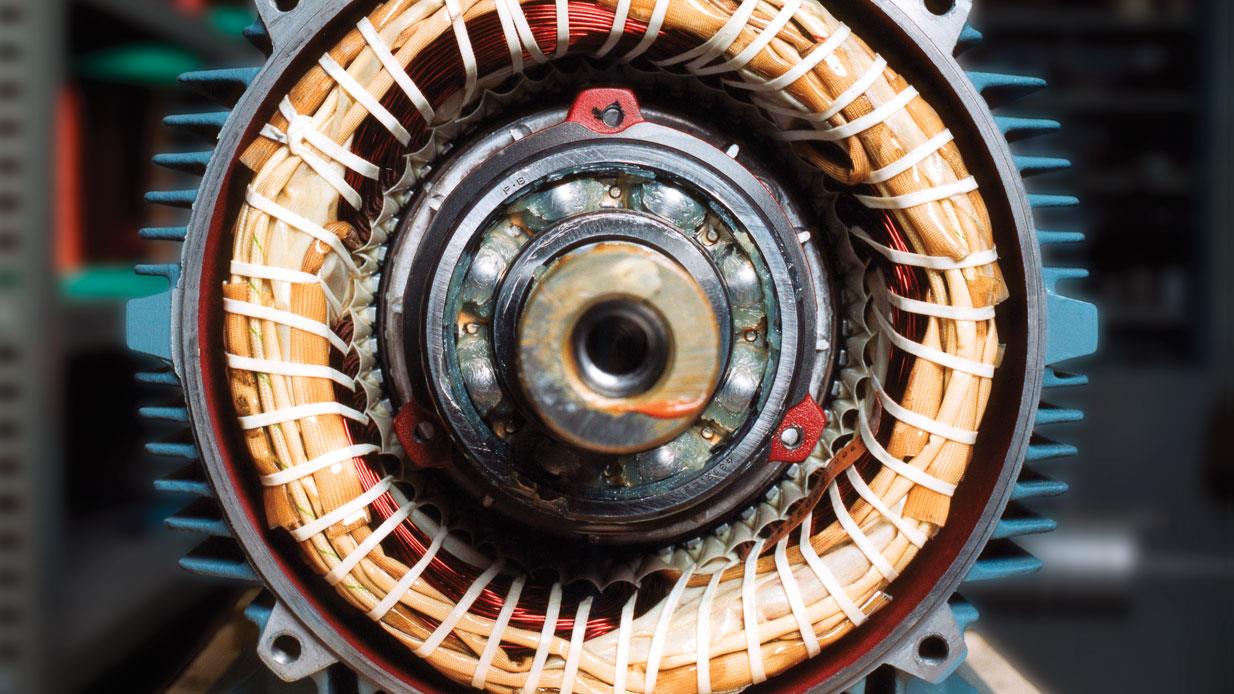
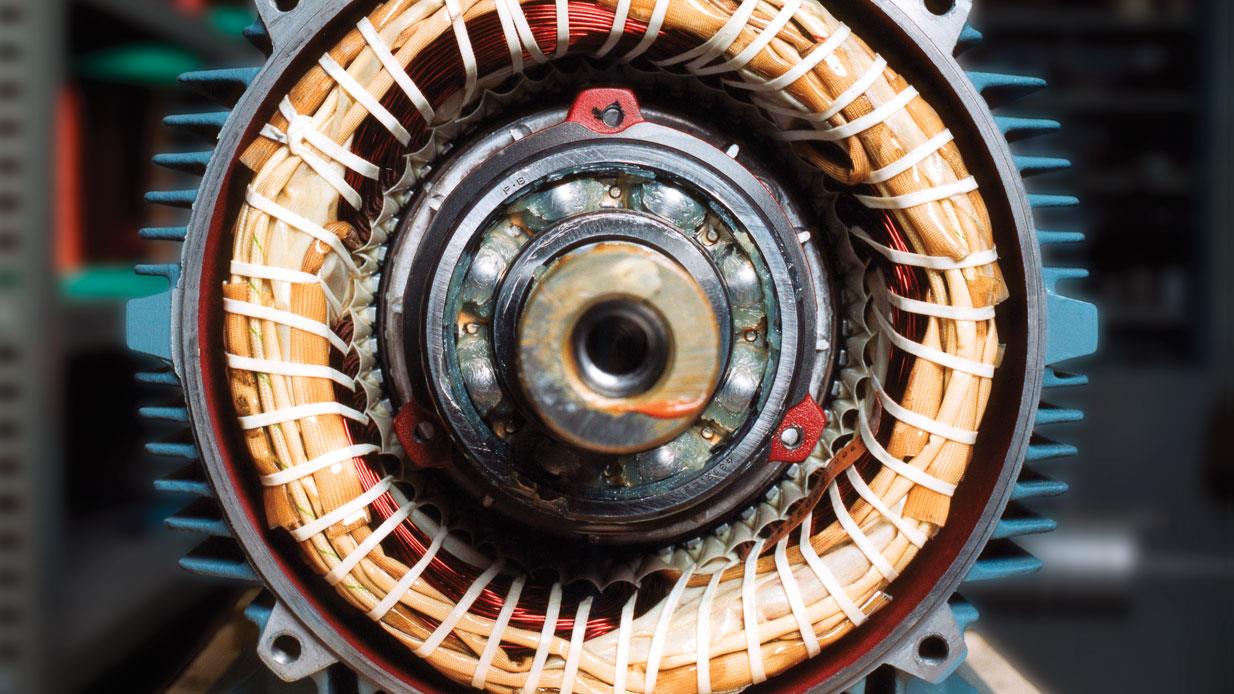
Articles
How Efficient Is An Electric Motor
Modified: August 27, 2024
Discover the efficiency of electric motors in our informative articles. Learn how electric motors are revolutionizing various industries.
(Many of the links in this article redirect to a specific reviewed product. Your purchase of these products through affiliate links helps to generate commission for Storables.com, at no extra cost. Learn more)
Introduction
An electric motor is a device that converts electrical energy into mechanical energy, making it an essential component in a wide range of applications such as industrial machinery, household appliances, and electric vehicles. Unlike traditional internal combustion engines, electric motors offer several advantages, including higher efficiency, lower emissions, and quieter operation.
Understanding the efficiency of electric motors is crucial in today’s energy-conscious world. Efficient motors not only reduce energy consumption but also contribute to cost savings and environmental sustainability. This article explores the efficiency of electric motors, the factors that affect it, and the importance of improving motor efficiency.
Electric motors rely on the interaction between magnetic fields and electric currents to produce motion. When an electric current passes through a coil inside the motor, it creates a magnetic field. This magnetic field interacts with the permanent magnets or electromagnets inside the motor, resulting in a rotational force and mechanical motion.
The efficiency of an electric motor refers to the ratio of useful work output to the electrical energy input. It is expressed as a percentage, with higher efficiency indicating a greater proportion of electrical energy converted into mechanical work. By maximizing motor efficiency, energy losses can be minimized, enhancing overall system performance.
Key Takeaways:
- Electric motors play a crucial role in various applications, and understanding their efficiency is key to reducing energy consumption, lowering costs, and promoting environmental sustainability.
- Factors such as motor design, operating conditions, and maintenance significantly influence motor efficiency. Selecting high-efficiency motors, proper maintenance, and advanced control techniques are essential for optimizing motor performance.
Read more: How To Build A Electric Motor
How Electric Motors Work
To understand how electric motors work, it’s important to grasp the basic principles of electromagnetism. When an electric current flows through a wire, it generates a magnetic field around the wire. In an electric motor, this principle is harnessed to create rotational motion.
Electric motors typically consist of several key components. First, there are the stationary parts, including the stator and the housing. The stator is the outer part of the motor that contains the coils or windings. These windings are made up of insulated copper wire and are arranged in a specific pattern to create a rotating magnetic field.
