls within safe limits.
It’s also worth noting that reducing the voltage may cause a decrease in torque. This can be a disadvantage in situations where high torque is required, such as lifting heavy loads. However, in applications where precise speed control is more important than torque, adjusting the voltage can be an effective solution.
Overall, adjusting the voltage is a simple and cost-effective method to slow down an electric motor. By carefully considering the motor’s operating range and making gradual voltage adjustments, you can achieve the desired decrease in motor speed without compromising its performance or longevity.
Now that we have explored the first method of adjusting voltage to slow down an electric motor, let’s move on to the next technique.
To slow down an electric motor, you can use a variable frequency drive (VFD) to control the speed by adjusting the frequency of the electrical supply to the motor. This allows for precise and efficient speed control.
Read more: How To Build A Electric Motor
Method 2: Changing Gear Ratio
Changing the gear ratio is another effective method to slow down an electric motor. This technique is particularly useful when the motor is connected to a mechanical system with gears, such as in vehicles or industrial machinery.
The gear ratio refers to the ratio of the number of teeth on the driven gear to the number of teeth on the driving gear. By modifying the gear ratio, you can alter the speed of the motor output. Increasing the gear ratio will result in a decrease in the motor speed, while decreasing the gear ratio will increase the speed.
To change the gear ratio, you need to select gears with different numbers of teeth. For example, if you want to decrease the motor speed, you can replace the current driving gear with one that has more teeth, or replace the driven gear with one that has fewer teeth. This change in gear ratio will cause the motor to rotate at a slower speed.
It’s important to note that when changing the gear ratio, you should consider the torque requirements of the connected load. Increasing the gear ratio may reduce the torque available at the output, which could impact the system’s overall performance. Therefore, it’s crucial to calculate and select the appropriate gear ratio that balances the desired speed reduction and torque requirements.
In some cases, it may be necessary to consult an expert or refer to the motor or equipment documentation to determine the suitable gear ratio changes. They can provide guidance on the optimal gear ratios to achieve the desired speed reduction while maintaining the necessary torque levels.
Changing the gear ratio is a reliable and widely used method to slow down an electric motor. By selecting the appropriate gears and correctly altering the gear ratio, you can achieve the desired reduction in motor speed for various applications.
Now that we have explored the second method of changing gear ratio to slow down an electric motor, let’s move on to the next technique.
Method 3: Using Variable Frequency Drives (VFD)
Variable Frequency Drives (VFDs), also known as adjustable speed drives, provide precise control over motor speed by varying both the frequency and voltage supplied to the motor. This method is particularly useful in applications where frequent or precise speed changes are required.
VFDs operate by converting the incoming AC power into DC power, then converting it back to a controlled AC output with adjustable frequency and voltage. By changing the frequency and voltage, the VFD can control the motor’s rotational speed.
Using a VFD to slow down an electric motor offers several advantages. Firstly, it allows for smooth and continuous speed regulation without the need for mechanical adjustments or gear changes. This can be beneficial in applications where precise speed control is essential, such as in industrial processes or HVAC systems.
Additionally, VFDs provide other features such as torque control and soft start/stop functions. Torque control enables precise control over the motor’s torque output, which can be useful in applications with varying load requirements. Soft start/stop functions gradually ramp up or down the motor’s speed, reducing mechanical stress and prolonging the motor’s lifespan.
When using a VFD, it’s important to select a drive that is compatible with the motor’s specifications and power requirements. Proper installation and programming are crucial to ensure the VFD is set up correctly for the motor and the specific application. Consulting with an experienced electrician or motor technician is recommended to ensure optimal performance and safe operation.
While VFDs offer excellent control over motor speed, it’s important to note that they can be more expensive compared to other methods. However, the benefits they provide in terms of precise speed control and additional features often outweigh the cost factor in applications that require frequent speed adjustments.