Inside the stator, you’ll find the rotor, which is the moving part of the motor. The rotor is the component that actually spins and drives the machinery. It is typically made up of a series of magnets, either permanent magnets or electromagnets, arranged in a specific configuration.
When electrical power is supplied to the motor, it flows through the windings in the stator, creating a magnetic field. This magnetic field then interacts with the magnets on the rotor, causing the rotor to rotate. The rotation of the rotor produces the mechanical energy required to perform work.
Controlling the speed of an electric motor is achieved by varying the electrical input. By adjusting the voltage and the current, the speed of the motor can be regulated. Additionally, varying the configuration of the windings and the arrangement of the magnets on the rotor can also impact the motor’s speed and torque.
Overall, the operation of an electric motor relies on the principles of electromagnetism and the interaction between magnetic fields and electric currents to produce rotational motion. Through careful design and control, electric motors can be optimized for specific applications, delivering efficient and reliable performance.
Efficiency of Electric Motors
The efficiency of an electric motor is a crucial metric that determines how effectively it converts electrical energy into mechanical work. A higher efficiency motor means less wasted energy and more power available for useful work.
Motor efficiency is typically expressed as a percentage and can range from around 50% to over 95% for modern, high-efficiency motors. The efficiency of electric motors is affected by various factors, including design, manufacturing quality, and operating conditions.
One of the key factors that affect motor efficiency is the type of motor. There are several types of electric motors, including brushed DC motors, brushless DC motors, induction motors, and synchronous motors. Each type has its advantages and disadvantages in terms of efficiency and performance.
Modern brushless DC motors and permanent magnet synchronous motors are known for their high efficiency. These motors use permanent magnets to create the magnetic field on the rotor, eliminating the need for brushes and commutators found in brushed DC motors. As a result, they experience lower energy losses and achieve higher efficiency.
Operating conditions also play a significant role in motor efficiency. Factors such as temperature, load, and speed can impact the efficiency of the motor. It is important to operate the motor within its rated parameters to ensure optimal efficiency. Overloading or operating the motor at extreme temperatures can lead to increased energy losses and reduced efficiency.
Maintenance and proper lubrication of the motor also contribute to its efficiency. Regular maintenance, including cleaning, lubrication, and bearing replacement, helps to reduce friction and improve overall motor performance. A well-maintained motor operates more efficiently and has a longer lifespan.
Additionally, motor efficiency can be influenced by the electrical system it is connected to. Voltage level, power quality, and wiring configurations can impact the overall efficiency of the motor. It is important to analyze the electrical system to ensure proper voltage regulation and minimize power losses.
In summary, the efficiency of an electric motor is determined by its design, manufacturing quality, operating conditions, and the electrical system it is connected to. By selecting high-efficiency motor types, maintaining the motor properly, and considering the operating conditions, it is possible to optimize the efficiency of electric motors and maximize their performance.
Factors Affecting Motor Efficiency
The efficiency of an electric motor is influenced by a variety of factors. Understanding these factors can help in selecting the right motor for a specific application and optimizing its performance. Here are some key factors that affect motor efficiency:
- Motor Design: The design of the motor itself plays a significant role in determining its efficiency. Factors such as the type of motor, the materials used, and the arrangement of the windings and magnets all impact efficiency. Modern motor designs, such as brushless DC motors and permanent magnet synchronous motors, are known for their high efficiency.
- Motor Size: The size and power rating of the motor can affect its efficiency. Smaller motors tend to have higher efficiency as they have less internal resistance and can operate at higher speeds. However, it’s important to select a motor size that is suitable for the intended application to ensure optimal efficiency.
- Load: The load placed on the motor is a critical factor in determining its efficiency. Motors perform best when operating near their rated load. Overloading the motor can cause increased energy losses and reduced efficiency. It’s important to properly size the motor to match the load requirements of the application.
- Speed: The speed at which the motor operates can impact its efficiency. Motors are designed for optimal efficiency within a certain speed range. Running the motor at excessively low or high speeds can decrease efficiency. Selecting a motor with a speed rating that matches the desired operating speed can help maximize efficiency.
- Temperature: The temperature at which the motor operates can affect its efficiency. Motors have an optimal operating temperature range, and operating outside of this range can result in increased energy losses. Proper cooling and ventilation should be considered to maintain the motor at an optimal temperature for maximum efficiency.
- Power Quality: The quality of the electrical power supplied to the motor can impact its efficiency. Factors such as voltage level, harmonics, and power factor can affect energy losses within the motor. It’s important to ensure a stable power supply and address any power quality issues to maximize motor efficiency.
- Maintenance: Regular maintenance and proper lubrication are essential for maintaining motor efficiency. Dust, dirt, and lack of lubrication can increase friction and energy losses. Regular inspections, cleaning, and lubrication can help reduce these losses and improve motor efficiency.
By considering these factors and selecting a motor that aligns with the specific application requirements, it is possible to maximize motor efficiency and optimize overall system performance.
Energy Losses in Electric Motors
While electric motors are highly efficient at converting electrical energy into mechanical work, they still experience energy losses during operation. These losses can occur in various forms and significantly impact the overall efficiency of the motor. Understanding these energy losses is crucial for identifying areas of improvement and maximizing motor efficiency.
Here are some common types of energy losses in electric motors:
- Stator Copper Losses: When current flows through the stator windings, resistance causes energy losses in the form of heat. These losses, known as stator copper losses, are directly proportional to the square of the current flowing through the windings. Lower-resistance materials and efficient winding designs can help reduce these losses.
- Iron Core Losses: The iron core of the motor experiences energy losses due to hysteresis and eddy currents. Hysteresis losses occur as the magnetic core goes through cycles of magnetization and demagnetization. Eddy current losses arise from circulating currents induced in the core by the varying magnetic field. Using high-quality magnetic materials and lamination techniques can minimize these losses.
- Mechanical Friction and Windage Losses: The mechanical components of the motor, such as bearings and brushes (in brushed motors), can cause energy losses through friction. Additionally, the movement of the rotor through the air generates windage losses. Minimizing friction through proper lubrication and using efficient bearing designs can help reduce these losses.
- Rotor Copper Losses: In motors that have windings on the rotor, such as wound rotor induction motors, there are energy losses due to the resistance of the rotor windings. These losses increase with the square of the rotor current. Utilizing materials with lower resistance and optimizing the rotor design can decrease these losses.
- Stray Load Losses: Stray load losses refer to losses that occur in other parts of the motor, such as the electromagnetic field outside the core. These losses are influenced by factors such as the coil design and the proximity of other conductive materials. Careful design and shielding techniques can help minimize stray load losses.
- Inverter or Drive Losses: In motors that are driven by electronic inverters or drives, there are additional losses in the power conversion process. These losses result from the switching of power transistors and the generation of harmonics in the output waveform. Selecting high-efficiency drives and optimizing the drive setup can help reduce these losses.
By understanding and addressing these energy losses, it is possible to improve the overall efficiency of electric motors. Manufacturers are continually working on developing more efficient motor designs and incorporating advanced technologies to minimize energy losses and enhance motor performance.
Regular maintenance, such as keeping the motor clean and well-lubricated, can help improve the efficiency and lifespan of an electric motor.
Read more: How To Clean An Electric Motor
Calculating Motor Efficiency
Calculating the efficiency of an electric motor is a straightforward process that requires collecting some essential data about the motor’s input and output power. The efficiency of a motor is determined by the ratio of the useful work output to the electrical energy input.
Here’s how you can calculate the efficiency of an electric motor:
- Step 1: Collect Input Power Data: Start by measuring the electrical power input to the motor. This can be done by using a power meter or directly measuring the voltage and current supplied to the motor. Note down the values of voltage (V) and current (I) in the input circuit.
- Step 2: Calculate Input Power: Calculate the input power (Pin) by multiplying the voltage (V) by the current (I). This gives you the total electrical power supplied to the motor.