Overall, using a Variable Frequency Drive (VFD) is a highly effective method to slow down an electric motor, providing precise speed control and additional features. When correctly implemented, a VFD can optimize motor performance, increase energy efficiency, and extend the motor’s lifespan.
Now, let’s move on to the final method of slowing down an electric motor.
Method 4: Installing Motor Speed Controllers
Installing motor speed controllers is another technique to effectively slow down an electric motor. Motor speed controllers, such as rheostats or electronic speed controllers, provide a means to adjust and regulate the motor’s speed by varying the amount of current supplied to it.
Rheostats, also known as variable resistors, are a traditional type of motor speed controller. They work by inserting a variable resistance into the motor circuit. By adjusting the resistance, the current flowing through the motor can be controlled, leading to a change in the motor’s rotational speed. However, it’s important to note that rheostats are less efficient compared to other speed control methods and can cause energy wastage in the form of heat.
Electronic speed controllers (ESCs) are a more modern and efficient type of motor speed controller. They use electronic circuits and pulse-width modulation (PWM) techniques to control the motor’s speed. ESCs offer precise speed control and are commonly used in applications such as RC vehicles, drones, and certain industrial machinery.
When installing motor speed controllers, it’s crucial to select a controller that is compatible with the motor’s specifications and power requirements. The controller should be able to handle the voltage and current levels of the motor to ensure safe and reliable operation.
Proper wiring and installation are essential for motor speed controllers. It’s recommended to follow the manufacturer’s instructions or consult with a professional electrician to ensure correct wiring and configuration of the speed controller. This will ensure optimal performance and prevent any potential hazards.
Motor speed controllers provide the advantage of allowing precise and continuous speed adjustments as per the application’s requirements. They are commonly used in power tools, small appliances, and other applications where constant speed adjustments are necessary.
While installing motor speed controllers can be more complex compared to other methods, their ability to provide fine-tuned speed control makes them a valuable tool for slowing down an electric motor.
Now that we have explored the fourth method of installing motor speed controllers to slow down an electric motor, let’s summarize our discussion.
Conclusion
Slowing down an electric motor is a task that may be required in various situations, whether to improve efficiency, reduce wear and tear, or meet specific operational requirements. By understanding the underlying principles of electric motors and the causes of high motor speed, you can employ the right techniques to effectively slow down the motor.
Throughout this article, we explored four common methods for slowing down an electric motor. Adjusting the voltage allows for a simple and cost-effective way to decrease motor speed, but it should be done within the motor’s specified operating range. Changing the gear ratio is another effective method, particularly useful in applications with gears, but careful consideration of torque requirements is necessary. Using Variable Frequency Drives (VFDs) provides precise speed control and additional features, making them suitable for applications that require frequent speed changes. Finally, installing motor speed controllers, such as rheostats or electronic speed controllers, offers continuous speed adjustments for applications that require constant speed variations.
When implementing these methods, it’s important to consider the specific requirements of the motor and the application. Consulting the motor’s documentation or seeking professional advice can help ensure the chosen technique is appropriate and falls within safe operating limits.
By effectively slowing down an electric motor, you can optimize performance, extend the motor’s lifespan, and meet the specific needs of your application. Whether it’s adjusting voltage, changing gear ratios, using VFDs, or installing motor speed controllers, you now have the knowledge to take control of the motor’s speed and achieve optimal results.
Remember, safety should always be a top priority when working with electric motors. If you are unsure or uncomfortable with making adjustments or installations, it’s best to seek assistance from a qualified professional to ensure the proper and safe operation of your motor.
So go ahead, put these techniques into practice, and unlock the full potential of your electric motor by slowing it down to suit your needs!
Frequently Asked Questions about How To Slow Down An Electric Motor
Was this page helpful?
At Storables.com, we guarantee accurate and reliable information. Our content, validated by Expert Board Contributors, is crafted following stringent Editorial Policies. We're committed to providing you with well-researched, expert-backed insights for all your informational needs.
0 thoughts on “How To Slow Down An Electric Motor”