- Step 3: Collect Output Power Data: Next, measure the mechanical output power of the motor. This can be done by connecting a dynamometer or load to the motor shaft and measuring the torque (T) and rotational speed (N) of the motor. Note down the values of torque (T) and rotational speed (N).
- Step 4: Calculate Output Power: Calculate the output power (Pout) by multiplying the torque (T) by the rotational speed (N). This gives you the mechanical power output of the motor.
- Step 5: Calculate Efficiency: Finally, calculate the efficiency of the motor by dividing the output power (Pout) by the input power (Pin) and multiplying by 100 to obtain the result as a percentage: Efficiency = (Pout / Pin) x 100
It’s important to note that these calculations provide an approximation of the motor’s efficiency and do not account for losses in the motor control system or other external factors. However, this method gives a good indication of the motor’s overall efficiency.
Keep in mind that motor efficiency can vary depending on the load and operating conditions. To obtain a more accurate efficiency measurement, multiple readings can be taken at different load and speed points, and an average efficiency can be calculated.
Motor manufacturers often provide efficiency specifications for their motors, making it easier to select a motor that meets specific efficiency requirements. Higher efficiency motors may have a higher upfront cost but can result in significant energy savings over the motor’s lifetime, making them a worthwhile investment.
Importance of Motor Efficiency
The efficiency of electric motors plays a vital role in various industries and applications. Understanding the importance of motor efficiency is essential for optimizing energy usage, reducing costs, and promoting sustainability. Here are some key reasons why motor efficiency is crucial:
- Energy Conservation: Electric motors consume a significant amount of electrical energy worldwide. By improving motor efficiency, energy consumption can be reduced, resulting in lower energy bills and decreased reliance on fossil fuels. This is especially important as sustainability and environmental concerns continue to grow.
- Reduced Operating Costs: High-efficiency motors may have a higher upfront cost, but they can lead to significant cost savings in the long run. By minimizing energy losses and maximizing the conversion of electrical energy into useful work, efficient motors reduce overall operating costs. This is particularly relevant in industries with heavy motor usage, such as manufacturing or HVAC systems.
- Environmental Impact: Motor efficiency directly impacts carbon emissions and environmental footprints. By using energy more efficiently, fewer greenhouse gases are released, contributing to the fight against climate change. Increased motor efficiency aligns with global efforts to reduce carbon emissions and move towards cleaner and more sustainable energy sources.
- Legal and Regulatory Requirements: Many countries and regions have implemented energy efficiency regulations and standards that mandate the use of high-efficiency motors. Compliance with these regulations is crucial for businesses to avoid penalties and legal consequences. Choosing efficient motors ensures adherence to these requirements.
- Improved System Performance: Efficient motors not only consume less energy but also operate more reliably and effectively. They generate less heat and experience fewer energy losses, resulting in improved motor performance, reliability, and longevity. This translates to less downtime, reduced maintenance costs, and higher productivity for industries that rely on motor-driven machinery.
- Technological Advancements: Advancements in motor technology continue to push the boundaries of efficiency. Manufacturers are constantly innovating and developing more efficient motor designs, materials, and control systems. Investing in high-efficiency motors allows businesses to take advantage of the latest technological advancements and stay at the forefront of energy efficiency.
Motor efficiency is a key aspect of energy management and sustainability initiatives in both commercial and residential settings. By selecting and utilizing efficient motors, businesses can reduce their environmental impact, save on operating costs, and contribute to a more sustainable future.
Improving Motor Efficiency
Improving motor efficiency is a goal for many industries and businesses seeking to optimize energy usage and reduce operating costs. Here are some effective strategies and practices to enhance motor efficiency:
- Select High-Efficiency Motors: One of the most straightforward ways to improve motor efficiency is to choose motors that are designed for high efficiency. Look for motors that have a high efficiency rating and are labeled with energy efficiency certification such as NEMA or IE ratings. These motors are specifically designed to minimize energy losses and maximize performance.
- Right-Size the Motor: Ensure that the motor size matches the requirements of the application. Oversized motors not only consume more energy but may also operate inefficiently at lighter loads. By selecting a motor with the appropriate horsepower and torque rating, energy losses can be minimized, leading to improved efficiency.
- Proper Motor Maintenance: Regular motor maintenance is essential for maintaining optimum efficiency. Keep the motor clean and inspect it periodically for any signs of wear and tear. Replace worn-out parts such as bearings or brushes promptly to minimize friction and energy losses. Additionally, ensure that the motor is properly lubricated as inadequate lubrication can lead to increased energy losses due to friction.
- Optimize Motor Control: Utilize advanced motor control techniques to enhance motor efficiency. Variable Frequency Drives (VFDs) or electronic motor controllers can control the speed and torque of the motor, matching it with the required load. This can prevent energy losses associated with constant speed operation, especially in applications with varying load demand.
- Harmonics Mitigation: Implement measures to mitigate power quality issues such as harmonics. Harmonics in the electrical supply can cause increased energy losses in motors and decrease overall efficiency. Use harmonic filters or power conditioning equipment to reduce the impact of harmonics on the motor and maintain optimal motor performance.
- Efficient System Design: Consider the entire system when designing motor-driven applications. Optimize the overall system design to minimize energy losses, such as using proper wire sizing and insulation materials to reduce voltage drops. Ensure that the motor is correctly matched with the load to avoid overloading and inefficiencies.
- Employee Training and Awareness: Educate employees on the importance of motor efficiency and energy conservation. Promote energy-saving practices such as turning off motors when not in use, optimizing motor start-stop cycles, and promoting energy-efficient behaviors. Increasing employee awareness and involvement can lead to significant energy savings and improved motor efficiency.
Improving motor efficiency is a continuous process that requires evaluation, monitoring, and implementation of energy-efficient practices. By adopting these strategies and staying updated with the latest motor efficiency technologies, businesses can achieve significant energy savings, reduce operating costs, and contribute to a greener and more sustainable future.
Conclusion
Understanding and prioritizing motor efficiency is critical for businesses and industries looking to optimize energy consumption, reduce costs, and promote sustainability. Electric motors are used in a wide range of applications, making their efficiency crucial for overall system performance. By maximizing motor efficiency, businesses can achieve substantial energy savings while minimizing environmental impact.
We have explored the various aspects of motor efficiency, including how electric motors work, factors influencing efficiency, energy losses, and methods for calculating and improving motor efficiency. It is clear that motor efficiency is influenced by numerous factors, such as motor design, load, operating conditions, and maintenance. Each of these factors must be carefully considered to ensure optimal motor performance.
Efficient motors not only consume less energy, but they also operate more reliably, improving system performance and reducing downtime. They contribute to cost savings by minimizing energy losses and reducing operating expenses. Additionally, using high-efficiency motors aligns with regulatory requirements and demonstrates a commitment to sustainability and environmental responsibility.
To improve motor efficiency, it is important to select high-efficiency motors that are suitable for the specific application and load requirements. Regular maintenance, proper lubrication, and monitoring of operating conditions are also crucial to ensure optimal motor efficiency over time. Employing advanced motor control techniques, addressing power quality issues, and optimizing system design further contribute to improving motor efficiency.
Enhancing motor efficiency is a continuous process that requires a proactive approach, ongoing monitoring, and employee awareness. By implementing energy-saving practices and fostering a culture of energy efficiency, businesses can make significant strides in reducing energy consumption and promoting sustainability.
In conclusion, investing in high-efficiency motors and adopting energy-efficient practices not only benefits the bottom line but also helps create a greener and more sustainable future. By prioritizing motor efficiency, businesses can contribute to energy conservation, cost reduction, and a healthier environment for generations to come.
Frequently Asked Questions about How Efficient Is An Electric Motor
Was this page helpful?
At Storables.com, we guarantee accurate and reliable information. Our content, validated by Expert Board Contributors, is crafted following stringent Editorial Policies. We're committed to providing you with well-researched, expert-backed insights for all your informational needs.
0 thoughts on “How Efficient Is An Electric Motor”